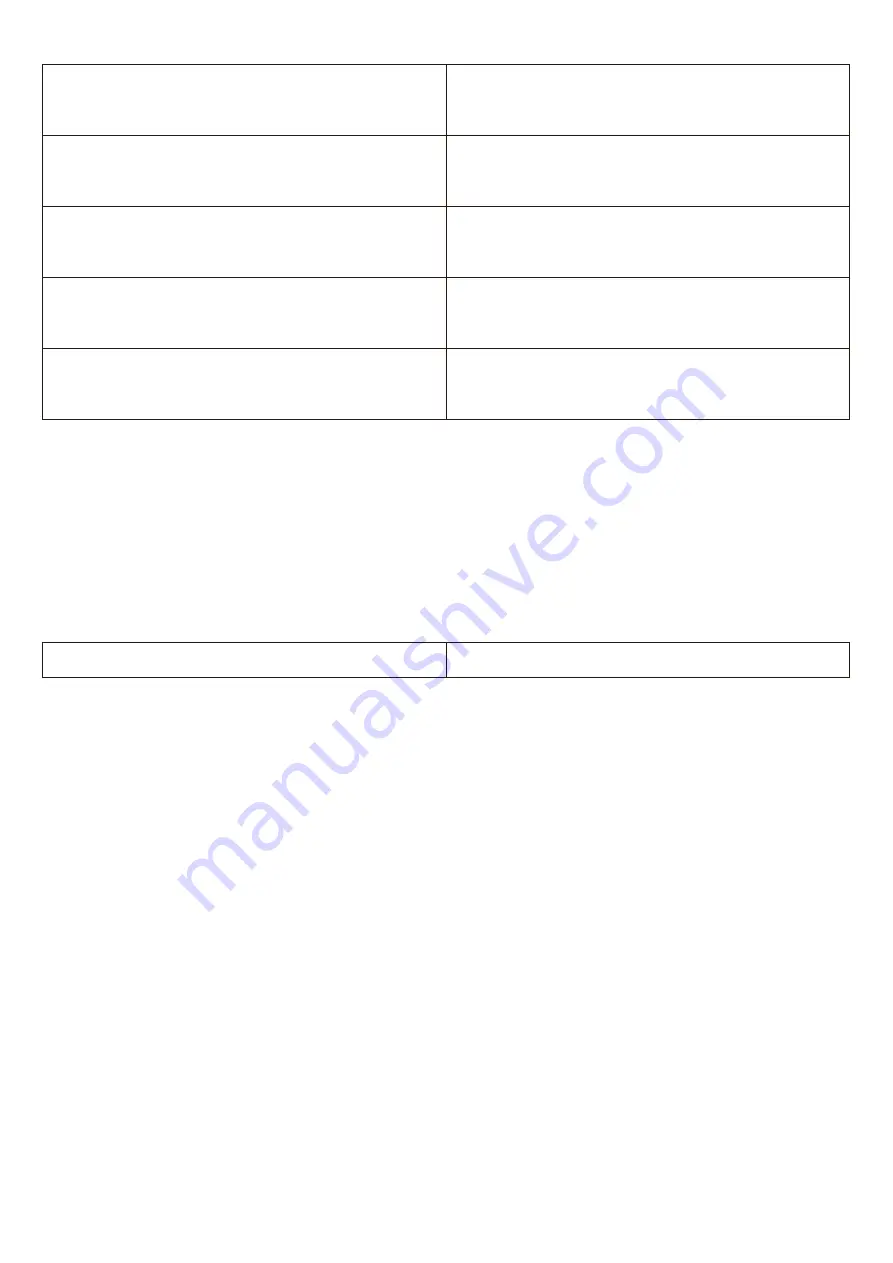
65
F1-06 stator resistance of asynchronous motor
0.001Ω
~
65.535Ω( frequency inverter power ≤55kW )
0.0001 ~ 6.5535 ( frequency inverter power > 55kW )
[ model determination ]
F1-07 rotor resistance of asynchronous motor
0.001Ω
~
65.535Ω( frequency inverter power ≤55kW )
0.0001 ~ 6.5535 ( frequency inverter power > 55kW )
[ model determination ]
F1-08 induction motor leakage reactance
0.01 ~ 655.35 mH ( frequency inverter power ≤ 55 kW )
0.001 ~ 65.535 mH ( frequency inverter power > 55 kW )
[ model determination ]
F1-09 mutual inductance reactance of asynchronous
motor
0.1 ~ 6553.5 mH ( frequency inverter power ≤ 55 kW )
0.01 ~ 655.35 mH ( frequency inverter power > 55 kW )
[ model determination ]
F1-10 asynchronous motor no-load current
0.01A ~ F1 - 03 ( frequency inverter power ≤ 55kW )
0.1A ~ F1 - 03 ( frequency inverter power > 55kW )
[ model determination ]
F1-06
~
F1-10 is parameters of asynchronous motors. These parameters are generally not found on the motor
nameplate and need to be automatically tuned by the frequency inverter. Among them, “asynchronous motor static
tuning" can only obtain F1-06
~
F1-08 three parameters, while " asynchronous motor complete tuning" can obtain not
only all five parameters here, but also encoder phase sequence, current loop PI parameters, etc.
When changing the rated power of the motor (F1 - 01) or the rated voltage of the motor (F1 - 02), the frequency
inverter will automatically modify the F1 - 06 ~ F1 - 10 parameter values to restore these 5 parameters to the
common standard Y series motor parameters. If it is impossible to tune the asynchronous motor on site, you can
enter the above-mentioned corresponding function code according to the parameters provided by the motor
manufacturer.
F0 - 29 motor parameters self - tuning
0
~
3 [0]
0: no operation.
1: simple static self - tuning.
It is suitable for asynchronous motors where large inertia loads are not easy to disengage and cannot be
rotated.
2: rotational self - tuning
During the complete setting process, the frequency inverter will first perform static setting, and then accelerate
to 80 % of the rated frequency of the motor according to the acceleration time F0 - 10. After maintaining for a period
of time, the frequency inverter will slow down and shut down according to the deceleration time F0 - 11 and end the
setting.
3. Advanced static self-tuning
Is applicable to the case where there is no encoder, and the motor parameters are self-learned when the motor
is at rest (at this time, the motor may still have slight shaking)
Description:
1. Tuning supports motor tuning in keyboard operation mode, terminal mode and communication mode.
2. In order to ensure the optimal control performance of the frequency inverter during vector control, please
disconnect the load from the motor and use rotational tuning to self-learn the motor parameters; otherwise it will
affect the vector control effect. Please use static tuning 2 when the motor has a large inertia load which is not easy to
disengage and vector control is required.
3. Steps
3.1 Motor type and nameplate parameters F1-00
~
F1-05 must be set correctly.
3.2 F1 - 29 = 1 or 2 or 3. The panel displays the word STUDY at this time.
Содержание HV480 Series
Страница 1: ...HV610 Series Frequency Inverter User Manual HNC Electric Limited ...
Страница 12: ...8 2 2 3 Frequency inverter control loop terminal description ...
Страница 13: ...9 ...
Страница 166: ...162 Appendix II Plastic shell dimensions and mounting dimensions Fig 1 R75G3 2R2G3 Fig 2 004G3 7R5G3 ...
Страница 167: ...163 Appendix III dimensions and mounting dimensions of sheet metal machines Fig 3 011G3 200G3 Fig 4 185G3 560G3 ...