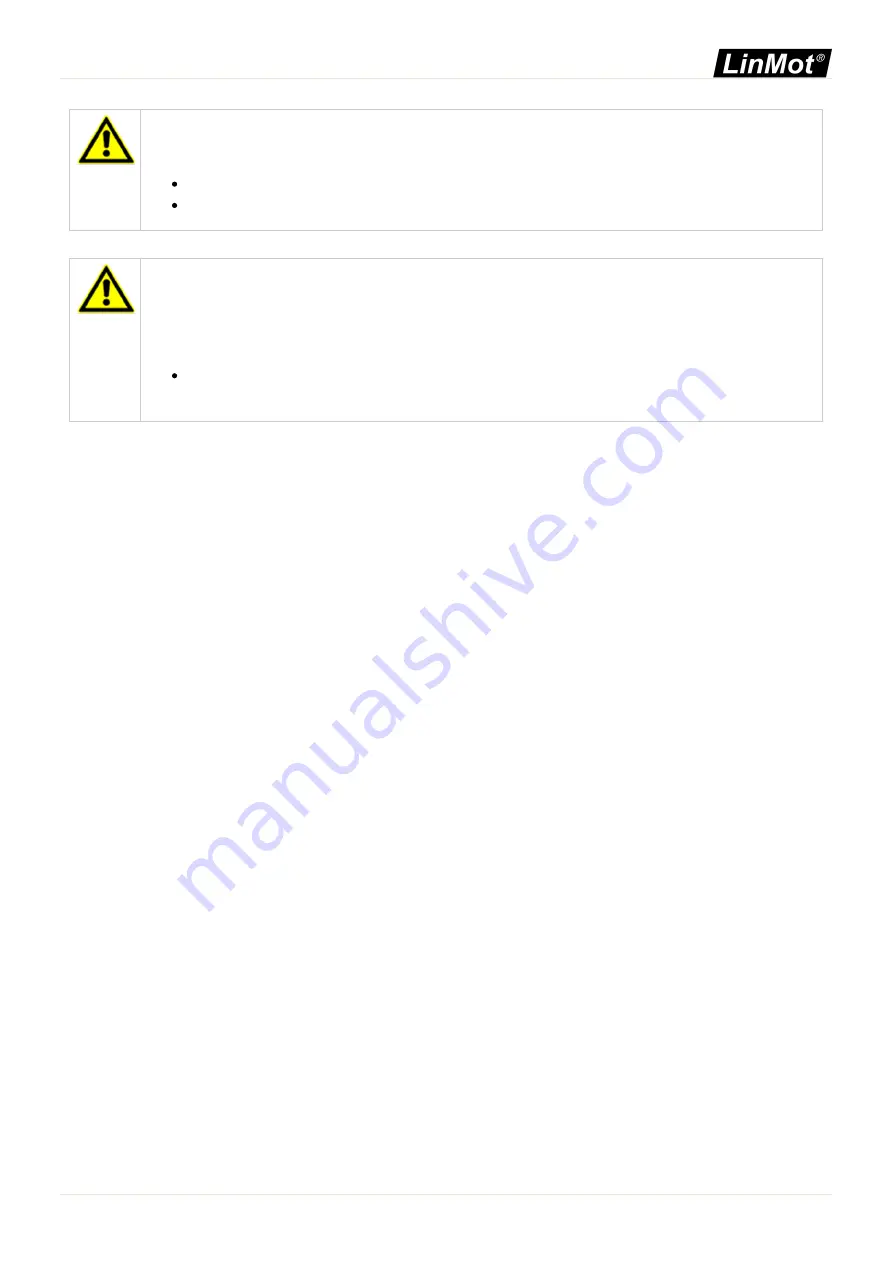
WARNING
Parameterization of the encoder system
Encoder faults are detected using different hardware and software monitoring functions.
It is not permissible to disable these monitoring functions.
Set the encoder configuration correctly.
WARNING
Converter operation despite active messages
With activated safety functions, there are a number of system messages that still permit the drive to be
traversed. In these cases, you must ensure that the causes of the messages are corrected immediately.
These messages include, among others, the following:
Brake Test Time Ov: The brake test time interval has been elapsed. A brake test must be performed
as soon as possible.
2S Drive Systems / 0185-1174_E_1V1_SM_C1251-2S / NTI AG
0185-1174_E_1V1_SM_C1251-2S / 2021-11-26 16:43 (Rev. 12500)
Page 30 of 150