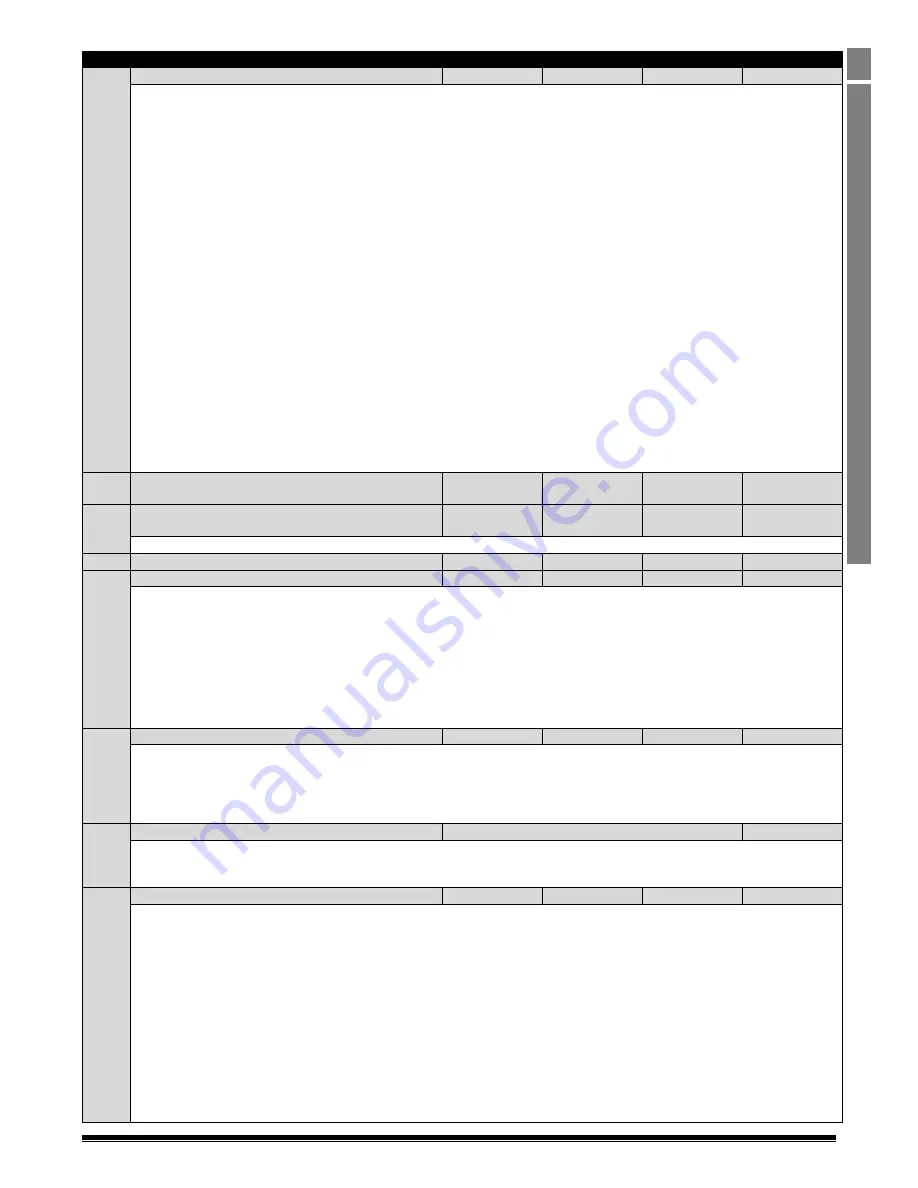
Optidrive P2 Advanced User Guide Rev 2.00
www.invertekdrives.com
9
Opt
idr
ive
P2
Par
ame
ter
Se
t Ov
er
view
1
Par.
Name
Minimum
Maximum
Default
Units
P2-18
User Relay 2 Output (Terminals 17 & 18) Function select
0
14
0
-
Selects the function assigned to Relay Output 2. The relay has two output terminals, Logic 1 indicates the relay is active, and therefore
terminals 17 and 18 will be linked together.
