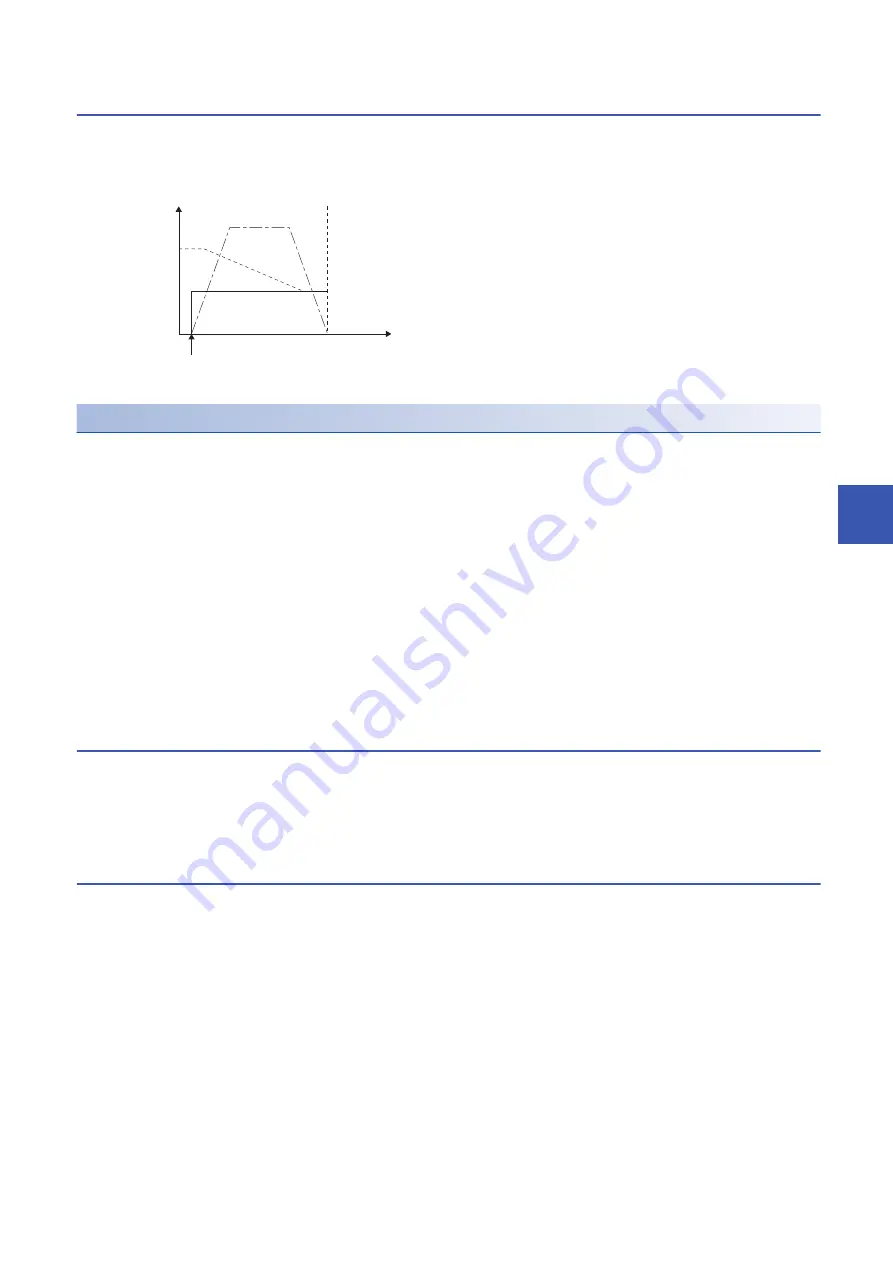
7 AUXILIARY AND APPLIED FUNCTIONS
7.7 Pressure Control
459
7
Pressure release operation
A servo program for pressure release operation is not necessary. Pressure profile data from the device specified with the
pressure control parameter "Pressure profile start device" is written to the device, and pressure release operation starts by
turning the pressure release startup device from OFF to ON. The speed limit value time constant can be set.
Processing details
• Pressure release operation starts by turning ON the pressure release startup device from the sequence program or Motion
SFC program. If the load cell pressure drops below the set pressure, the mode resets.
• When the deceleration start point of the speed limit value stop time constant to the end address is reached, deceleration
starts automatically. If the pressure release startup device is turned OFF at this time, a deceleration stop that uses the
speed limit value time constant is made.
• Pressure can be changed during pressure release operation. Speed and address cannot be changed during pressure
release operation.
• Feed/dwell operation cannot be executed during pressure release operation.
• When the required setting values at the startup of pressure release operation are outside the range, the pressure control
status device (pressure release (b3)) does not turn ON, and a minor error (error code: 19E1H) occurs.
• When the required setting values are changed to values outside the range during pressure release control, the setting
values are ignored, operation continues with the present setting values, and a warning (error code: 09E3H) occurs.
• "1" is stored in the execution point device of pressure release operation.
Operation by stroke limit
When the real current value exceeds the software stroke limit, a minor error (error code: 1993H, 1995H) occurs, and control
switches to positioning control.
Be sure to set a software stroke limit because the pressure control axis has modes that continue reversing due to a failure in
the load cell during pressure control.
Using point No. to substitute M-code
The execution point No. stores the execution step in a value converted to hexadecimal. Each step is displayed in bits, and
shifts left by 1 bit for every step advanced.
SE2
Load cell pressure
PR0
V0
Pressure release
operation startup
Mode reset
Содержание MELSEC iQ-R16MTCPU
Страница 1: ...MELSEC iQ R Motion Controller Programming Manual Positioning Control R16MTCPU R32MTCPU R64MTCPU ...
Страница 2: ......
Страница 477: ...APPENDICES Appendix 1 Processing Times of the Motion CPU 475 A MEMO ...
Страница 481: ......