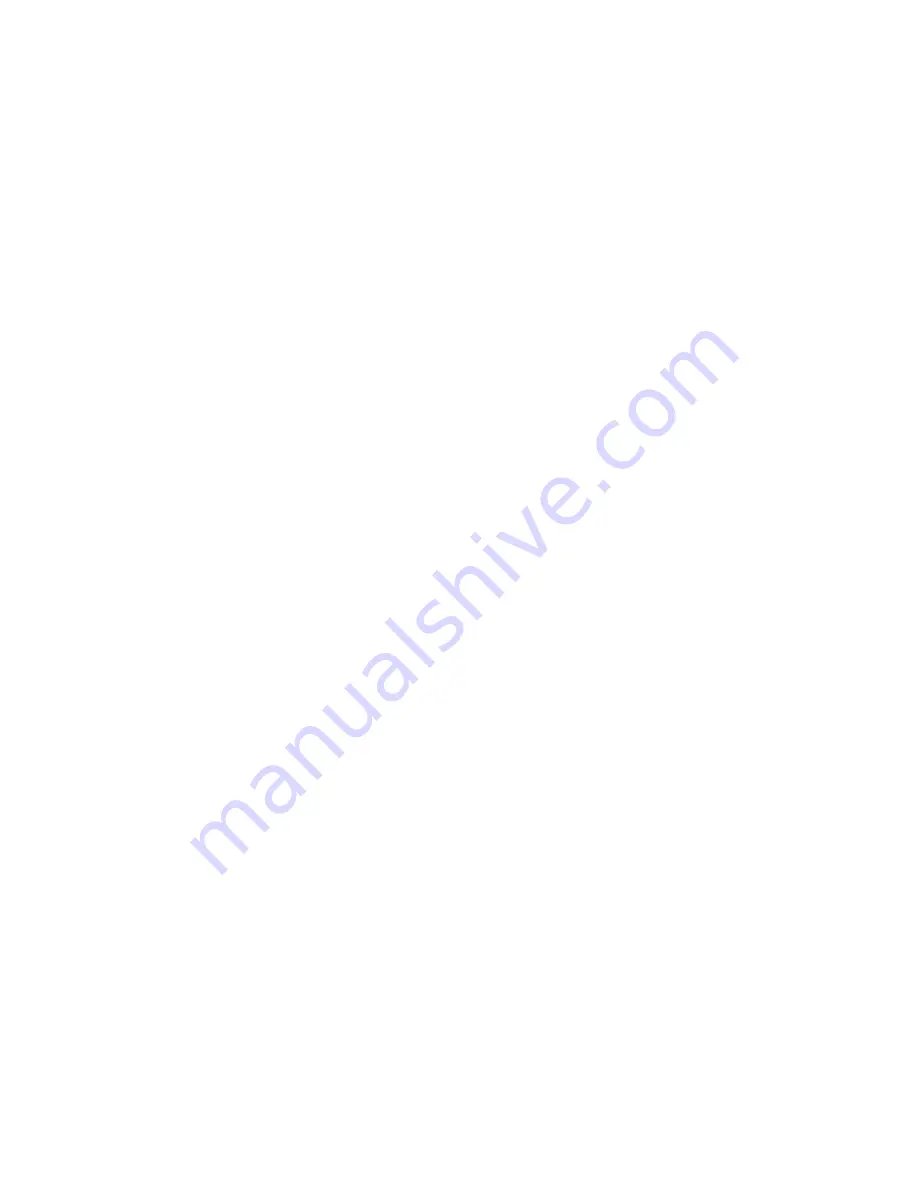
2.6 Control to the Fan ....................................................................................................................... 39
2.7 Control to the 4-way Valve .......................................................................................................... 40
2.8 Control to the Water Pump ......................................................................................................... 40
2.9 Control the Electrostatic Expansion Valve .................................................................................. 40
2.10 Protection Control ..................................................................................................................... 40
3 Controller ............................................................................................................................................... 41
3.1 General........................................................................................................................................ 41
3.2 Operation Instructions ................................................................................................................. 43
3.3 Intelligent Control ........................................................................................................................ 70
UNIT INSTALLATION
.............................................................................................................................. 82
1. Installation Guides ................................................................................................................................ 83
1.1 Installation Position ..................................................................................................................... 84
1.2 Matters Need Attention ............................................................................................................... 84
2 Filed Supplied Pipes and Valves........................................................................................................... 85
3 Service Tools ......................................................................................................................................... 86
4 Instalaltion Instructions .......................................................................................................................... 87
4.1 Installation Examples .................................................................................................................. 87
4.2 Pre-Installation ............................................................................................................................ 89
4.3 Selection of Installation Location ................................................................................................ 90
4.4 Outline Dimension of Outdoor Unit ............................................................................................. 91
4.5 Installation of Monobolc Unit ....................................................................................................... 92
4.6 Installation of Hydraulic Unit ....................................................................................................... 93
4.7 Installation of Water Tank ........................................................................................................... 96
4.8 Request of water quality ............................................................................................................. 99
4.9 Electric Wiring ........................................................................................................................... 100
4.10 Wiring of the Terminal Board .................................................................................................. 101
4.11 Wiring of the 2-Way Valve ...................................................................................................... 103
4.12 Wiring of the 3-Way Valve ...................................................................................................... 103
4.13 Wiring of Other Thermal .......................................................................................................... 104
