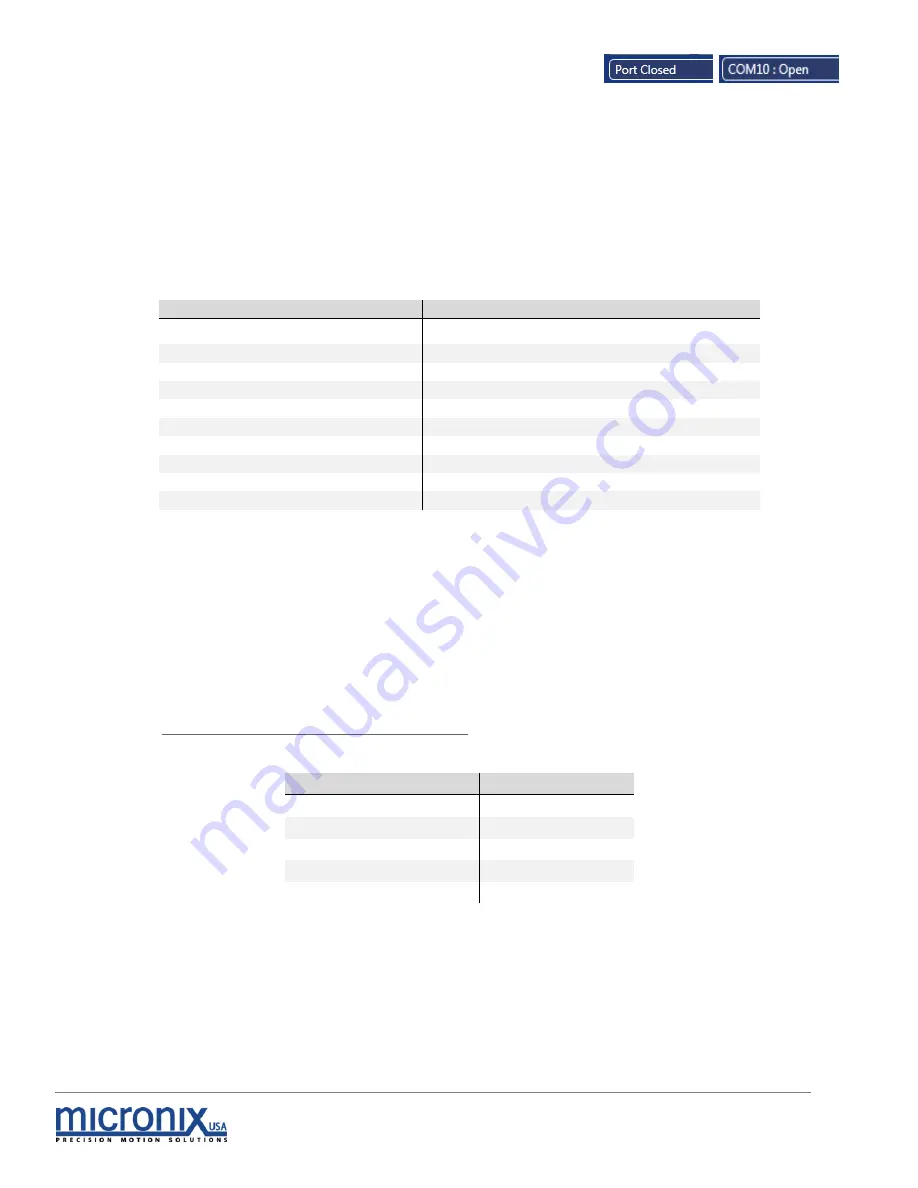
3-8
MICRONIX USA, LLC
www.micronixusa.com
Rev: 3.02
c.
The Port field should change to indicate the Port is Open
and the terminal should populate with some information about the system and then turn
blank. You are now ready to start moving a stage with your MMC-200. For more information
about this program see the MMC-100 MCP program guide.
2.
More information
–
more information about the MMC-100 MCP can be found in the MMC-100 MCP
program guide.
3.
Technical Information
3.1
MMC-200 Specifications
Parameter
Description
Axes
1 (stackable up to 99 axes)
Motor Type
Stepper motors
Interface
USB 2.0 compliant
Commands
ASCII Commands
Trajectory Mode
Trapezoidal velocity profile
Servo Clock
10 kHz
Trajectory Update
1 kHz
Power Supply
Regulated 24V DC (1A per module/axis*)
Enclosure Dimensions
145 x 85 x 25
Software Interface
MMC-200 MCP, LabVIEW
VI’s
*A single power supply may be used per stack. Each module/axis requires 1A maximum depending on the
type of motor it is driving, therefore add up Individual module amperages to determine the power supply
amperage requirement.
3.2
Serial Port Setup
If the MMC-200 is not automatically recognized by your computer, you will have to first install the
FTDI interface drivers before communicating with the controller. The drivers are supplied on the
supplemental CD under the folder
MMC-200 Drivers
or can be downloaded from:
http://www.ftdichip.com/Drivers/VCP.htm
Below are the virtual RS-232 configuration settings necessary for correct communication setup:
Software Parameter
Setting
Data Bits
8
Stop Bits
1
Parity
No
Handshake
No
Baud rate
38400
3.3
RJ11 RS485 Bus
The RS485 Intermodular RJ11 connector connects directly to the same Serial bus as the FTDI interface
above. The RS485 line needs a terminating resistor of
22kΩ or higher.
This connector can be used to
communicate with the MMC-100 in the place of the USB connection. For more on the RS-485
Intermodular RJ11 connector see the Appendix 6.4.
Содержание MMC-200 Series
Страница 1: ......