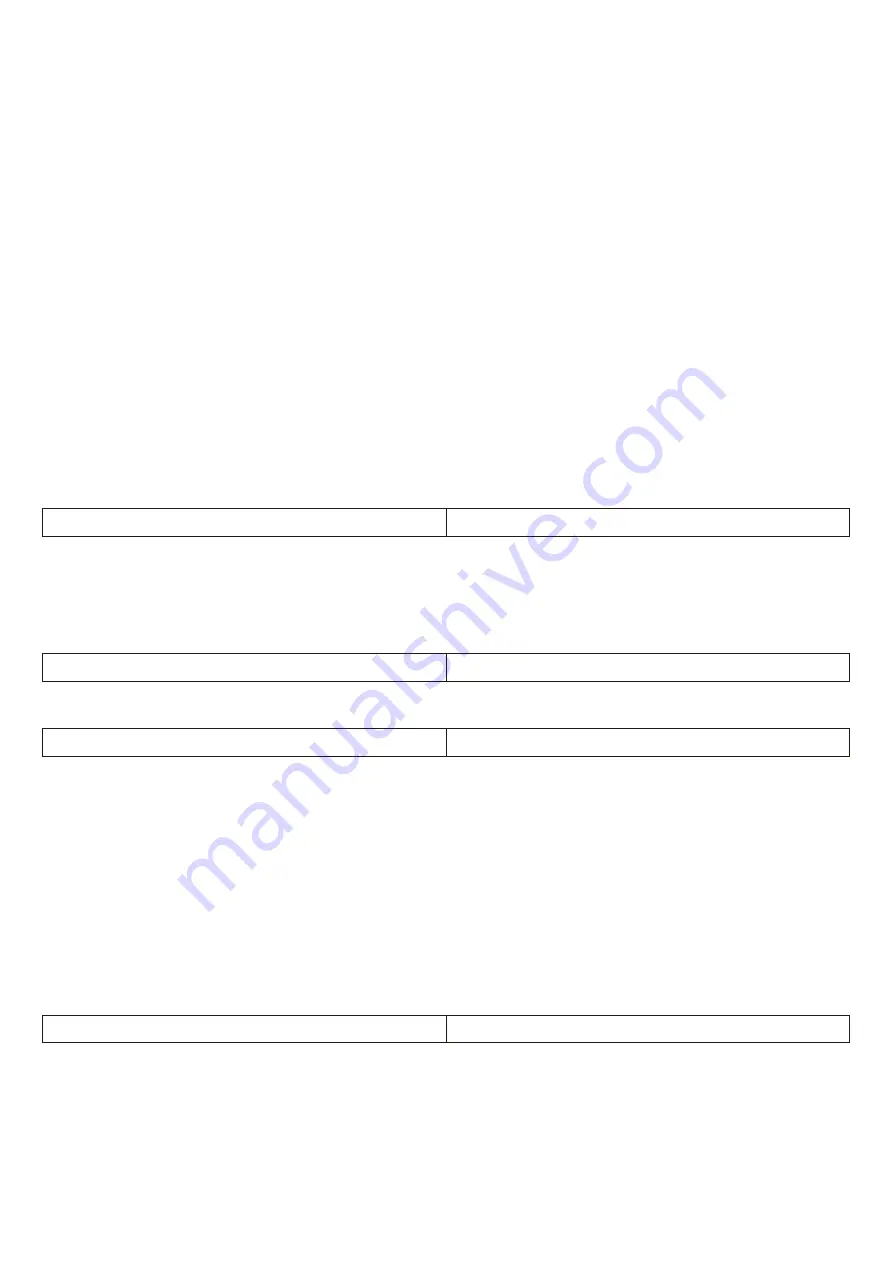
56
8. PID
The output of process PID control is selected as the operating frequency. It is generally used in field closed-loop
control of process, such as constant pressure closed-loop control and constant tension closed-loop control.
When applying PID as the frequency source, the relevant parameters of FA group “PID function" need to be set.
9. Communication given
Refers to the frequency given by the communication method
The upper computer gives the data through the communication address 0x1000. The data format is
-100.00 %~100.00 %, and 100.00 % refers to the percentage of the maximum frequency F0 - 16.
10. Panel potentiometer given
Given that the panel potentiometer is used as the frequency source, the JP1 jumper in the upper left corner of
the main board needs to be connected to the “JP" terminal. Rotary panel potential the device corresponds to 0 Hz at
the leftmost end and rotates to the rightmost end corresponding to F0 - 16 maximum frequency, which is also limited
by the upper limit frequency F0 - 18.
Whether the frequency display is not 0 when the potentiometer is rotated at the far left end, F5 - 71 will be
slightly increased at this time.
If the potentiometer is rotated at the far right end, the frequency display is not the maximum frequency, then
fine-tune and reduce F5 - 72 appropriately.
Note: when using the potentiometer keyboard, the AI3 terminal function on the main control panel will fail. If you
need AI function, please select AI1 / AI2.
F0 - 04 reverse control prohibited
0
~
1 [0]
0: motor allows reverse rotation
1: the motor is not allowed to reverse.
In fact, negative frequency is prohibited. When reverse operation is prohibited and reverse operation is
prohibited, the frequency inverter keeps running at 0 Hz.
F0 - 04 = 1 should be set when the motor is not allowed to rotate reversely.
F0 - 05 phase sequence direction
0
~
1 [0]
0: standard phase sequence.
1: carry out phase sequence exchange. (The direction of rotation of the motor changes)
F0 - 06 start protection selection
0
~
1 [0]
0: start unprotects. As long as there is a start command and there is no fault, the frequency inverter will output
and run.
1: start protection.
If the operation command of the frequency inverter is valid at power-up time (for example, the terminal operation
command is closed before power - up), then the frequency inverter will not respond to the operation command,
You must remove the operation command once before the frequency inverter responds.
If the operation command is valid at the time of frequency inverter fault reset and the frequency inverter does not
respond to the operation command, the operation command must be removed before the operation protection state
can be eliminated.
It can prevent the danger caused by the motor responding to the operation command when the motor is powered on
or when the fault is reset without knowing.
F0 - 07 jog. K key function selection
0
~
4 [0]
The JOG.K key is a multi-function key. The function of the JOG.K key can be set through this function code. This key
can be used to switch between shutdown and operation.
0: this key has no function.
1: keyboard command and remote operation switch. It refers to the switch of command source, that is, the
switch between current command source and keyboard control (local operation). If the current command source is
keyboard - controlled, this key function is invalid.
Содержание HV480 Series
Страница 1: ...HV610 Series Frequency Inverter User Manual HNC Electric Limited ...
Страница 12: ...8 2 2 3 Frequency inverter control loop terminal description ...
Страница 13: ...9 ...
Страница 166: ...162 Appendix II Plastic shell dimensions and mounting dimensions Fig 1 R75G3 2R2G3 Fig 2 004G3 7R5G3 ...
Страница 167: ...163 Appendix III dimensions and mounting dimensions of sheet metal machines Fig 3 011G3 200G3 Fig 4 185G3 560G3 ...