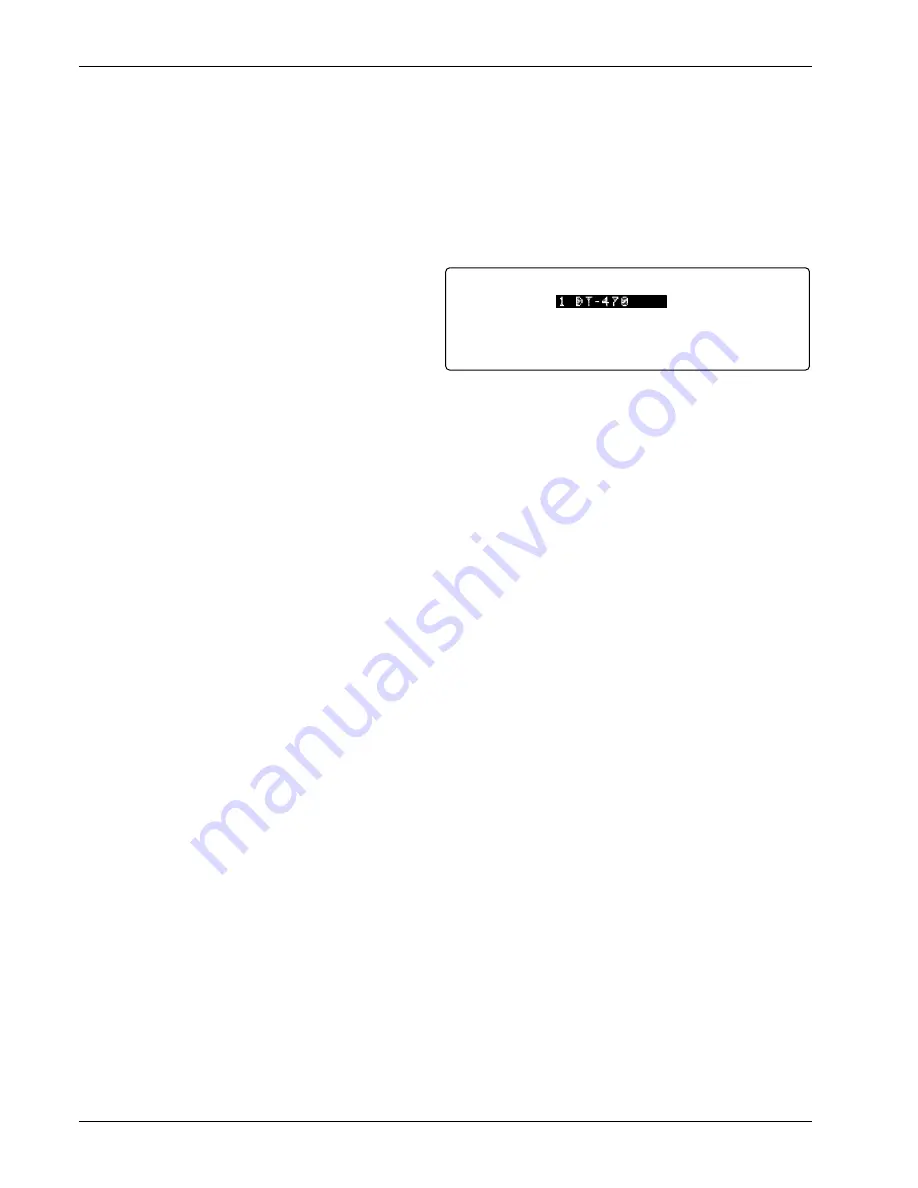
Lake Shore Model 340 Temperature Controller User’s Manual
8-6
Instrument Programming
Perform two-point SoftCal calibrations for applications above 70 K at liquid nitrogen (77.35 K) and room
temperature (305 K). Accuracy for the PT-102, PT-103, or PT-111 platinum sensor is as follows:
±250 mK from 70 K to 325 K
≈
±500 mK from 325 K to
≈
±1400 mK at 480 K
(DIN
Class
A
or
Class
B
tolerance)
Perform three-point SoftCal calibrations at liquid nitrogen (77.35 K), room temperature (305 K), and high
temperature (480 K). Accuracy for the PT-102, PT-103, or PT-111 platinum sensor is
