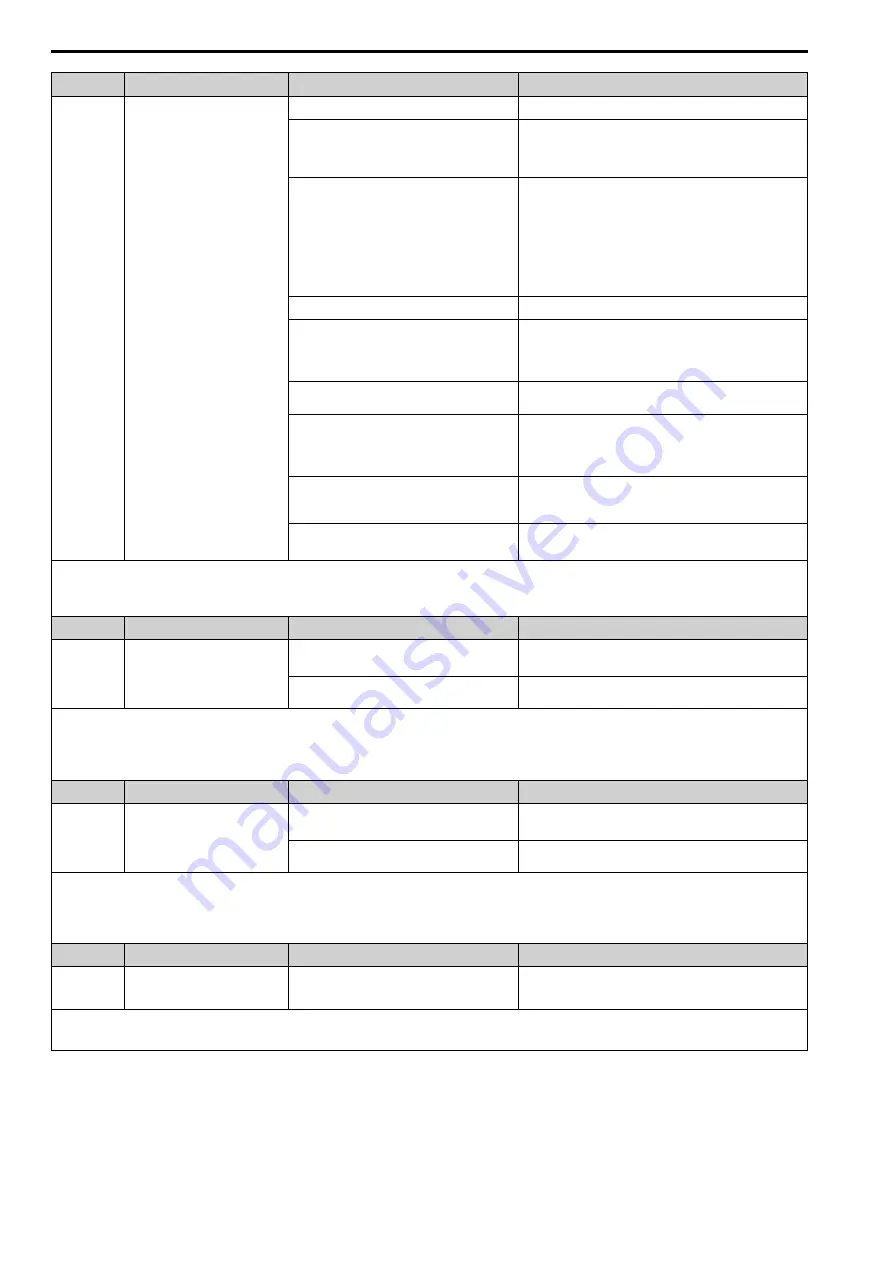
232
SIEPCYEUOQ2V01A Q2V Technical Manual
Code
Name
Causes
Possible Solutions
oL2
Drive Overload
The load is too large.
Decrease the load.
The acceleration/deceleration times or cycle times
are too short.
•
Examine the acceleration/deceleration times and the motor
start/stop frequencies (cycle times).
•
Increase the values set in
C1-01 to C1-08 [Acceleration/
Deceleration Times]
.
The V/f pattern does not fit the motor qualities.
•
Examine the ratios between the V/f pattern frequency and
voltage. Decrease the voltage if it is too high compared to the
frequency.
•
Adjust
E1-04 to E1-10 [V/f Pattern Parameters]
. Decrease the
values set in
E1-08 [Mid A Voltage]
and
E1-10 [Min Output
Voltage]
. For motor 2, adjust
E3-04 to E3-10
.
Note:
If the values set in
E1-08
and
E1-10
are too low, the overload
tolerance will decrease at low speeds.
The drive capacity is too small.
Replace the drive with a larger capacity model.
Overload occurred while running at low speed.
•
Decrease the load when running at low speed.
•
Replace the drive with a larger capacity model.
•
Decrease the value set in
C6-02 [Carrier Frequency
Selection]
.
The torque compensation gain is too large.
Decrease the value set in
C4-01 [Trq Comp Gain]
to make sure
that the motor does not stall.
