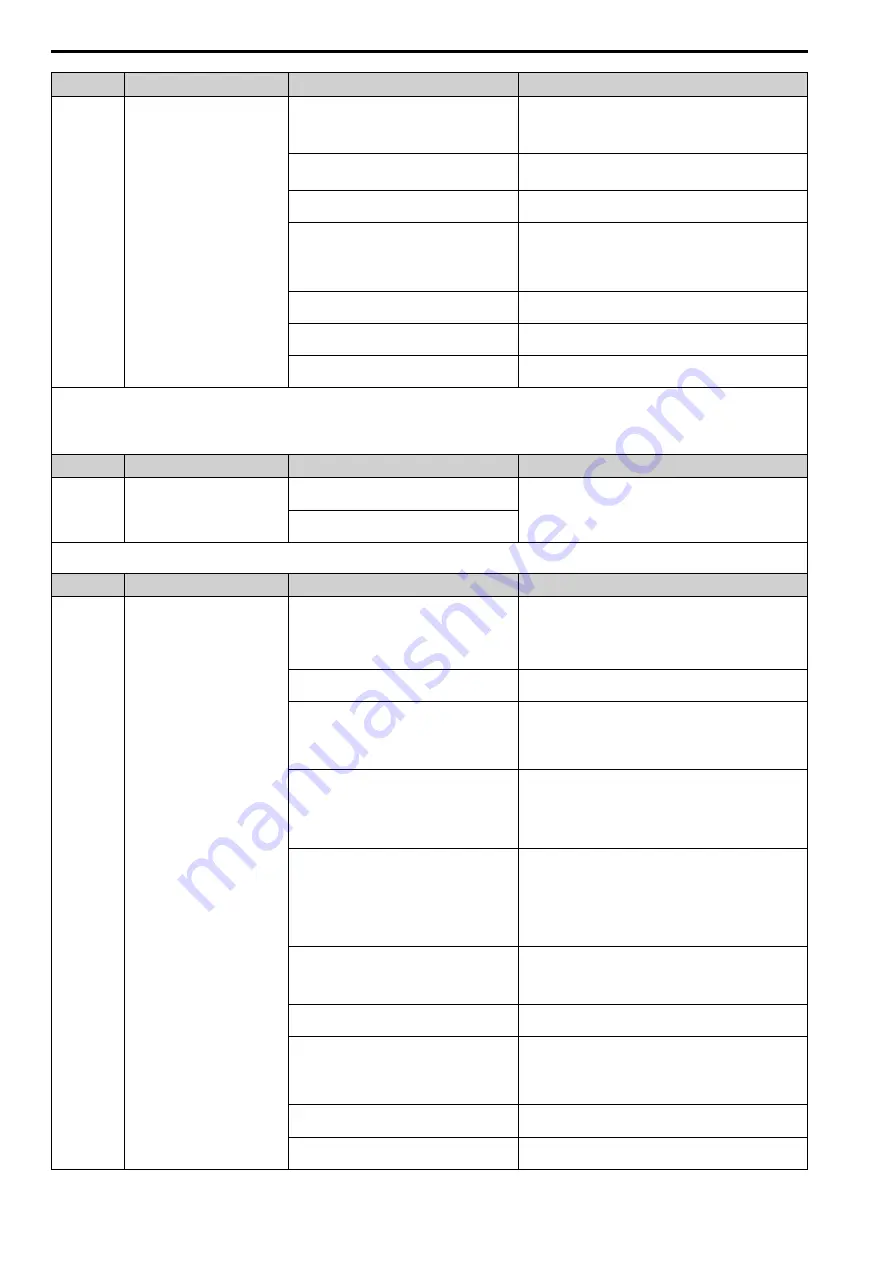
228
SIEPCYEUOQ2V01A Q2V Technical Manual
Code
Name
Causes
Possible Solutions
LSo
Low Speed Motor Step-Out
The motor code set incorrectly.
•
Set
E5-01 [PM Mot Code Selection]
correctly as specified by
the motor.
•
For specialized motors, refer to the motor test report and set
E5-xx
correctly.
The load is too large.
•
Decrease the load.
•
Replace the drive and motor with larger capacity models.
An external force on the load side caused the motor
to move at start.
Find and repair problems on the load side that cause the motor to
rotate from the load side.
The drive incorrectly detected the motor magnetic
pole position.
•
Set
b3-01 = 1 [SpSrch@Start Selection = Enabled]
.
•
If the value for
U6-57 [PoleDis IdDifVal]
is lower than 819,
increase the value set in
n8-84 [Polarity Det Current]
. Consult
the motor manufacturer for information about maximum
setting values.
The setting of
n8-84 [Polarity Det Current]
is too
low.
Increase the n8-84 setting from the default. Consult the motor
manufacturer for information about maximum setting values.
Incorrect values set in
L8-93 [Lso Detect Time]
,
L8-
94 [Lso Detect Level]
, and
L8-95 [Lso Amount]
.
Increase the values set in
L8-93 to L8-95.
The drive incorrectly detected the motor magnetic
pole position.
If you are using an IPM motor, do High Frequency Injection
Auto-Tuning.
Note:
•
The drive detects this fault if it detects step-out while running at low speed.
•
Do a Fault Reset to clear the fault.
