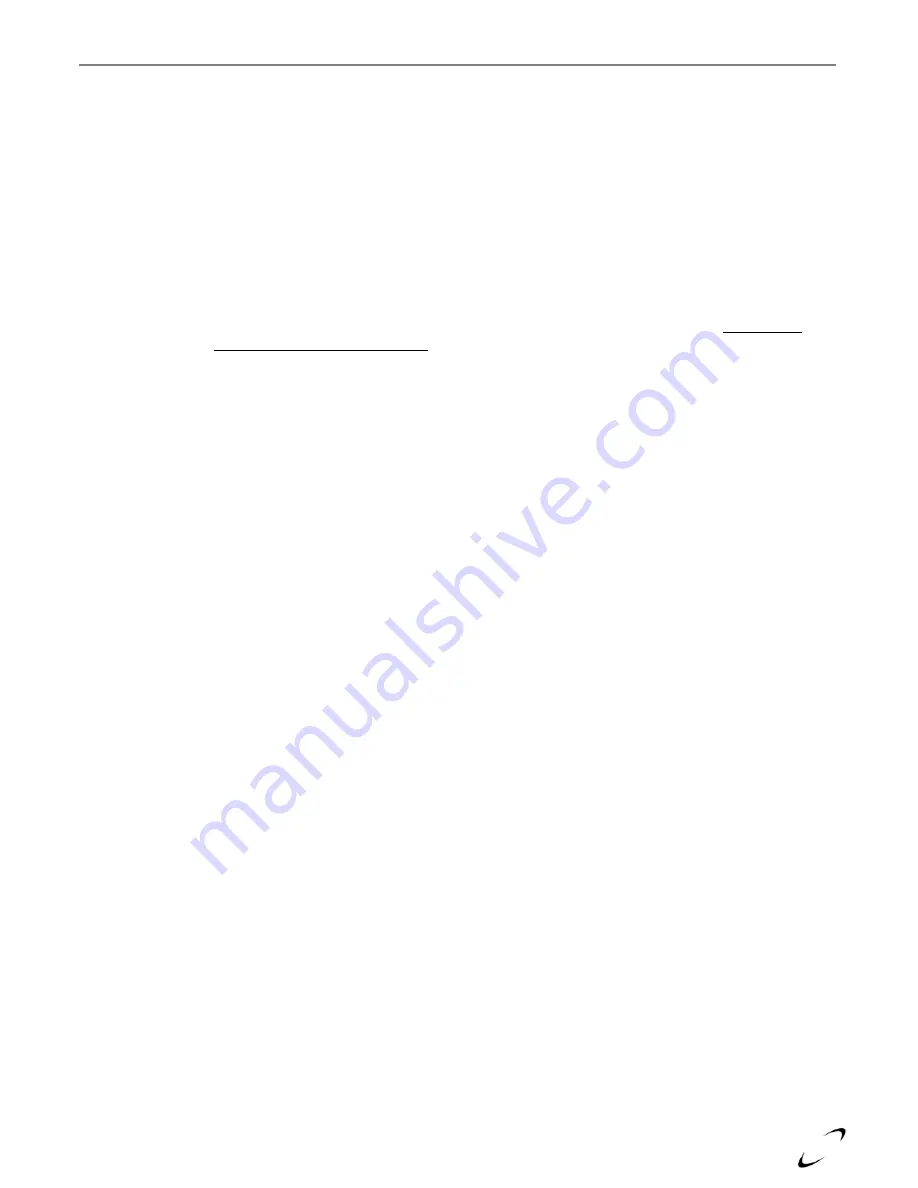
Ts Series Installation and Operation Instructions
│
Trinity Ts
15
Venting Rules and Guidelines
1.
Prevailing Winds:
Ensure the vent is located where it will not be exposed to normal prevailing winds.
2.
Combustion Air-Intake Contamination:
Air for combustion must be drawn from outdoors from an area
free of dust and contaminants. Combustion air containing chemicals such as chloride, fluoride, bromine or
iodine or dust and debris will cause corrosion damage of the heat exchanger voiding your NTI warranty.
Refer to Table 4-1 for a list of corrosive products and contaminants sources to avoid.
3.
Vertical Separation:
The exhaust must be a minimum of 18” [457 mm] above the air inlet, and the air inlet
must always be a minimum of 12” [305 mm] plus snow allowance above any surface that will support snow.
(Two feet plus snow allowance is highly recommended). Consult your weather office, for the maximum
typical snowfall for your region.
