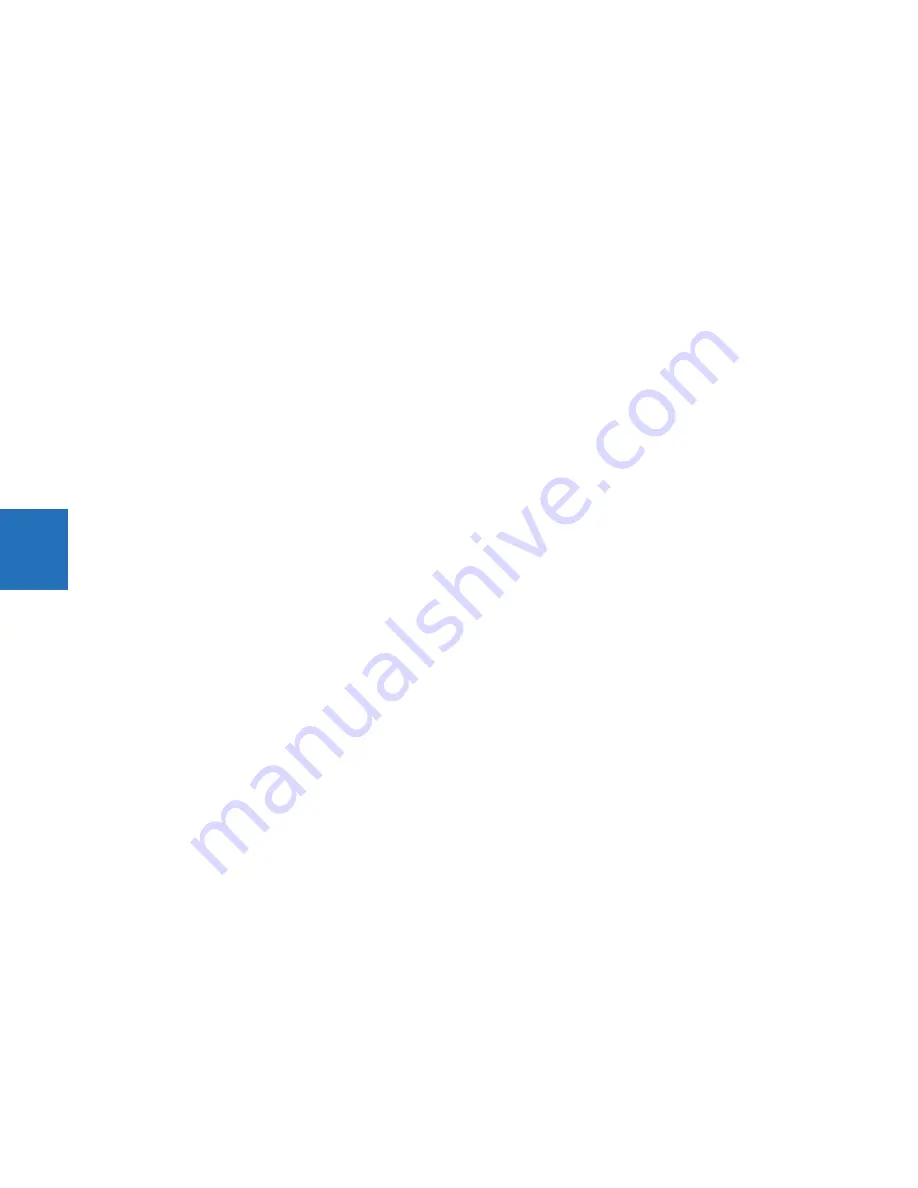
5-240
L90 LINE CURRENT DIFFERENTIAL SYSTEM – INSTRUCTION MANUAL
GROUPED ELEMENTS
CHAPTER 5: SETTINGS
5
GND DIST Z1 DIR RCA
— Selects the characteristic angle (or maximum torque angle) of the directional supervising function. If
the mho shape is applied, the directional function is an extra supervising function, as the dynamic mho characteristic itself
is a directional one. In conjunction with the quadrilateral shape selection, this setting defines the only directional function
built into the ground distance element. The directional function uses memory voltage for polarization.
GND DIST Z1 DIR COMP LIMIT
— This setting selects the comparator limit angle for the directional supervising function.
GND DIST Z1 QUAD RGT BLD
— This setting defines the right blinder position of the quadrilateral characteristic along the
resistive axis of the impedance plane (see the Quadrilateral Distance Characteristic figure). The angular position of the
blinder is adjustable with the use of the
GND DIST Z1 QUAD RGT BLD RCA
setting. This setting applies only to the quadrilateral
characteristic; set it with consideration to the maximum load current and required resistive coverage.
GND DIST Z1 QUAD RGT BLD RCA
— This setting defines the angular position of the right blinder of the quadrilateral
characteristic (see the Quadrilateral Distance Characteristic figure).
