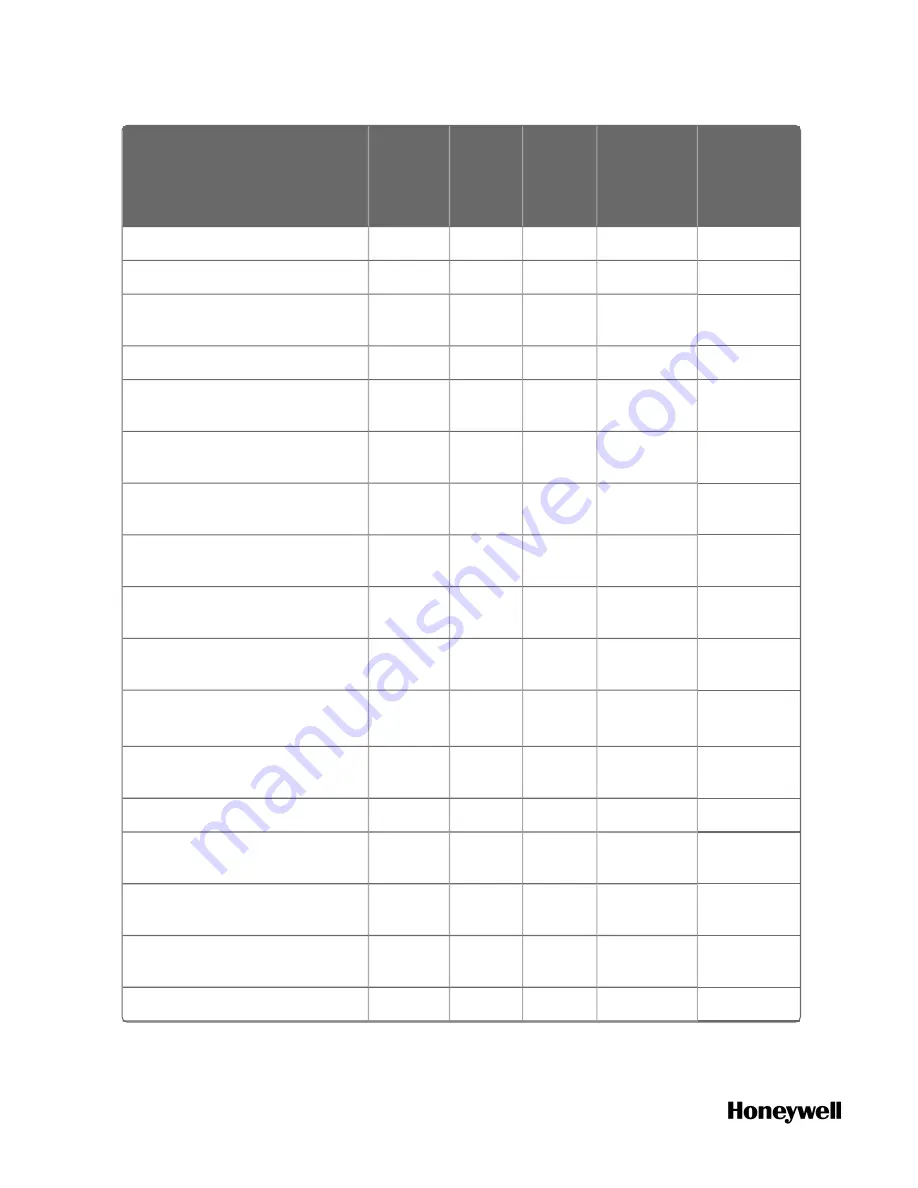
Module
A: Enter
Quantity
B: Max
Current
@ 5V
C: Max
Current
@ 24V
D:
Calculate
5V current
(D = A * B)
E:
Calculate
24V
current (E
= A * C)
EPM
( )
500mA
0mA
( )
( 0 )
PSM
( )
22 mA
0 mA
( )
( 0 )
UIO
( )
380
mA
0 mA*
( )
( 0 )
UAI
( )
40 mA
25 mA
( )
( )
DIM, 120/240 VAC, 16
Channel
( )
130
mA
0 mA
( )
( 0 )
DIM, AC/DC, 16 Channel
( )
130
mA
0 mA
( )
( 0 )
DIM, 24 VDC, 32 Channel
( )
130
mA
0 mA
( )
( 0 )
DOM, 120/240 VAC, 8
Channel
( )
220
mA
0 mA
( )
( 0 )
DOM, 24 VDC, 32 Channel
( )
235
mA
0 mA
( )
( 0 )
Relay Output, 8 Channel
( )
110
mA
100
mA
( )
( )
AOM, 4 Channel
( )
40 mA
200
mA
( )
( )
AOM, 8 Channel
( )
225
mA
350
mA
( )
( )
HLAI, 16 Channel
( )
75 mA
50 mA
( )
( )
DIM, Contact type, 16
Channel
( )
130
mA
40 mA
( )
( )
Pulse/Frequency/Quadrature
( )
110
mA
250
mA
( )
( )
Serial Comm Module
( )
400
mA
0 mA
( )
(0)
Redundancy Module
( )
1 mA
0 mA
( )
(0)
80
Содержание ControlEdge 900 platform
Страница 6: ...6 Contents ...
Страница 12: ...12 Chapter 1 About this guide ...
Страница 52: ...52 ...
Страница 57: ...57 One Slot Rack 1 CPM 1 EPM 1 P S 1 RM ...
Страница 59: ...59 One Slot Rack ...
Страница 62: ...Figure 5 7 Rack dimensions with redundant power supply 62 ...
Страница 75: ...75 c Insert the Ethernet cables and mount the security cover for the EMP ...
Страница 76: ...d Optional mount a wire security seal The user should get a wire security seal themselves 76 ...
Страница 124: ...Figure 5 31 Universal Analog Input Wiring Figure 5 32 Examples of RTD Input Wiring 124 ...
Страница 125: ...125 Figure 5 33 Analog Input Wiring Eight TCs Figure 5 34 Analog Input Wiring Eight Resistance Inputs ...
Страница 136: ...Settings using input 1 as example Single ended factory setting Differential Figure 5 46 Pulse Counting Wiring 136 ...
Страница 137: ...137 Figure 5 47 Pulse Outing Wiring Figure 5 48 Frequency Wiring ...
Страница 138: ...Figure 5 49 Quadrature Differential External Power Wiring Figure 5 50 Quadrature Single Ended External Power Wiring 138 ...
Страница 144: ...Figure 5 57 16 point High Level Analog Input Wiring 144 ...
Страница 147: ...147 Figure 5 60 AC DC Isolated Input Module Wiring ...
Страница 148: ...148 ...
Страница 168: ...168 ...
Страница 178: ...178 Chapter 8 Diagnostics and Troubleshooting ...
Страница 221: ...Appendix A Installing RTP RTP Internal schematic Applies to UAI Figure A 13 Analog Input RTP Internal schematic 221 ...
Страница 222: ...Appendix A Installing RTP 222 ...
Страница 227: ...Appendix A Installing RTP Relay Output RTP Internal schematic 227 ...