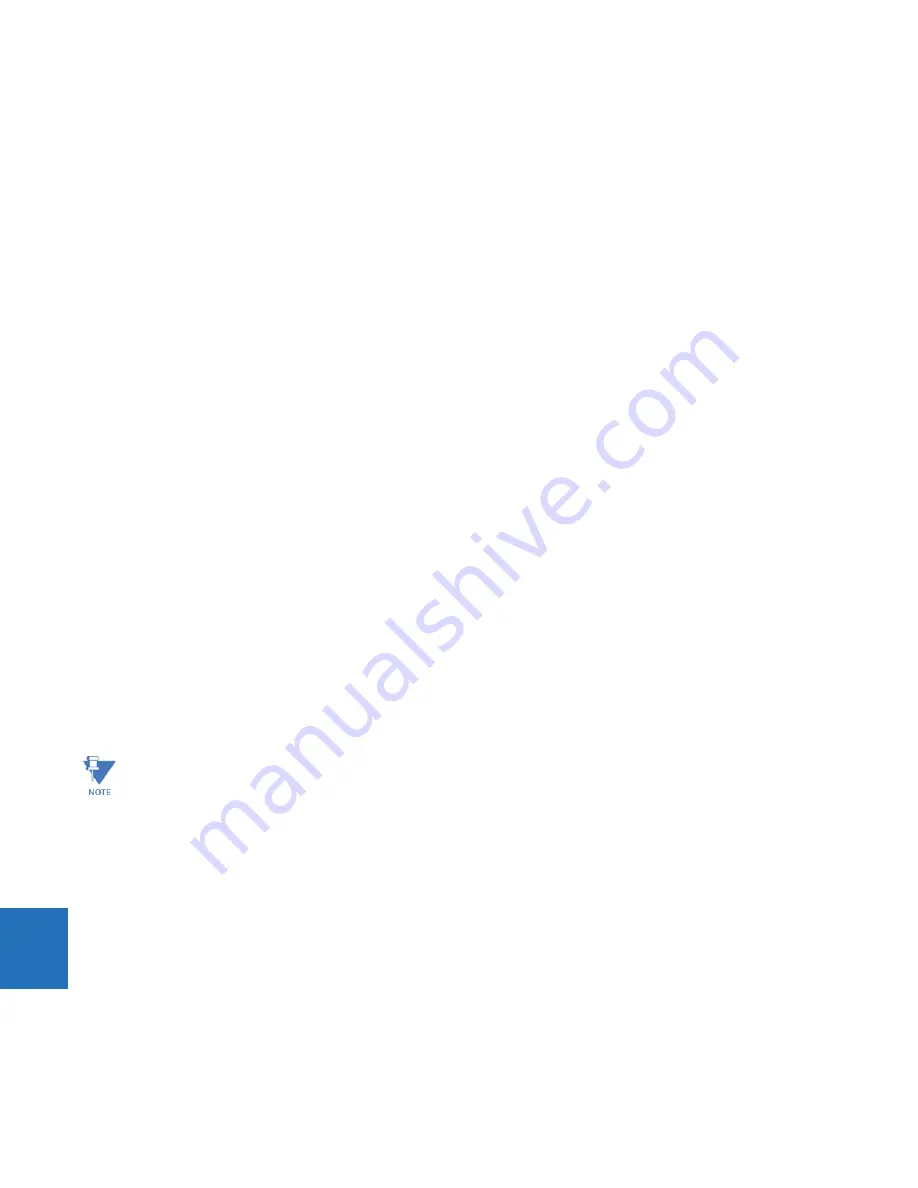
9-2
L30 LINE CURRENT DIFFERENTIAL SYSTEM – INSTRUCTION MANUAL
TESTING
CHAPTER 9: COMMISSIONING
9
Expected result — In a few seconds “Yes” changes to “Local Loopback Test PASSED” and then to “No”, signifying the
test was successfully completed and the communication modules operated properly.