0
: Drive Enabled (Running)
. Logic 1 when the motor is enabled
1 : Drive Healthy
. Logic 1 when power is applied to the drive and no fault exists
2
: At Target Frequency (Speed)
. Logic 1 when the output frequency matches the setpoint frequency. Hysterisis is applied, defined by
P6-04.
3 : Output Frequency > 0.0 Hz
. Logic 1 when the drive output frequency to the motor is exceeds 0.0Hz. Hysterisis is applied, defined by
P6-04.
4
: Output Frequency >= Limit
. Logic 1 when the motor speed exceeds the adjustable limit
5
: Output Current >= Limit
. Logic 1 when the motor current exceeds the adjustable limit
6
: Output Torque >= Limit
. Logic 1 when the motor torque exceeds the adjustable limit
7
: Analog Input 2 Signal Level >= Limit
. 1 Logic when the signal applied to the Analog Input 2 exceeds the adjustable limit
8 : Hoist Brake Control
. When P2-18 = 8, the Optidrive is set to ‘Hoist Mode Operation’, and output relay 2 must be used to control the
motor holding brake.
9 : No Function
10 : Service Due
. Logic 1 when the user settable maintenance time (P6-24) has expired. This allows the user to set a service interval
time, for example in the even where a machine requires a defiend service time interval for maintenance, the drive can provide visual
indication of the maintenance interval.
11 : Drive Ready to Run
. Defined as not in inhibit mode, hardware enable present, not in mains loss condition and no trip.
12 : Drive Tripped.
Logic 1 when the drive has
tripped and the display shows a fault.
13 : STO Status.
Logic 1 when the STO inputs are present, and the drive is not in inhibit state
Note
: When using settings 4 – 7, parameters P2-19 and P2-20 must be used together to control the behaviour. The output will switch
to Logic 1 when the selected signal exceeds the value programmed in P2-19, and return to Logic 0 when the signal falls below the value
programmed in P2-20.
14 : PID Error >= Limit.
Logic 1 when the PID Error exceeds the adjustable threshold
P2-19
Adjustable Threshold 1 Upper Limit (Analog Output 2 /
Relay Output 2)
P2-20
200.0
100.0
%
P2-20
Adjustable Threshold 1 Lower Limit (Analog Output 2 /
Relay Output 2)
0.0
P2-19
0.0
%
Used in conjunction with some settings of Parameters P2-13 & P2-18.
P2-21
Display Scaling Factor
-30.000
30.000
0.000
-
P2-22
Display Scaling Source
0
3
0
-
P2-21 & P2-22 allow the user to program the Optidrive to display an alternative output unit scaled from an existing parameter, e.g. to
display conveyer speed in metres per second based on the output frequency. This function is disabled if P2-21 is set to 0.
If P2-21 is set >0, the variable selected in P2-22 is multiplied by the factor entered in P2-21, and can be displayed whilst the drive is
running. The display will show a ‘
’ on the left hand side to indicate the customer scaled units.
P2-22 Setting Options :-
0 : Motor Speed
1 : Motor Current
2 : Analog Input 2
3 : P0-80 Value
P2-23
Zero Speed Holding Time
0.0
60.0
0.2
Seconds
Determines the time for which the drive output frequency is held at zero when stopping, before the drive output is disabled. This can
be utilised to ensure the motor has come to a complete standstill before the drive switches off, or to allow time for a holding brake to
engage. It is not intended to provide a continuous output holding torque for prolonged periods.
When operating in V/F mode, the output voltage and hence current will be dependent on the setting of P1-11.
When operating in Vector Mode, the output voltage and current are automatically controlled by the vector algorithm.
P2-24
Effective Switching Frequency
See Below
kHz
Effective power stage switching frequency. The range of settings available and factory default parameter setting depend on the drive
power and voltage rating, refer to section 2.1. Higher frequencies reduce the audible ‘ringing’ noise from the motor, and improve the
output current waveform, at the expense of increased drive heat losses.
P2-25
Fast Deceleration Ramp Time (Fast Stop)
0.00
240.0
0.00
Seconds
This parameter allows an alternative deceleration ramp down time to be programmed into the Optidrive, which can be selected by
digital inputs (dependent on the setting of P1-13) or selected automatically in the case of a mains power loss if P2-38 = 2.
When set to 0.00, the drive output will be immediately disabled, and the load will coast to stop.