The speed search-related parameters are set
incorrectly.
•
Examine the settings for all speed search-related parameters.
•
Adjust
b3-03 [SpSrch Deceleration Time]
.
•
Set
b3-24 = 1 [SpSrch Method Selection = Speed Estimation]
after Auto-Tuning.
Phase loss in the input power supply is causing the
output current to change.
•
Correct errors with the wiring for main circuit drive input
power.
•
Make sure that there is no phase loss, and repair problems.
Overload occurred during overexcitation
deceleration.
•
Decrease the value set in
n3-13 [OverExcBr Gain]
.
•
Decrease the value set in
n3-21 [OverExcBr Current Level]
.
Note:
•
The drive detects this fault if the electronic thermal protector of the drive started the drive overload protection.
•
Do a Fault Reset to clear the fault.
•
L5-07 [OL1-4 Auto-Reset Select]
disables the Auto Restart function.
Code
Name
Causes
Possible Solutions
oL3
Overtorque Detection 1
A fault occurred on the machine.
Example: The machine is locked.
Examine the machine and remove the cause of the fault.
The parameters are incorrect for the load.
Adjust
L6-02 [Trq Det1 Level]
and
L6-03 [Trq Det1 Time]
settings.
Note:
•
The drive detects this fault if the drive output current is more than the level set in
L6-02
for longer than
L6-03
.
•
Do a Fault Reset to clear the fault.
•
If the drive detects this fault, it will operate the motor as specified by the Stopping Method set in
L6-01 [Trq Det1 Select]
.
•
L5-07 [OL1-4 Auto-Reset Select]
disables the Auto Restart function.
Code
Name
Causes
Possible Solutions
oL4
Overtorque Detection 2
A fault occurred on the machine.
Example: The machine is locked.
Examine the machine and remove the cause of the fault.
The parameters are incorrect for the load.
Adjust
L6-05 [Trq Det2 Level]
and
L6-06 [Trq Det2 Time]
settings.
Note:
•
The drive detects this fault if the drive output current is more than the level set in
L6-05
for longer than
L6-06
.
•
Do a Fault Reset to clear the fault.
•
If the drive detects this fault, it will operate the motor as specified by the Stopping Method set in
L6-04 [Trq Det2 Select]
.
•
L5-07 [OL1-4 Auto-Reset Select]
disables the Auto Restart function.
Code
Name
Causes
Possible Solutions
oL5
Mechanical Weakening Detection 1
The drive detected overtorque as specified by the
conditions for mechanical weakening detection set
in
L6-08 [MechF Enable]
.
Do a deterioration diagnostic test on the machine side.
Note:
•
Do a Fault Reset to clear the fault.
•
If the drive detects this fault, it will operate the motor as specified by the Stopping Method set in
L6-08
.
Содержание Q2V Series
Страница 2: ...This Page Intentionally Blank 2 SIEPCYEUOQ2V01A Q2V Technical Manual...
Страница 12: ...12 SIEPCYEUOQ2V01A Q2V Technical Manual...
Страница 18: ...i 2 Legal Information 18 SIEPCYEUOQ2V01A Q2V Technical Manual...
Страница 26: ...1 2 Features and Advantages of Control Methods 26 SIEPCYEUOQ2V01A Q2V Technical Manual...
Страница 38: ...2 8 Installation Methods 38 SIEPCYEUOQ2V01A Q2V Technical Manual...
Страница 70: ...3 3 Main Circuit Wiring 70 SIEPCYEUOQ2V01A Q2V Technical Manual Models B006 B012...
Страница 102: ...3 17 Motor Application Precautions 102 SIEPCYEUOQ2V01A Q2V Technical Manual...
Страница 138: ...4 12 Test Run Checklist 138 SIEPCYEUOQ2V01A Q2V Technical Manual...
Страница 143: ...Standards Compliance 5 5 2 European Standards SIEPCYEUOQ2V01A Q2V Technical Manual 143 EU Declaration of Conformity...
Страница 144: ...5 2 European Standards 144 SIEPCYEUOQ2V01A Q2V Technical Manual...
Страница 145: ...Standards Compliance 5 5 2 European Standards SIEPCYEUOQ2V01A Q2V Technical Manual 145...
Страница 146: ...5 2 European Standards 146 SIEPCYEUOQ2V01A Q2V Technical Manual...
Страница 266: ...7 10 Troubleshooting Without Fault Display 266 SIEPCYEUOQ2V01A Q2V Technical Manual...
Страница 284: ...8 6 Storage Guidelines 284 SIEPCYEUOQ2V01A Q2V Technical Manual...
Страница 312: ...10 10 Peripheral Devices and Options 312 SIEPCYEUOQ2V01A Q2V Technical Manual...
Страница 430: ...11 21 Parameters Changed by PM Motor Code Selection 430 SIEPCYEUOQ2V01A Q2V Technical Manual...
Страница 731: ...SIEPCYEUOQ2V01A Q2V Technical Manual 731 Z Z pulse Auto Tuning 125...
Страница 733: ...SIEPCYEUOQ2V01A Q2V Technical Manual 733...