•
LSo
is a protective function that stops the motor and stops the reverse run if a motor without a motor code incorrectly detects the initial polarity. To quickly detect motor
reversal, decrease the values set in
L8-93
to
L8-95
to a range in which the drive does not malfunction.
Code
Name
Causes
Possible Solutions
nSE
Node Setup Error
The
H1-xx = 7E [Node Setup]
terminal was
activated during run.
The drive received a Run command while the Node
Setup function was active.
Stop the drive when the Node Setup function is in use.
Note:
Do a Fault Reset to clear the fault.
Code
Name
Causes
Possible Solutions
oC
Overcurrent
The load is too heavy.
•
Measure the current flowing into the motor.
•
Replace the drive with a larger capacity model if the current
value is more than the drive rated current.
•
Decrease the load or replace with a larger drive to prevent
sudden changes in the current level.
Overheating caused damage to the motor or the
motor insulation is not satisfactory.
Measure the motor insulation resistance, and replace the motor if
there is electrical conduction or unserviceable insulation.
The motor main circuit cable is contacting ground
to make a short circuit.
•
Examine the motor main circuit cable for damage, and repair
short circuits.
•
Measure the resistance between the motor main circuit cable
and the ground terminal. If there is electrical conduction,
replace the cable.
A short circuit or ground fault on the drive output
side caused damage to the output transistor of the
drive.
•
Make sure that there is not a short circuit in terminal B1 and
terminals U/T1, V/T2, and W/T3. Make sure that there is not a
short circuit in terminals - and terminals U/T1, V/T2, and W/
T3.
•
If there is a short circuit, contact the manufacturer or your
nearest sales representative.
The acceleration time is too short.
•
Calculate the torque necessary during acceleration related to
the load inertia and the specified acceleration time.
•
Increase the values set in
C1-01, C1-03, C1-05, or C1-07
[Acceleration Times]
to get the necessary torque.
•
Increase the values set in
C2-01 to C2-04 [S-Curve
Characteristics]
to get the necessary torque.
•
Replace the drive with a larger capacity model.
The drive is trying to operate a specialized motor or
a motor that is larger than the maximum applicable
motor output of the drive.
•
Examine the motor nameplate, the motor, and the drive to
make sure that the drive rated current is larger than the motor
rated current.
•
Replace the drive with a larger capacity model.
A magnetic contactor was switched at the output.
Set the operation sequence to not turn ON or OFF the magnetic
contactor while the drive is outputting voltage.
The V/f pattern settings are incorrect.
•
Examine the ratios between the V/f pattern frequency and
voltage. Decrease the voltage if it is too high compared to the
frequency.
•
Adjust
E1-04 to E1-10 [V/f Pattern Parameters]
. For motor 2,
adjust
E3-04 to E3-10
.
The torque compensation gain is too large.
Decrease the value set in
C4-01 [Trq Comp Gain]
to make sure
that the motor does not stall.
Electrical interference caused a problem.
Examine the control circuit lines, main circuit lines, and ground
wiring, and decrease the effects of electrical interference.
Содержание Q2V Series
Страница 2: ...This Page Intentionally Blank 2 SIEPCYEUOQ2V01A Q2V Technical Manual...
Страница 12: ...12 SIEPCYEUOQ2V01A Q2V Technical Manual...
Страница 18: ...i 2 Legal Information 18 SIEPCYEUOQ2V01A Q2V Technical Manual...
Страница 26: ...1 2 Features and Advantages of Control Methods 26 SIEPCYEUOQ2V01A Q2V Technical Manual...
Страница 38: ...2 8 Installation Methods 38 SIEPCYEUOQ2V01A Q2V Technical Manual...
Страница 70: ...3 3 Main Circuit Wiring 70 SIEPCYEUOQ2V01A Q2V Technical Manual Models B006 B012...
Страница 102: ...3 17 Motor Application Precautions 102 SIEPCYEUOQ2V01A Q2V Technical Manual...
Страница 138: ...4 12 Test Run Checklist 138 SIEPCYEUOQ2V01A Q2V Technical Manual...
Страница 143: ...Standards Compliance 5 5 2 European Standards SIEPCYEUOQ2V01A Q2V Technical Manual 143 EU Declaration of Conformity...
Страница 144: ...5 2 European Standards 144 SIEPCYEUOQ2V01A Q2V Technical Manual...
Страница 145: ...Standards Compliance 5 5 2 European Standards SIEPCYEUOQ2V01A Q2V Technical Manual 145...
Страница 146: ...5 2 European Standards 146 SIEPCYEUOQ2V01A Q2V Technical Manual...
Страница 266: ...7 10 Troubleshooting Without Fault Display 266 SIEPCYEUOQ2V01A Q2V Technical Manual...
Страница 284: ...8 6 Storage Guidelines 284 SIEPCYEUOQ2V01A Q2V Technical Manual...
Страница 312: ...10 10 Peripheral Devices and Options 312 SIEPCYEUOQ2V01A Q2V Technical Manual...
Страница 430: ...11 21 Parameters Changed by PM Motor Code Selection 430 SIEPCYEUOQ2V01A Q2V Technical Manual...
Страница 731: ...SIEPCYEUOQ2V01A Q2V Technical Manual 731 Z Z pulse Auto Tuning 125...
Страница 733: ...SIEPCYEUOQ2V01A Q2V Technical Manual 733...