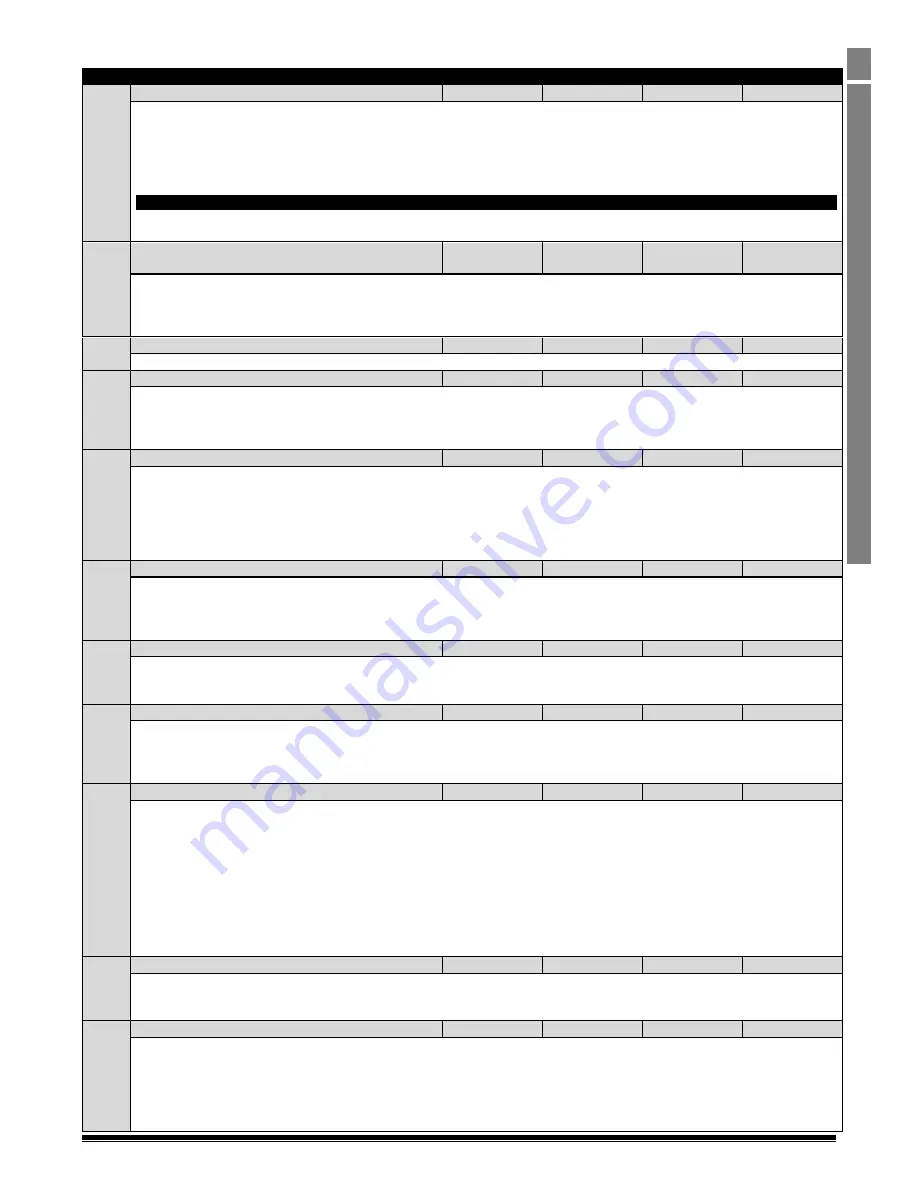
Optidrive P2 Advanced User Guide Rev 2.00
www.invertekdrives.com
17
Opt
idr
ive
P2
Par
ame
ter
Se
t Ov
er
view
1
1.3.6.
Parameter Group 6 – Advanced Functions
Par.
Name
Minimum
Maximum
Default
Units
P6-01
Enable Firmware Upgrade
0
3
0
-
Enables the firmware upgrade mode, allowing the User Interface firmware and/or the Power Stage Control firmware to be upgraded.
Options are:
0 : Disabled
1 : Upgrade User Interface and Power Stage Control firmware
2 : Upgrade User Interface firmware only
3 : Upgrade Power Stage Control firmware only
NOTE
This parameter should not be adjusted by the User. The firmware upgrade process is carried out fully automatically using Optitools
Studio PC software.
