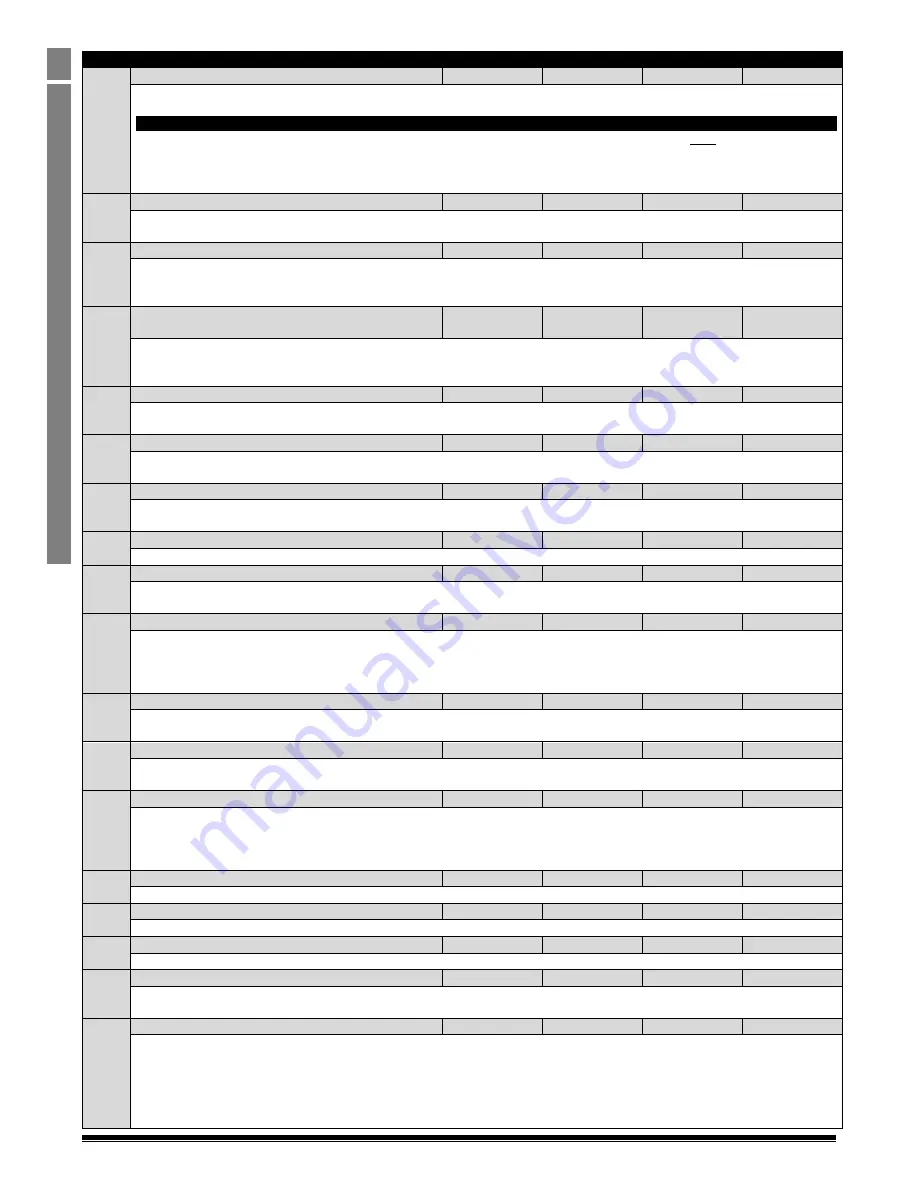
Optidrive P2 Advanced User Guide Rev 2.00
18
www.invertekdrives.com
Opt
idr
ive
P2
Par
ame
ter
Se
t
Ov
er
view
1
Par.
Name
Minimum
Maximum
Default
Units
P6-12
Speed Holding / DC Injection Time on Disable
0
250
0
s
When P6-18 = 0, defines a time period for which the drive will run at Preset Speed 8 (P2-08) following removal of the Enable signal,
before ramping to stop.
Note
Setting this parameter > 0 will result in the drive continuing to operate for the set time at the preset speed
after
the enable signal has
been removed. It is important to ensure this method of operation is safe prior to using this function.
When P6-18 > 0 and Hoist Mode is not enabled (P2-18 ≠ 8), a DC Current, which may be adjusted using P6-18 is injected into the motor
for the time set by this parameter when stopping, which can be useful to ensure the motor has completely stopped.
