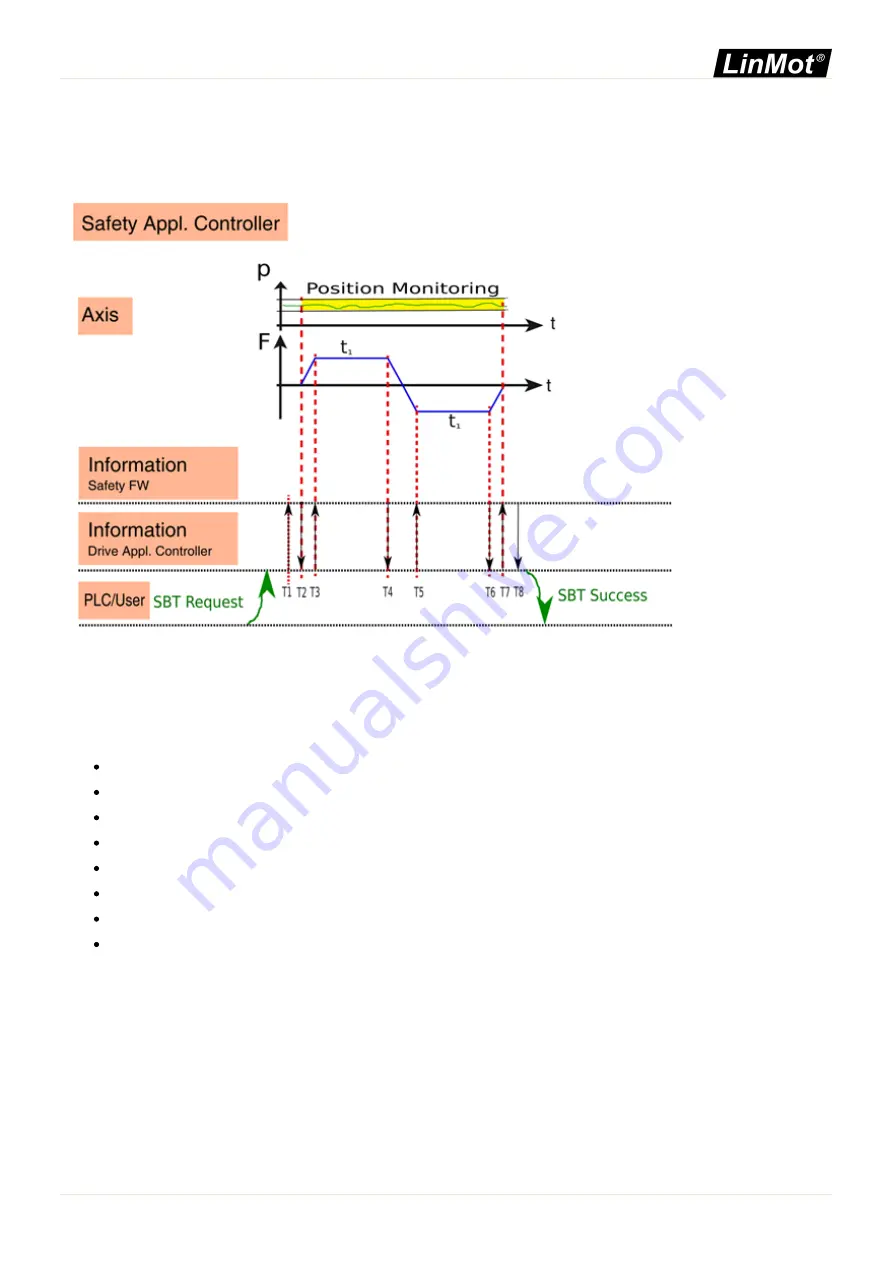
7.17 Safe Brake Test (SBT)
With the SBT test, a sequence is started, where the brake efficiency is tested. Therefore the motor will produce a force
or torque and the brake must hold the motor in position. The following figure shows the sequence:
Figure 25: SBT
The SBT sequence is processed in the drive automatically when it is requested. Therefore the motor has to be disabled
and the motor is braked. The Safety FW controls and monitors the complete SBT sequence. The following steps are
performed (the states can be monitored with the variable SBT State (UPID 1A42h)):
T1: the external SBT request is sent to the safety FW.
T2: the safety FW commands the drive appl. controller to ramp up the positive force/torque.
T3: the drive appl. controller informs the safety FW that the positive force/torque is reached.
T4: after the configurable SBT apply time the safety FW commands to ramp to the negative force/torque.
T5: the drive appl. controller informs the safety FW that the negative force/torque is reached.
T6: after the configurable SBT apply time the safety FW commands to ramp the force/torque to zero.
T7: the drive appl. controller informs the safety FW that the force/torque is turned off.
T8: the safety FW finishes the test sequence and sets all feedback signals. The feedback signals are updated and
the test is finished.
2S Drive Systems / 0185-1174_E_1V1_SM_C1251-2S / NTI AG
0185-1174_E_1V1_SM_C1251-2S / 2021-11-26 16:43 (Rev. 12500)
Page 104 of 150