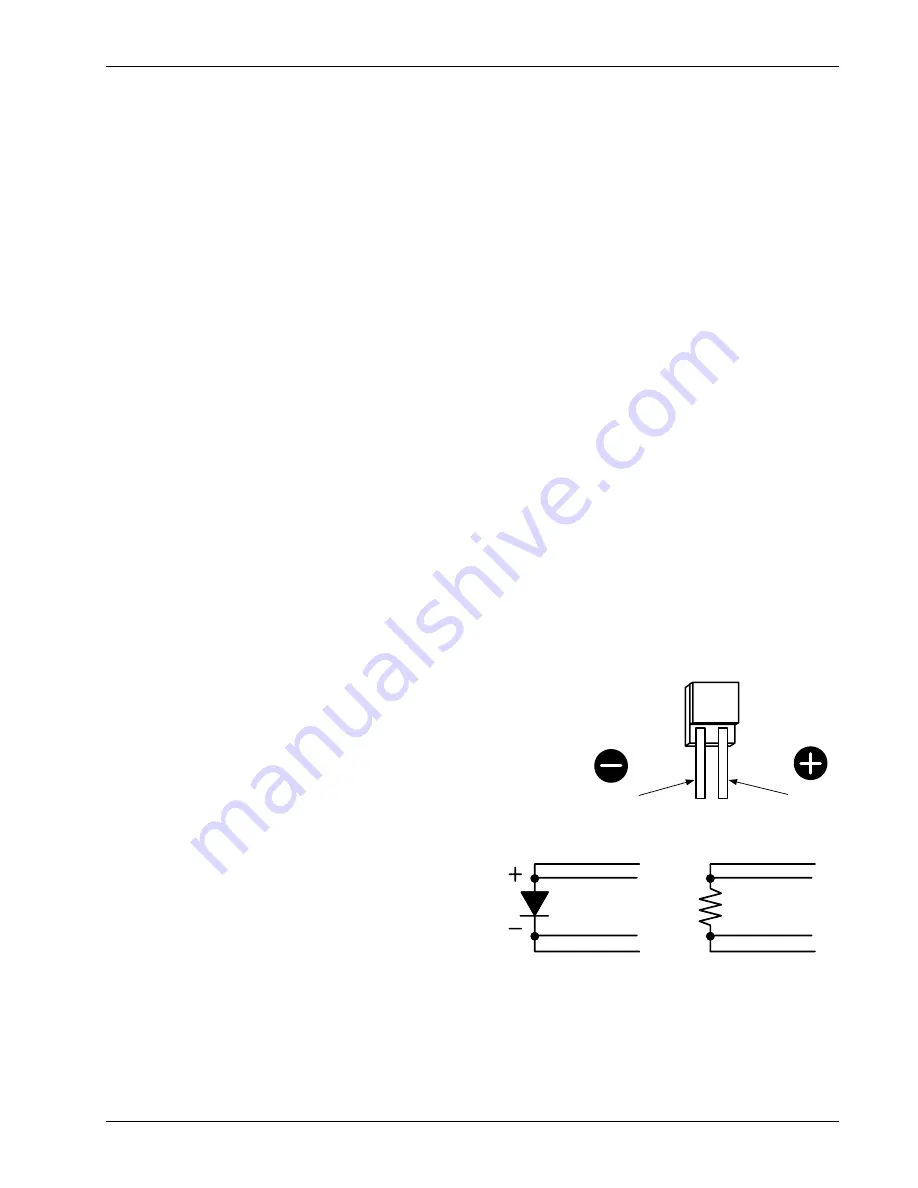
Lake Shore Model 340 Temperature Controller User’s Manual
Installation
3-7
3.4.2 Sensor Lead Cable
The sensor lead cable used outside the cooling system can be much different form what is used inside.
Between the instrument and vacuum shroud, error and noise pick up need to be minimized, not heat leak.
Larger conductor, 22 to 28 AWG stranded copper wire is recommended because it has low resistance yet
remains flexible when several wires are bundled in a cable. The arrangement of wires in a cable is also
important. For best results, voltage leads, V+ and V– should be twisted together and current leads I+ and I–
should be twisted together. The twisted pairs of voltage and current leads should then be covered with a
braided or foil shield which is connected to the driven shield pin of the instrument. This type of cable is
available through local electronics suppliers. Instrument specifications are given assuming 10 feet of sensor
cable. Longer cables, 100 feet or more, can be used but environmental conditions may degrade accuracy and
noise specifications.
3.4.3 Grounding and Shielding Sensor Leads
The sensor input measurements are isolated from earth ground to reduce the amount of earth ground
referenced noise that is present on the measurement leads. This isolation can be defeated by connecting
sensor leads to earth ground on the chassis of the instrument or in the cooling system. If one sensor lead
must be grounded, ground only one lead and ground it in only one place. Grounding leads on more than one
sensor prevents the sensor excitation current sources from operating.
Shielding the sensor lead cable is important to keep external noise from entering the measurement. A shield
is most effective when it is near the measurement potential so the Model 340 offers a driven shield that stays
close to the measurement. The shield of the sensor cable should be connected to the shield pin of the input
connector. It should not be terminated at the opposite end of the cable. The shield should not be connected to
earth ground on the instrument chassis or in the cooling system.
NOTE:
The shell of the connector is in contact with the chassis so the cable shield should never
touch the outer shell of the connector.
The shield pin of the Model 340 input connector can be connected to the shield drive or the measurement
ground. The shield drive is recommended for cables over 20 feet in length. To change the shield pin contact,
use JMP6 for Input B and JMP5 for Input A. See Figure 11-11.
3.4.4 Sensor
Polarity
Lake Shore sensors are shipped with instructions that indicate which
sensor leads are which. It is important to follow these instructions for
plus and minus leads (polarity) as well as voltage and current when
applicable. Diode sensors do not operate in the wrong polarity. They
look like an open circuit to the instrument. Two lead resistors can
operate with any lead arrangement and the sensor instructions may
not specify. Four-lead resistors can be more dependent on lead
arrangement. Follow any specified lead assignment for four lead
resistors. Mixing leads could give a reading that appears correct but
is not the most accurate.
3.4.5 Four-Lead Sensor Measurement
All sensors, including both two lead and four lead can be
measured with a four lead technique. The purpose of a
four lead measurement is to eliminate the effect of lead
resistance on the measurement. If it is not taken out, lead
resistance is a direct error when measuring a resistive
sensor.
In a four lead measurement, current leads and voltage
leads are run separately up to the sensor. With separate leads there is little current in the voltage leads so
their resistance does not enter into the measurement. Resistance in the current leads will not change the
current as long as the voltage compliance of the current source is not reached. When two lead sensors are
used in four lead measurements, the short leads on the sensor have an insignificant resistance.
Anode
Cathode
DT-470-SD
Diode Sensor Leads
I+
V+
I
V
Four-Lead
Diode
Four-Lead
Platinum
I+
V+
I
V