Example
: New Brunswick Canada - typical maximum snowfall is 19”, thus the inlet must be (12”+19”)
=
31” above grade and exhaust must be (31”+18”)
=
49” above grade.
4.
Horizontal Separation:
The horizontal distance between the inlet and exhaust must be a minimum of 4”
[102 mm] center to center. When the horizontal distance between the inlet and exhaust is greater than 12”
[305 mm], the difference in horizontal distance must be determined and the vertical separation increased by
the same amount.
Example:
The horizontal distance (HD)
=
24” [610 mm] and the vertical separation (VSmin)
=
18” [457
mm], the new vertical separation (VSnew) can be calculated using the following equation:
VSnew
=
(HD - 12”) + VS, where VSnew
=
(24” - 12”) + 18”
=
30”.
(If the horizontal distance is greater than 6’ [1.83 m], no additional vertical spacing is required. Vertical
separation is never required to be greater than 36” [915 mm].
5.
Wall Flashing:
Under normal operating conditions this boiler will produce a plume of white gases, and
should be taken into consideration when selecting an adequate location. A 36” [915 mm] diameter stainless,
plastic, or vinyl shield can be used to flash the exterior of the residence.
6.
Flue Gas Hazard:
Position the vent termination where vapors cannot make accidental contact with people
and pets or damage nearby shrubs and plants.
7.
Elbow Extensions:
Elbows on outside of wall must be no more than ½” [13 mm] away from the wall.
8.
Vent Sloping:
All indoor exhaust piping must be on a slope back to the boiler a minimum of ¼” per linear
foot of vent [6.25 mm per linear 305 mm]. For applications where excessive condensation is possible ½” per
linear foot [13 mm per linear 305 mm] is recommended.
9.
Vent Supports:
Where required Vent and Air-intake piping shall be secured to the wall for more rigidity.
All interior vent pipe shall be supported a minimum of every 36” [915 mm].
10.
Roof Exhaust:
In all roof applications the discharge must point away from the pitch of the roof.
11.
Roof Flashing:
Install adequate flashing where the pipe enters the roof, to prevent water leakage.
12.
Rain Cap:
Install and seal a rain cap over existing chimney openings, in vacant chimney applications.
13.
Venting Below Grade:
For installations that exit the wall below grade refer to Figure 4-9.
14.
Vent Screens:
Install factory supplied vent screens on the outside of the last elbow for both the inlet and
exhaust vent terminal elbows. Install the screen into the female opening of the elbow. Then cut a small piece
of pipe to sandwich the screen into the elbow. NOTE be sure that the small piece of pipe cut, does not
extend past the end of the elbow. Two screens are provided in the package. See Figures 4-6 and 4-7. Vent
screens are included in Optional Termination Kits.
15.
Pipe Sizing:
It is extremely important that the intake and exhaust vent piping be adapted to the appropriate
size immediately upon exiting the boiler cabinet. Refer to Figure 4-1 and Table 4-4.
16.
Condensate Hazard:
Do not locate vent over public walkways, driveways or parking lots. Condensate
could drip and freeze resulting in a slip hazard or damage to vehicles and machinery.
17.
Warning Plate:
Install the warning plate “Gas Vent Directly Below”, directly above (within 4 ft [1.22 m]
vertically) the location of the air inlet pipe, so it is visible from at least 8 ft [2.4 m] away. See Figure 4-16.
18.
Wall Thickness:
Direct vent terminations are designed to work with any standard wall thickness.
Installation guidelines for min/max wall thickness are as follows: Min.= 1” [25mm], Max.= 60” [1.52 m].
19.
Venting Options:
Due to potential moisture loading (build-up) along the exterior wall, sidewall venting
may not be the preferred venting option. Refer to Figures 4-2(b) and 4-3(b) for roof top venting options.
Содержание TRINITY Ts80
Страница 38: ...Trinity Ts Installation and Operation Instructions Ts Series 38 Figure 11 2 Ts80 Model Low Voltage Field Wiring...
Страница 40: ...Trinity Ts Installation and Operation Instructions Ts Series 40 Figure 12 1 b Ts80 Ladder Logic Diagram...
Страница 48: ...Trinity Ts Installation and Operation Instructions Ts Series 48 Figure 13 4 Diagnostic Mode Screens...
Страница 73: ...Ts Series Installation and Operation Instructions Trinity Ts 73 NOTES...
Страница 74: ...Trinity Ts Installation and Operation Instructions Ts Series 74 NOTES...
Страница 75: ...Ts Series Installation and Operation Instructions Trinity Ts 75 NOTES...