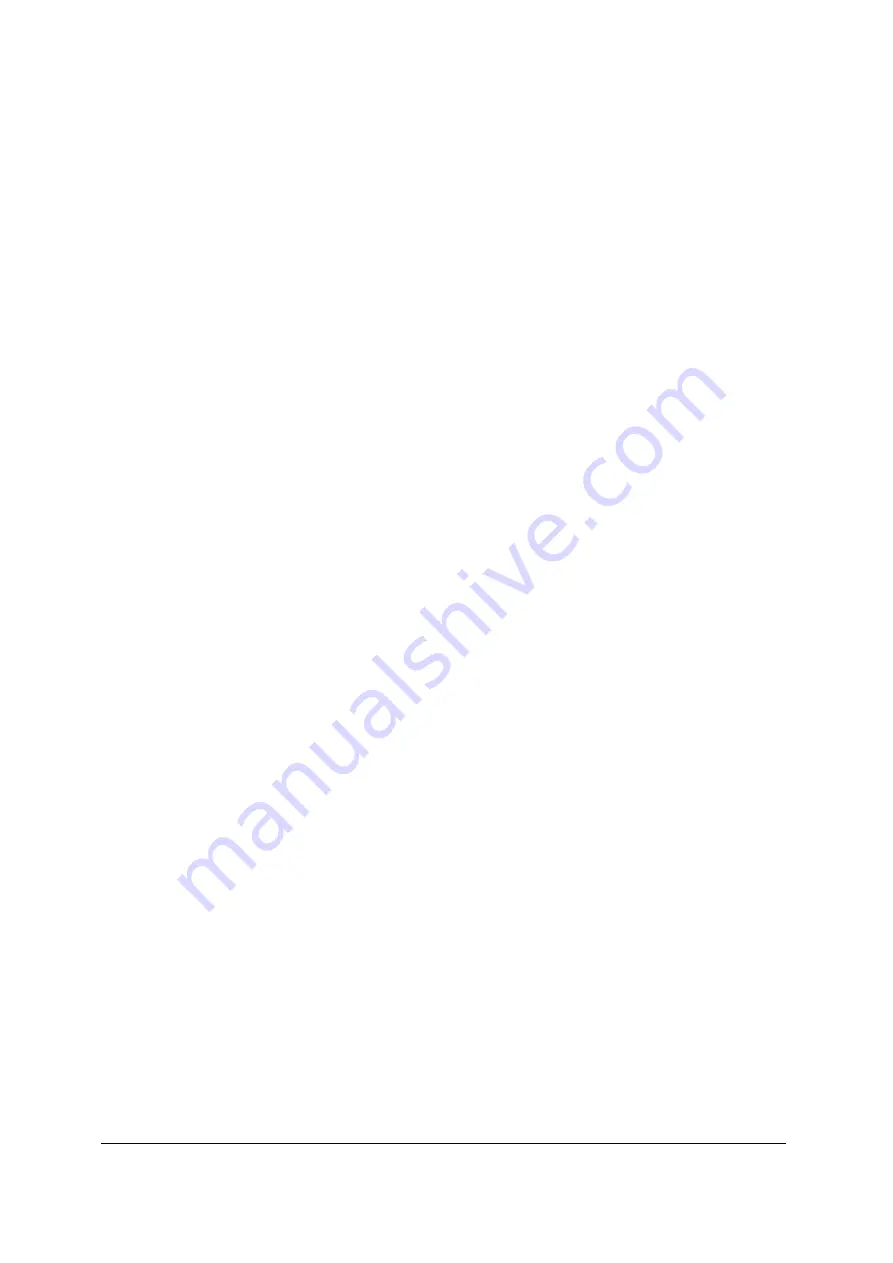
TransformerCare Unit
Status monitoring
HYDAC FILTER SYSTEMS GMBH
en
Page 40 / 64
BeWa TCU 3472805b en 2011-07-05.doc
2011-07-05
Continuous water content monitoring (optional)
If the TCU is equipped with an AquaSensor AS1000, you can measure the degree
of saturation (relative moisture) of the oil. This degree of saturation is output by the
AquaSensor in the range of 0 … 100% as 4 … 20mA signal.
For this, 0% would mean water-free oil and 100% would mean oil that is completely
saturated with water.
The AquaSensor absorbs water molecules from the fluid, which leads to a change in
the capacity of the sensor element. The measured value received presents the
saturation of the fluid as a percentage.
A thermocouple integrated on the AquaSensor measures the temperature in the
range from -25 … 100°C. This is output like the saturation as a 4 … 20mA signal.
The 4 … 20mA signals are fitted in the switch box (see Page 28).
Содержание TCU Series
Страница 63: ...Notes ...