±250 mK from 70 K to
325 K, and ±250 mK from 325 K to 480 K.
8.2.5 Creating a SoftCal Calibration Curve
Once the calibration data points have been
obtained, you may create a SoftCal calibration.
Press
SoftCal
.
Use the
s
or
t
key to select the Standard curve
that the SoftCal will be based on. Press the
Enter
key. Use the numerical keypad to enter the location
where the new user curve will be stored. Press the
Enter
key. Use the numerical keypad to enter from 1 to 10
digits for a sensor serial number. Press the
Enter
key. Enter the first temperature and corresponding sensor
reading. Press the
Enter
key. Repeat the process for the next two temperature points. When complete, press
the
Save Screen
key. You see a brief
Generating Curve
message, followed by a longer
Saving user
curves...
message. The SoftCal curve has now been generated. The new curve has the name
SCAL XXY
where
XX
is DT for diodes and PT for platinum, and
Y
specifies how many points were used to generate the
curve. Once the curve is generated, you must remember to select the curve for the desired input. Refer to
Paragraph 5.2.
8.3 INTERNAL
PROGRAMMING
Internal programming allows the user to enter a set of simple instructions, called a program, into the
instrument. Some instructions mimic front panel operations; like setpoint ramps and control parameter
changes. Other instructions are for timing and decision making. The instrument can run the instructions in an
internal program without operator interaction. Since program status can be monitored with a computer
interface, internal programs can be used during computer controlled experiments.
The internal program feature works with control Loop 1. There is enough memory in the Model 340 to hold
100 programming instructions. The instructions can be put in up to 10 different program locations. The
program locations are provided to help organize internal programming operations. As many as 100 and as
few as 2 or 3 instructions can be placed in a single program location. The total number of instructions in all
ten program locations must not exceed 100. An End instruction, described in the next paragraph, is included
in each program location but does not take one of the 100 memory locations.
The following paragraphs provide details about the programming instructions offered in the Model 340, then
gives an example of how to put the instructions together into a program. A second example illustrates how
programs in two or more program locations can be used together.
8.3.1 Program
Instructions
The Model 340 has 13 programming instructions divided into three categories: output ramping, direct setting
operations, and flow control. The instructions are listed below with paragraph references.
Command Display
Paragraph
Command
Display
Paragraph
Output
Ramping
Flow
Control
Ramp Setpoint Absolute
Ramp SP Abs. 8.3.1.1
Wait Wait
8.3.1.8
Ramp Setpoint Relative
Ramp SP Rel. 8.3.1.2
Settle
Settle 8.3.1.9
Ramp Manual Output Absolute Ramp MOut Abs.
8.3.1.3
Repeat Repeat
8.3.1.10
Ramp Manual Output Relative
Ramp MOut Rel. 8.3.1.4
End
Repeat End
Repeat
8.3.1.10
Direct Settings
Call Call
8.3.1.11
Control Parameters
Parameters 8.3.1.5
End
End 8.3.1.12
Digital Output
Digital Output
8.3.1.6 No
Operation NOP
8.3.1.13
Relays Relays
8.3.1.7
S t d . C u r v e :
U s e r C u r v e :
1 D T -4 7 0
2 1 S N :
P o in t 1:
P o in t 2 :
P o in t 3 :
T e m p .
4 .2 0 0 0
7 7 .3 5 0 0
3 0 5 .0 0 0
R e a d in g
1.6 2 6 2 2
1.0 2 0 3 2
0 .5 0 6 9 1
S O F T C A L