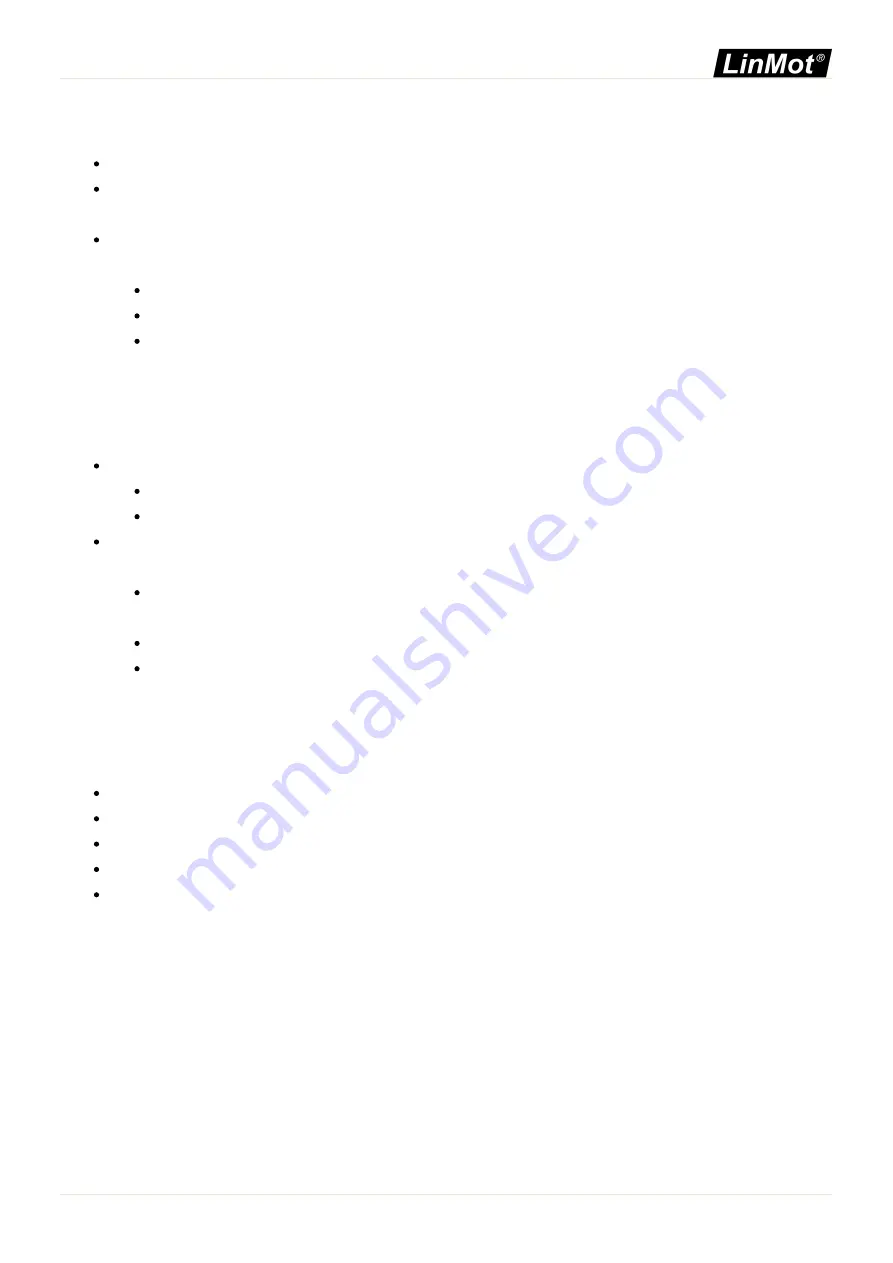
10.1.2 Requirements for the acceptance test
The machine is properly wired.
All safety equipment (such as protective door monitoring devices, light barriers, emergency limit switches) are
connected and ready for operation.
Commissioning of the position control must be completed, as e.g. the over-travel distance may otherwise change
as a result of a changed dynamic response of the drive control. These include, for example:
Configuration of the setpoint channel
Control in the higher-level controller
Configuration of the position controller
10.1.3 Acceptance Test
The acceptance test comprises 2 parts:
Checking whether the safety functions in the converter are correctly set:
Does the position control handle the configured application cases in the machine?
Do the set interface, times and monitoring functions match the configuration of the machine?
Checking whether the safety-relevant functions in the plant or machine function correctly. This part of the
acceptance test goes beyond the drive acceptance test:
Is all safety equipment such as protective door monitoring devices, light barriers or emergency-off switches
connected and ready for operation?
Does the higher-level control correctly respond to the safety-relevant feedback signals of the drive?
Do the drive settings match the configured safety-relevant function in the machine?
10.1.4 Documentation
The documentation consists of the following parts:
Description of the safety-relevant components and functions of the machine or plant.
Report of the acceptance test results.
Report of the settings of the safety functions (ASCII report) and configuration of safe address switches.
Complete drive configuration (readout by LinMot-Talk)
The documentation must be signed by the person who carried out the acceptance test.
2S Drive Systems / 0185-1174_E_1V1_SM_C1251-2S / NTI AG
0185-1174_E_1V1_SM_C1251-2S / 2021-11-26 16:43 (Rev. 12500)
Page 142 of 150