GND DIST Z1 QUAD LFT BLD
— This setting defines the left blinder position of the quadrilateral characteristic along the
resistive axis of the impedance plane (see the Quadrilateral Distance Characteristic figure). The angular position of the
blinder is adjustable with the use of the
GND DIST Z1 QUAD LFT BLD RCA
setting. This setting applies only to the quadrilateral
characteristic; set it with consideration to the maximum load current.
GND DIST Z1 QUAD LFT BLD RCA
— This setting defines the angular position of the left blinder of the quadrilateral
characteristic (see the Quadrilateral Distance Characteristic figure).
GND DIST Z1 SUPV
— The ground distance elements are supervised by the magnitude of the neutral (3I_0) current. Set the
current supervision pickup to be less than the minimum 3I_0 current for the end of the zone fault, taking into account the
required fault resistance coverage to prevent maloperation due to VT fuse failure. Settings less than 0.2 pu are not
recommended, so apply them with caution. To enhance ground distance security against spurious neutral current during
switch-off transients, three-phase faults, and phase-to-phase faults, a positive-sequence current restraint of 5% is applied
to the neutral current supervision magnitude. Set this setting at least three times the
CURRENT CUTOFF LEVEL
setting
specified in the
PRODUCT SETUP
DISPLAY PROPERTIES
menu.
GND DIST Z1 VOLT LEVEL
— This setting is relevant for applications on series-compensated lines, or in general, if series
capacitors are located between the relaying point and a point for which the zone shall not overreach. For plain (non-
compensated) lines, set it to zero. Otherwise, the setting is entered in per unit of the VT bank configured under the
DISTANCE SOURCE
. Effectively, this setting facilitates dynamic current-based reach reduction. In non-directional
applications (
GND DIST Z1 DIR
set to “Non-directional”), this setting applies only to the forward reach of the non-directional
zone. See the Application of Settings chapter for details and information on calculating this setting value for applications
on series compensated lines.
GND DIST Z1 DELAY
— This setting enables the user to delay operation of the distance elements and implement a stepped
distance backup protection. The distance element timer applies a short drop-out delay to cope with faults located close to
the boundary of the zone when small oscillations in the voltages or currents can inadvertently reset the timer.
GND DIST Z1 BLK
— This setting enables the user to select a FlexLogic operand to block the given ground distance element.
VT fuse fail detection is one of the applications for this setting.
Содержание L90
Страница 14: ...1 4 L90 LINE CURRENT DIFFERENTIAL SYSTEM INSTRUCTION MANUAL FOR FURTHER ASSISTANCE CHAPTER 1 INTRODUCTION 1 ...
Страница 68: ...2 54 L90 LINE CURRENT DIFFERENTIAL SYSTEM INSTRUCTION MANUAL SPECIFICATIONS CHAPTER 2 PRODUCT DESCRIPTION 2 ...
Страница 136: ...3 68 L90 LINE CURRENT DIFFERENTIAL SYSTEM INSTRUCTION MANUAL CONNECT TO D400 GATEWAY CHAPTER 3 INSTALLATION 3 ...
Страница 224: ...4 88 L90 LINE CURRENT DIFFERENTIAL SYSTEM INSTRUCTION MANUAL FLEXLOGIC DESIGN USING ENGINEER CHAPTER 4 INTERFACES 4 ...
Страница 692: ...6 36 L90 LINE CURRENT DIFFERENTIAL SYSTEM INSTRUCTION MANUAL PRODUCT INFORMATION CHAPTER 6 ACTUAL VALUES 6 ...
Страница 708: ...7 16 L90 LINE CURRENT DIFFERENTIAL SYSTEM INSTRUCTION MANUAL TARGETS MENU CHAPTER 7 COMMANDS AND TARGETS 7 ...
Страница 742: ...9 6 L90 LINE CURRENT DIFFERENTIAL SYSTEM INSTRUCTION MANUAL TESTING CHAPTER 9 COMMISSIONING 9 ...
Страница 804: ...10 62 L90 LINE CURRENT DIFFERENTIAL SYSTEM INSTRUCTION MANUAL FAULT LOCATOR CHAPTER 10 THEORY OF OPERATION 10 ...
Страница 872: ...C 6 L90 LINE CURRENT DIFFERENTIAL SYSTEM INSTRUCTION MANUAL COMMAND LINE INTERFACE APPENDIX C COMMAND LINE INTERFACE C ...
Страница 878: ...D 6 L90 LINE CURRENT DIFFERENTIAL SYSTEM INSTRUCTION MANUAL REVISION HISTORY APPENDIX D MISCELLANEOUS D ...
Страница 882: ...iv L90 LINE CURRENT DIFFERENTIAL SYSTEM INSTRUCTION MANUAL ABBREVIATIONS ...
Страница 900: ...xviii L90 LINE CURRENT DIFFERENTIAL SYSTEM INSTRUCTION MANUAL INDEX ...