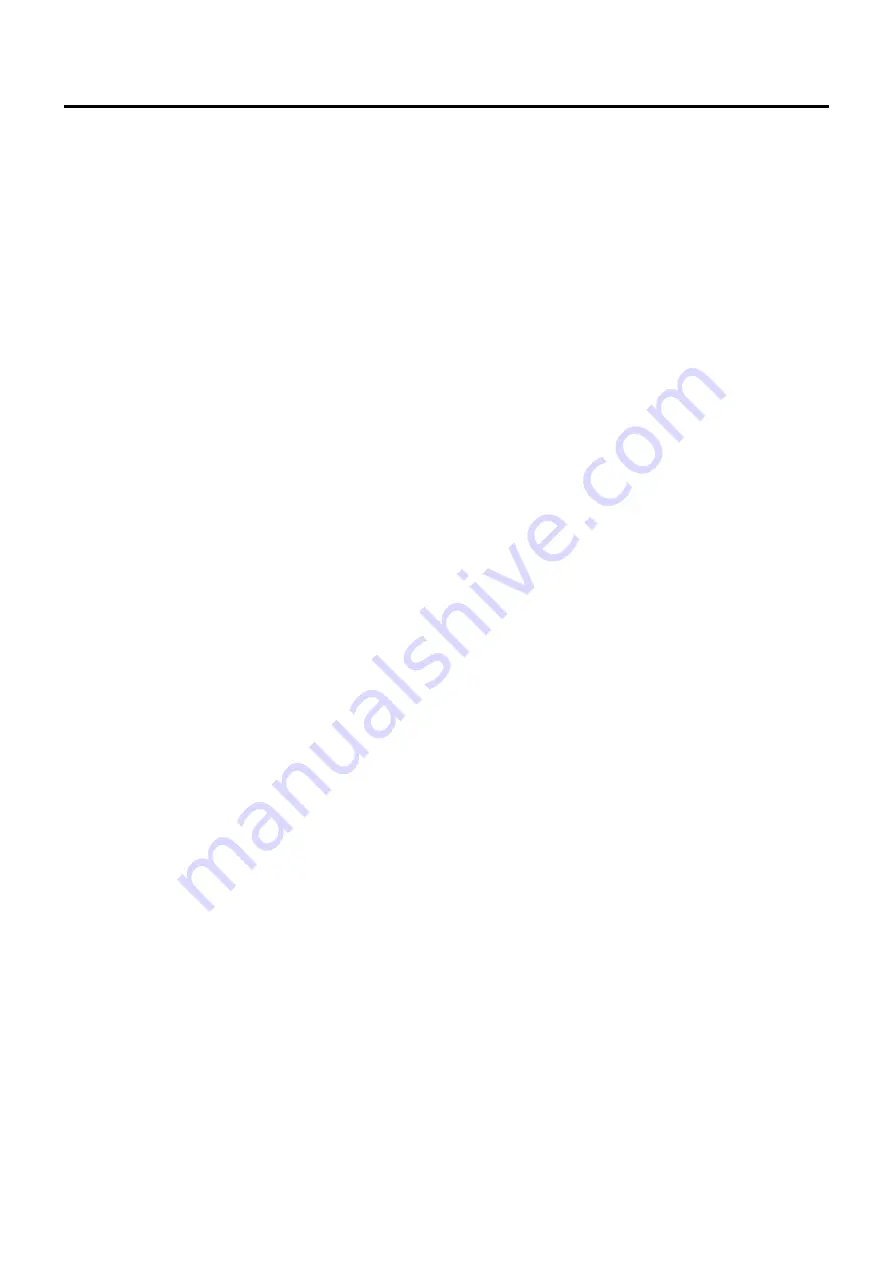
1A-8 Engine Control System
QWS Control
The QWS (quick warm-up system) curtails the engine
warm-up time. The glow control covers the engine
warm-up during the period from pre-startup to
immediate completion of startup. The QWS works
when the vehicle meets the required conditions after
engine startup and the driver turns on the QWS switch,
and lasts until the vehicle deviates from the QWS
working conditions.
QWS working conditions
• The engine coolant is less than 73°C.
• The engine is running at or above 400 rpm for at
least 0.5 second.
• Both EGR and PTO controls are disabled.
• The vehicle is free from AP sensor fault, ECT
sensor fault, A/D conversion fault, idle position
switch fault, clutch switch fault, neutral switch fault,
and vehicle speed sensor fault.
• The difference between actual and desired engine
speeds is less than 50 rpm.
• The desired engine speed is less than 1000 rpm.
• The vehicle is being off.
• The state where the starter switch is turned off and
the idle position switch is turned on lasts for at
least 0.5 seconds.
Exhaust Brake Control
A valve is installed inside the exhaust pipe. Closing this
valve increases the resistance during the exhaust
stroke to enhance the effect of engine brake. The drive
source of the exhaust brake valve is vacuum. A
solenoid valve is installed to control the vacuum. The
exhaust brake is controlled by opening and closing this
solenoid electrically. When the engine is running at or
above 500 rpm, the exhaust cut command is not sent
from the automatic transmission, and exhaust brake or
QWS working conditions are completely met, the VIM
turns on the solenoid valve.
Exhaust Brake Working Conditions
• The vehicle is running at or above 5 km/h or faults
are not detected on the vehicle speed sensor.
• The exhaust brake switch is turned on.
• The engine is running at or above 500 rpm for at
least 1 second.
• The idle position switch is turned on and the gear
is engaged.
• The vehicle is not equipped with ABS/ASR or the
exhaust brake cut command is not sent from the
ASR.
• The vehicle is free from AP sensor fault, exhaust
brake circuit fault, clutch switch fault, neutral
switch fault, idle position switch fault, A/D
conversion fault (VIM), and CAN timeout (VIM).
• For a manual transmission vehicle, the clutch
pedal is not pressed. For an automatic
transmission vehicle, the exhaust brake command
is not sent from the automatic transmission.
• The system voltage stays between 20 V and 30 V.
Idle Stop Control (for Vehicles Equipped with Idle
Stop Control System)
The idle stop control system automatically cuts the
engine to prevent the black smoke emission from the
vehicle that is not running for unloading or other works
(to restart the engine, manual operation is needed).
When all the idle stop conditions are met, the ECM
stops fuel injection and actuates energy-saving relays
to turn off wipers, mirror defoggers, flashers, seat
heaters, and other electrical equipment.
Idle Stop Control Working Conditions
• The driver fails to apply the parking brake and the
signal is input from the alarm unit. (Note 1)
• The vehicle ran at or above 5 km/h.
• The vehicle is idling.
• The vehicle speed is 0 km/h.
• The shift lever is in the neutral position.
• The QWS switch is turned off.
• The engine coolant temperature is at least 10°C.
• The battery voltage is at least 22 V.
• DTC has not been detected.
Note 1: When all the following conditions are met, the
parking brake disengagement alarm unit outputs the
idle stop permit signal to the VIM.
• The idle stop main switch is turned on.
• The shift lever is in the neutral position.
• The parking brake is applied.
• The headlamps are turned off.
• Any of doors is opened.