P6-13
Hoist Mode : Brake Release Time
0.0
5.0
0.2
s
Sets the time for which the drive will hold at the Brake Release Speed (set in P2-07 - Preset Speed 7) to allow the motor brake to
release.
P6-14
Hoist Mode : Brake Apply Time
0.0
5.0
0.3 – 0.5
s
Sets the time for which the drive will hold at the Brake Apply Speed (set in P2-08 - Preset Speed 8) to allow the motor brake to engage.
For vertical hoist applications this value should not be set below the time required for the brake to engage (brake response time, as
specified by the brake manufacturer). The minimum time is 0.1s.
P6-15
Hoist Mode : Brake Release Torque Threshold (Torque
Prove)
0.0
200.0
8.0
%
Sets the torque level, as a % of the nominal motor torque, which must be generated prior to the drive Output Relay 2 closing to signal
the motor holding brake to release. This is used to ensure the motor is connected and that sufficient torque has been generated to
prevent the load dropping on release of the mechanical brake. The torque threshold function is not active in V/f mode.
P6-16
Hoist Mode : Torque Threshold Timeout
0.0
25.0
5.0
s
Sets the time for which, following a start command, the drive will attempt to apply enough torque to the motor to reach the hoist
torque probe level (P6-15). Should the torque probe level not be reached within the set time the drive will trip.
P6-17
Maximum Torque Limit Timeout
0.0
25.0
0.0
Hz/Rpm
Sets the maximum time allowed for the motor to be operating at the motor/generator torque limit (P4-07/P4-09) before tripping. This
parameter is enabled only for vector control operation.
P6-18
DC Injection Braking Current
0.0
100.0
0.0
%
Defines the DC current level as a percentage of motor rated current (P1-08) that is applied to the motor when a stop command is
received and the DC Injection function is activated.
P6-19
Brake Resistor Resistance Value
See Below
200
See Below
Ohms
Sets the brake resistor value in Ohms. This value is used for the brake resistor thermal protection.
P6-20
Brake Resistor Power Rating
0.00
200.00
See Below
kW
Sets the brake resistor power in kW, with a resolution of 0.1kW. This value is used for the brake resistor thermal protection.
The thermal protection allows 10 x P6-20 for 5 seconds within a 50 second period, or 50 x P6-20 for 1 second within 50s.
P6-21
Brake Chopper under Temperature Duty Cycle
0.0
20.0
2.0
%
This parameter defines the duty cycle applied to the brake chopper whilst the drive is in an under temperature trip state. A brake
resistor can be mounted to the drive heat sink, and used to maintain the drive temperature above the minimum operating
temperature. This parameter should be used with extreme care, as incorrect adjustment may result in exceeding the rated power
capacity of the resistor. External thermal protection for the resistor should always be used to avoid this risk.
P6-22
Cooling Fan Runtime Counter Reset
0
1
0
-
0 : No Function
1 : Reset
. Setting to 1 resets the internal Fan run-time counter to zero (as displayed in Index 1 of P0-35).
P6-23
Energy Consumption (kWh) Meter Reset
0
1
0
-
0 : No Function
1 : Reset
. Setting to 1 resets internal kWh meter to zero (as displayed in Index 1 of P0-26 and Index 1 of P0-27).
P6-24
Maintenance Time Interval
0
60000
0
Hours
Allows the user to define a maintenance interval period for the application. This defines the total number of run time hours which
must elapse before the service indicator is displayed. This may be viewed on the drive OLED display, may be programmed to a relay
output, and also sets a bit in the drive status word.
When P6-25 is set to 1, the internal service interval counter is set to this value
P6-25
Maintenance Time Reset
0
1
0
-
When this parameter is set to 1, the internal service interval counter is set to the value defined in P6-24
P6-26
Analog Output 1 Scaling
0.0
500.0
100.0
%
Defines the scaling factor as a % used for Analog Output 1
P6-27
Analog Output 1 Offset
-500.0
500.0
0.0
%
Defines the offset as a % used for Analog Output 1
P6-28
P0-80 Display Value Index
0
200
0
-
This parameter defines the index of the internal variable, the value of which will be displayed in P0-80.
This is usually used in conjunction with the Function Block Program. Refer to section 1.6 for further information.
P6-29
Save User Parameters as Default
0
2
0
-
0 : No Function
1 : Save Parameters.
Setting this parameter to 1 saves the present drive parameter settings to the User Default Parameters Memory.
Following this, if the User carries out a 3-button default parameter command (UP, DOWN and STOP), the parameter saved at this time
will be restored.
2 : Erase Parameters
. Setting 2 clears the User Default Parameters Memory.