P6-02
Automatic Thermal Management Minimum Switching
Frequency
4
Model
Dependent
4
kHz
This parameter defines the minimum effective switching frequency which the drive will use.
During operation, the drive measures the power module temperature and will switch automatically to a lower switching frequency if
the temperature reaches a pre-defined limit. This parameter determines the lowest frequency that can be used. In the event that the
power module temperature continues to increase, the drive will trip on over temperature.
P6-03
Auto Reset Time Delay
1
60
20
s
Sets the delay time which will elapse between consecutive drive reset attempts when Auto Reset is enabled in P2-36
P6-04
Relay Output Hysteresis Control
0.0
25.0
0.3
-
This parameter works in conjunction with P2-11 and P2-13 = 2 or 3 to set a band around the target speed (P2-11 = 2) or zero speed
(P2-11 = 3). When the speed is within this band, the drive is considered to be at target speed or Zero speed. This function is used to
prevent “chatter” on the relay output if the operating speed coincides with the level at which the digital / relay output changes state.
e.g. if P2-13 = 3, P1-01 = 50Hz and P6-04 = 5%, the relay contacts close above 2.5Hz
P6-05
Encoder Speed Feedback Enable
0
1
0
-
0 : Disabled
1 : Enabled
. Setting to 1 enables encoder control mode of operation, which requires an optional encoder feedback interface. For
correct operation, ensure that the encoder has been properly fitted to the motor and its wiring is connected to the encoder feedback
module in accordance with the Encoder Feedback Interface User Guide. Before enabling this parameter, ensure that the sense of
rotation is correct by using parameter P0-57 (encoder feedback speed) while running in V/f mode. The sign in P0-57 should match that
of the speed reference.
P6-06
Encoder PPR
0
65535
0
-
When using the optional encoder feedback interface (OPT-2-ENCOD), this parameter should be set to the number of Pulses Per
Revolution for the connected encoder. This value has to be set correctly to guarantee proper operation of the drive when Encoder
feedback mode is enabled (P6-05 = 1). Improper setting of this parameter could cause the loss of control of the drive and / or a trip. If
set to zero, encoder feedback will be disabled.
P6-07
Speed Error Trip Level
0.0
100.0
5.0
%
When operating in vector mode, this parameter defines the maximum permissible error between the commanded motor speed and
the esitamed or measured motor speed. This provides protection against overspeeding or loss of motor control. If the speed error
exceeds this limit, the drive will trip. When set to zero, this protection is disabled.
P6-08
Maximum Speed Reference Frequency
0
20
0
kHz
When the motor speed reference is to be controlled by a frequency input signal (connected to Digital input 3), this parameter is used
to define the input frequency which corresponds to the maximum motor speed (set in P1-01). This maximum frequency that can be
set in this parameter must be in the range 5kHz to 20kHz.
When set to 0, this function is disabled.
P6-09
Speed Droop Control
0.0
25.0
0.0
%
This parameter only applies when the drive is in vector speed control mode. (P4-01=0, 3, 4,5, 6) When set to zero, the speed droop
control function is disabled. If P6-09 > 0, this parameter effectively defines a slip speed at motor rated output torque.
The droop speed is the percentage value of P1-09. Depending on the motor load condition, the reference speed will be reduced by a
certain droop value before goes into speed controller, calculated as shown below:
Droop speed = P6-09 * P1-09
Droop value = Droop speed * ( Motor real torque / Motor rated torque)
Speed controller input = Speed reference – Droop value
Droop control can be used to provide a small reduction in motor speed in proportion to the applied load. This can be especially useful
where multiple motors drive a common load, and the load should be shared evenly between the motors.
The real time droop value may be viewed in P0-62.
P6-10
Enable Function Block Program Operation
0
1
0
-
0 : Function Block Program Disabled.
1 : Function Block Prgram Enabled
. This parameter must be set to 1 to enable any Function Block Program loaded into the drive to
operate. When set to 0, the Function Block Program will be disabled.
P6-11
Speed Holding Time on Enable
0
250
0
s
Defines a time period for which the drive will run at Preset Speed 7 (P2-07) when the Enable signal is applied to the drive. The preset
speed can be any value from minimum to maximum frequency and in either direction. This function can be useful in applications
requiring controlled start-up behaviour regardless of the normal system operation, and allows the user to program the drive to always
start at the same frequency, with the same direction of rotation for a specified time period before returning to normal operation.