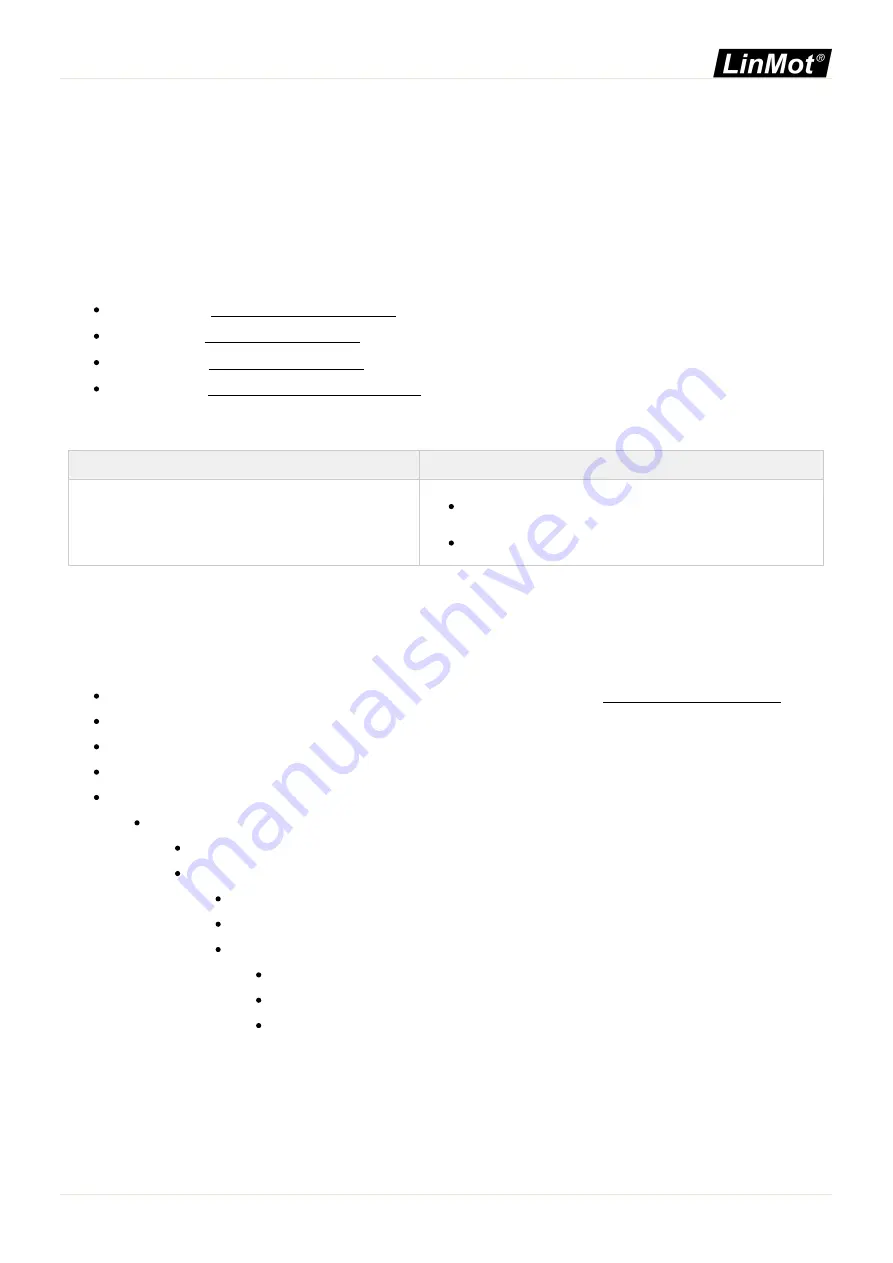
7.21.3.2 Deactivation
SLS shall only be deactivated if all possible request sources are inactive.
7.21.3.3 Fault Reaction
The fault reactions can be defined for each of the four instances of the SLS separately. All fault reactions behave as
described in the corresponding functional description:
SS2, see chapter,
7.19 - Safe Operating Stop (SOS)
7.21.4 Example for the Use
Example
Possible Solution
For setting up a machine, a machine operator must be able to
approach the machine by opening the protective door and
slowly move the machine with an acknowledgement button
nearby.
Configure and select the SLS function in the drive via safety
inputs or PROFIsafe.
The drive monitors safely the speed of the motor.
Table 88: SLS Example
7.21.5 Verification and Validation
The verification for the SLS function follows these steps:
Configure complete drive inclusive the SLS source and al parameters for SLS (7.21.1 - Parameters for SLS )
Validate the parameters on the drive.
Startup the drive.
Enable the motor.
For each configured speed limit check
activate SLS
Check reaction and status.
Move motor up to 50% of SLS speed limit. Start first test with this speed.
No error must occur.
Check the recorded safety speed to check the margin to the limit.
Setup the oscilloscope in LinMot-Talk to check the safety speed margin to the limit.
monitor Safe Speed Limit (UPID 1A2Ah)
monitor Safe Velocity (UPID 1A28h)
optionally monitor Safe Position (UPID 1A29h)
2S Drive Systems / 0185-1174_E_1V1_SM_C1251-2S / NTI AG
0185-1174_E_1V1_SM_C1251-2S / 2021-11-26 16:43 (Rev. 12500)
Page 131 of 150