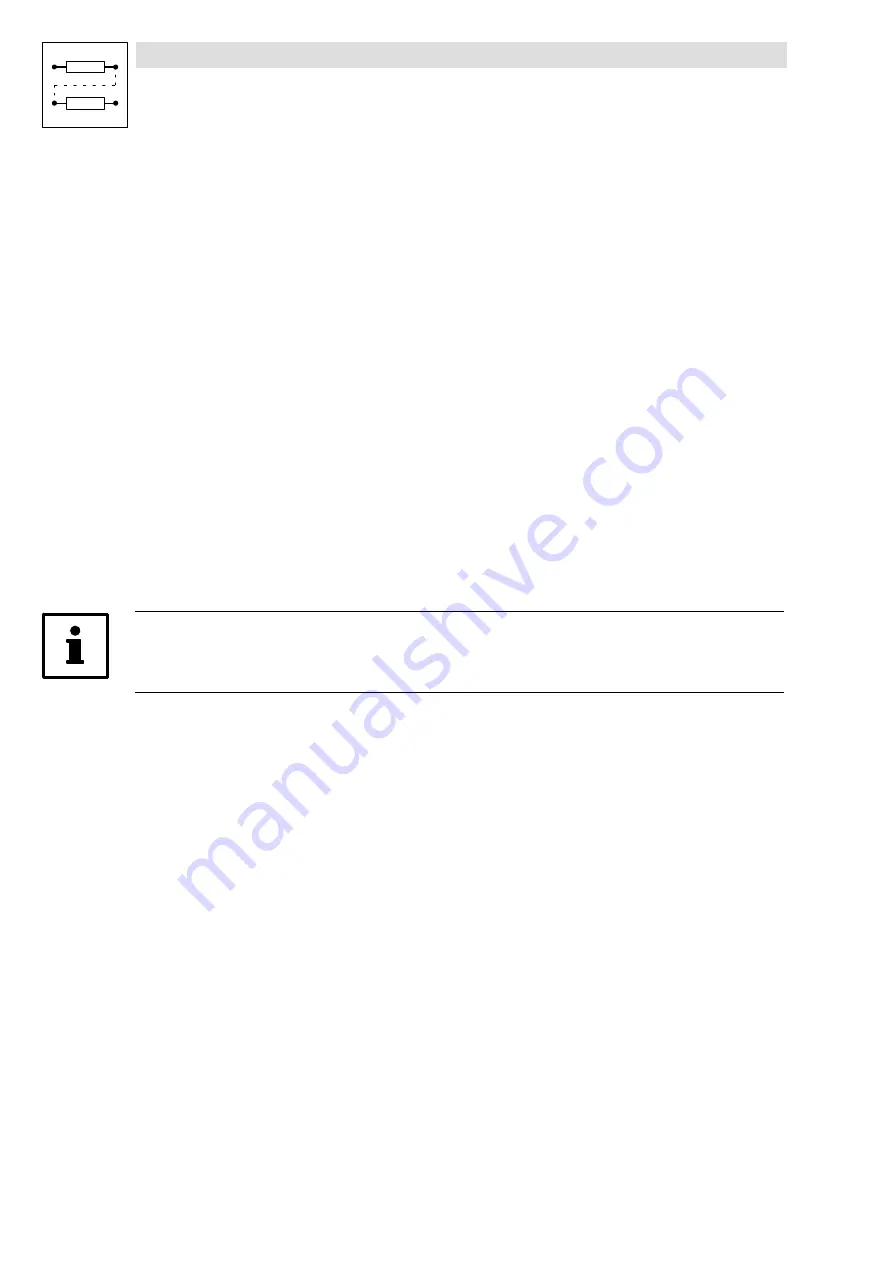
Configuration
2−124
l
EDSVF9383V−EXT EN 2.0
Fine setting
For the fine setting, repeat the following points several times.
1. Try to obtain a very low final speed without the controller reaching the undervoltage threshold
LU:
– Increase the proportional gain V
p
(C0980).
– Reduce the integral−action time T
n
(C0981).
2. Try to avoid activation of the brake unit or the undervoltage threshold OU:
– Increase the integral−action time T
n
(C0981) until the characteristic in Fig. 2−97 is almost
reached.
– If necessary, also reduce the setpoint of the DC−bus voltage at the input MFAIL−DC−SET (in
the example C0472/19).
3. An increase of the deceleration time or reduction of the brake torque (see Fig. 2−98) is only
possible with restrictions:
– Increasing the acceleration time T
ir
(C0982) reduces the initial brake torque and
simultaneously increases the deceleration time.
– Increasing the integral−action time T
n
(C0981) reduces the initial brake torque and
simultaneously increases the deceleration time. If the integral−action times under C0981 are
too long, the controller reaches the LU threshold before zero speed is reached. The drive is
thus no longer under control.
4. Re−establish any signal connections which may be required to the outputs of the drive
controller (terminals X6).
Tip!
Use C0003 to save all settings in a parameter set , if they are to be retained on power−off.
Содержание 9300 vector Series
Страница 8: ...Preface Definition of notes used 1 6 l EDSVF9383V EXT EN 2 0...
Страница 188: ...Application examples Centre winder with internal diameter calculation 3 18 l EDSVF9383V EXT EN 2 0...
Страница 192: ...Signal flow charts Speed control 4 4 l EDSVF9383V EXT EN 2 0 Fig 4 1 Basic configuration 1000 speed control sheet 1...
Страница 205: ...Signal flow charts Step control 4 17 l EDSVF9383V EXT EN 2 0 Fig 4 13 Basic configuration 2000 step control sheet 1...
Страница 211: ...Signal flow charts Torque control 4 23 l EDSVF9383V EXT EN 2 0 Fig 4 17 Basic configuration 4000 torque control sheet 1...