4.14 Wiring of Optional Electric Heater ........................................................................................... 106
4.15 Wiring of the Gate-Controller .................................................................................................. 107
4.16 Wiring of the Remote Air Temperature Sensor ...................................................................... 108
4.17 Wiring of the Thermostat......................................................................................................... 109
4.18 Wiring of the Control ............................................................................................................... 109
5 Commissioning and Trial Run ............................................................................................................. 110
5.1 Check before startup ................................................................................................................. 110
5.2 Test run ..................................................................................................................................... 111
TEST OPERATION & TROUBLESHOOTING & MAINTENANCE
....................................................... 113
1 Trial Run .............................................................................................................................................. 114
1.1 Check for Wiring........................................................................................................................ 114
1.2 Check for the Water System ..................................................................................................... 114
1.3 Check for the Communication System ..................................................................................... 114
1.4 Trial Run .................................................................................................................................... 114
2 Error Code List .................................................................................................................................... 114
3 Flow Chart of Troubleshooting ............................................................................................................ 117
3.1 Comp High-pressure Protection E1 .......................................................................................... 117
Содержание VERSATI III Series
Страница 1: ...VERSATI Ⅲ Air To Water Heat Pump ...
Страница 5: ...Engineering Data ENGINEERING DATA ...
Страница 10: ...Engineering Data 1 4 Operating Principle 1 4 1 Schematic Diagram ...
Страница 22: ...Design and Selection DESIGN SELECTION ...
Страница 33: ...Unit Control UNIT CONTROL ...
Страница 72: ...Unit Control ...
Страница 76: ...Unit Control 3 3 2 Setting of Main Functions 1 Set mode and temperature ...
Страница 77: ...Unit Control 2 Click Func at the left lower corner in device operation interface to enter advanced settings ...
Страница 79: ...Unit Control 3 3 3 2 Help Click Help and view the operation instructions of the APP ...
Страница 80: ...Unit Control ...
Страница 81: ...Unit Control 3 3 3 3 Feedback Click Feedback to submit feedback ...
Страница 82: ...Installation UNIT INSTALLATION ...
Страница 113: ...Test Operation Troubleshooting Maintenance TEST OPERATION TROUBLESHOOTING MAINTENANCE ...
Страница 117: ...Test Operation Troubleshooting Maintenance 3 Flow Chart of Troubleshooting 3 1 Comp High pressure Protection E1 ...
Страница 118: ...Test Operation Troubleshooting Maintenance 3 2 Comp Low pressure Protection E3 ...
Страница 119: ...Test Operation Troubleshooting Maintenance 3 3 Comp Discharge Temp Protection E4 ...
Страница 120: ...Test Operation Troubleshooting Maintenance 3 4 Overload Protection of Compressor or Driver Error ...
Страница 121: ...Test Operation Troubleshooting Maintenance 3 5 DC Fan Error EF 3 6 Temperature Sensor Error ...
Страница 122: ...Test Operation Troubleshooting Maintenance 3 7 Communication Malfunction E6 ...
Страница 123: ...Test Operation Troubleshooting Maintenance 3 8 Capacity Switch Error Code C5 ...
Страница 125: ...Test Operation Troubleshooting Maintenance IPM or PFC Over temperature Protection Code P8 ...
Страница 127: ...Test Operation Troubleshooting Maintenance ...
Страница 135: ...Test Operation Troubleshooting Maintenance ...