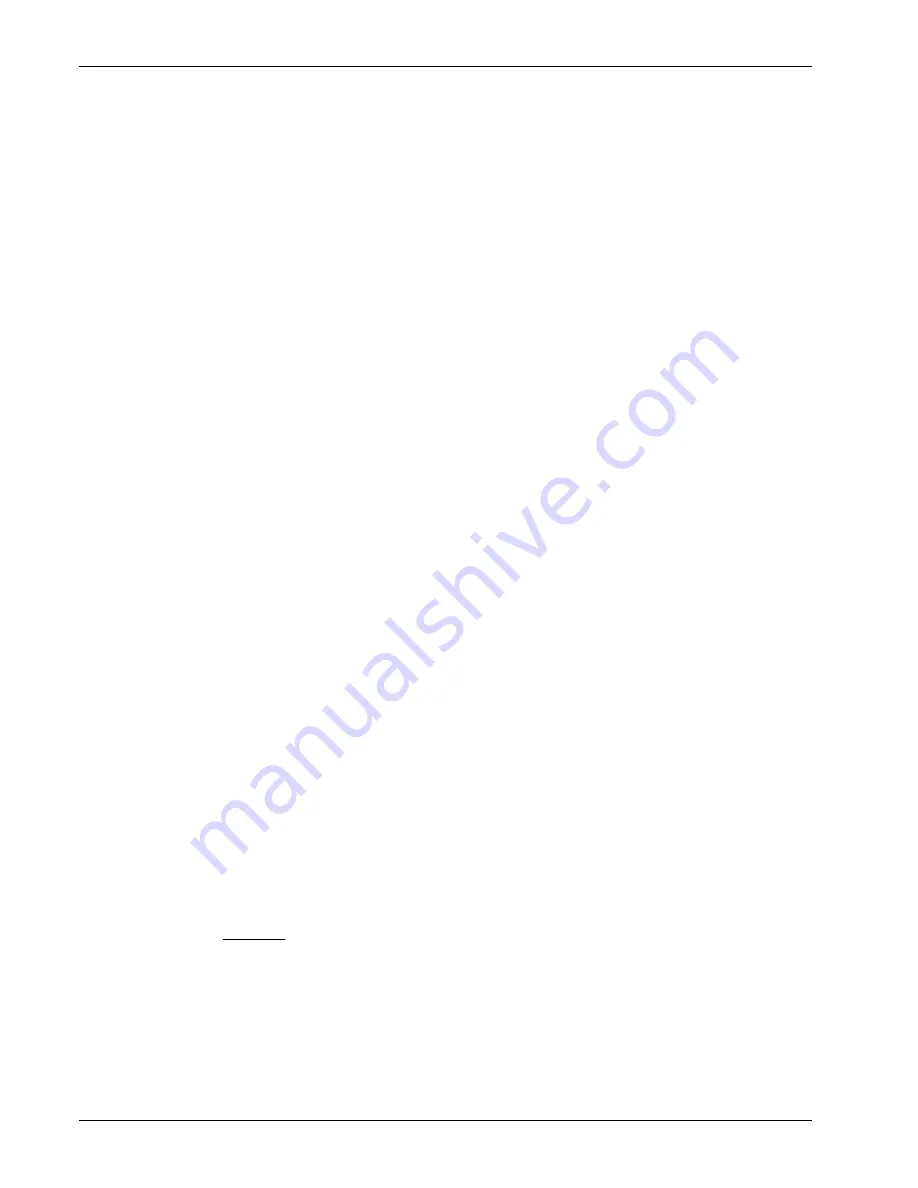
Lake Shore Model 340 Temperature Controller User’s Manual
2-12
Cooling System Design
Tuning Proportional (Continued)
Gradually increase the proportional setting by doubling it each time. At each new setting, allow time for the
temperature of the load to stabilize. As the proportional setting is increased, there should be a setting in which
the load temperature begins a sustained and predictable oscillation rising and falling in a consistent period of
time. See Figure 2-3a. The goal is to find the proportional value in which the oscillation begins, do not turn the
setting so high that temperature and heater output changes become violent.
Record the proportional setting and the amount of time it takes for the load change from one temperature
peak to the next. The time is called the oscillation period of the load and it helps describe the dominant time
constant of the load which is used in setting integral. If all has gone well,
the appropriate proportional setting
is
one half
of the value required for sustained oscillation. See Figure 2-3b.
If the load does not oscillate in a controlled manner, the heater range could be set too low. A constant heater
reading of 100% on the display would be an indication of a low range setting. The heater range could also be
too high, indicated by rapid changes in the load temperature or heater output with a proportional setting of
less than 5. There are a few systems that will stabilize and not oscillate with a very high proportional setting
and a proper heater range setting. For these systems, setting a proportional setting of one half of the highest
setting is the best choice.
2.7.3 Tuning
Integral
When the proportional setting is chosen and the integral is set to zero (off), the Model 340 controls the load
temperature below the setpoint. Setting the integral allows the Model 340 control algorithm to gradually
eliminate the difference in temperature by integrating the error over time. See Figure 2-3d. An integral setting
that is too low causes the load to take too long to reach the setpoint. An integral setting that is too high
creates instability and cause the load temperature to oscillate.
Begin this part of the tuning process with the system controlling in proportional only mode. Use the oscillation
period of the load that was measured above in seconds.
Divide 1000 by the period to get the integral setting.
Enter the integral setting into the Model 340 and watch the load temperature approach the setpoint. If the
temperature does not stabilize and begins to oscillate around the setpoint, the integral setting is too high and
should be reduced by one half. If the temperature is stable but never reaches the setpoint, the integral setting
is too low and should be doubled.
To verify the integral setting make a few small (2 to 5 degree) changes in setpoint and watch the load
temperature react. Trial and error can help improve the integral setting by optimizing for experimental needs.
Faster integrals, for example, get to the setpoint more quickly at the expense of greater overshoot. In most
systems, setpoint changes that raise the temperature act differently than changes that lower the temperature.
If it was not possible to measure the oscillation period of the load during proportional setting, start with an
integral setting of 20. If the load becomes unstable reduce the setting by half. If the load is stable make a
series of small, two to five degree, changes in the setpoint and watch the load react. Continue to increase the
integral setting until the desired response is achieved.
2.7.4 Tuning
Derivative
If an experiment requires frequent changes in setpoint or data taking between changes in the setpoint,
derivative should be considered. See Figure 2-3e. A derivative setting of zero, off, is recommended when the
control system is seldom changed and data is taken when the load is at steady state.
Compute a derivative setting in seconds as one fourth the measured oscillation period of the load in seconds.
If this period is unknown and the integral setting was determined experimentally, the derivative setting in
seconds is calculated as:
D
I
setting
setting
=
×
1000
4
.
Again, do not be afraid to make some small setpoint changes; halving or doubling this setting to watch the
affect.