11. If Channel 2 is used, make the following setting change and repeat Step 10 for Channel 2 as performed for channel 1:
TESTING
CHANNEL TESTS
LOCAL LOOPBACK TEST
LOCAL LOOPBACK CHANNEL NUMBER
: "2"
12. Verify and record that the Local Loopback Test was performed properly with the following status check:
ACTUAL VALUES
STATUS
CHANNEL TESTS
CHANNEL 1(2) LOCAL LOOPBACK STATUS
: "OK"
13. Make the following setting change in one of the relays:
TESTING
CHANNEL TESTS
REMOTE LOOPBACK TEST
REMOTE LOOPBACK CHANNEL NUMBER
: "1"
14. Initiate the Remote Loopback Channel Tests by making the following setting change:
TESTING
CHANNEL TESTS
REMOTE LOOPBACK
REMOTE LOOPBACK FUNCTION
: "Yes"
Expected result — The “Running Remote Loopback Test” message appears; within 60 to 100 seconds, the “Remote
Loopback Test PASSED” message appears for a few seconds and then changes to “No”, signifying that the test
successfully completed and communications with the relay were successfully established. The “Remote Loopback
Test FAILED” message indicates that either the communication link quality does not meet requirements (BER less than
10–4) or the channel is not established – check the communications link connections.
15. If Channel 2 is used, make the following setting change and repeat Step 14 for Channel 2 as performed for Channel 1:
TESTING
CHANNEL TESTS
REMOTE LOOPBACK TEST
REMOTE LOOPBACK CHANNEL NUMBER
: "2"
16. Verify and record the Remote Loopback Test was performed properly with the following status check:
ACTUAL VALUES
STATUS
CHANNEL TESTS
CHANNEL 1(2) REMOTE LOOPBACK STATUS
: "OK"
17. Verify and record that Remote Loopback Test fails during communications failures as follows: start test as per Steps
13 to 14 and in two to five seconds disconnect the fiber Rx cable on the corresponding channel.
Expected result — The "Running Remote Loopback Test" message appears. When the channel is momentarily cut off,
the "Remote Loopback Test FAILED" message displays. The status check reads as follows:
ACTUAL VALUES
STATUS
CHANNEL TESTS
CHANNEL 1(2) LOCAL LOOPBACK STATUS
: "Fail"
18. Re-connect the fiber Rx cable. Repeat Steps 13 to 14 and verify that Remote Loopback Test performs properly again.
19. Verify and record that Remote Loopback Test fails if communications are not connected properly by disconnecting the
fiber Rx cable and repeating Steps 13 to 14.
Expected result — The
ACTUAL VALUES
STATUS
CHANNEL TESTS
CHANNEL 1(2) REMOTE LOOPBACK TEST
: "Fail"
message is constantly on the display.
20. Repeat Steps 13 to 14 and verify that Remote Loopback Test is correct.
21. Make the following setting change in both relays:
TESTING
TEST MODE
: "Disabled"
9.1.2 Clock synchronization tests
The 87L clock synchronization is based upon a peer-to-peer architecture in which all relays are Masters. The relays are
synchronized in a distributed fashion. The clocks are phase-synchronized to each other and frequency-synchronized to the
power-system frequency. The performance requirement for the clock synchronization is a maximum error of ±130
μ
s.
All tests are verified by using PFLL status displays. All PFLL status displays must be either OK or Fail.
1.
Ensure that Steps 1 through 7 inclusive of the previous section are completed.
2.
Verify and record that both relays have established communications with the following checks after 60 to 120
seconds:
ACTUAL VALUES
STATUS
CHANNEL TESTS
CHANNEL 1(2) STATUS
: “OK”
ACTUAL VALUES
STATUS
CHANNEL TESTS
REMOTE LOOPBACK STATUS
: “n/a”
ACTUAL VALUES
STATUS
CHANNEL TESTS
PFLL STATUS
: “OK”
During channel tests, verify in the
ACTUAL VALUES
STATUS
CHANNEL TESTS
CHANNEL 1(2) LOST PACKETS
display that the values are very low or even 0. If values are comparatively high, check the settings of
communications equipment (if applicable).
Содержание L30
Страница 10: ...x L30 LINE CURRENT DIFFERENTIAL SYSTEM INSTRUCTION MANUAL TABLE OF CONTENTS ...
Страница 14: ...1 4 L30 LINE CURRENT DIFFERENTIAL SYSTEM INSTRUCTION MANUAL FOR FURTHER ASSISTANCE CHAPTER 1 INTRODUCTION 1 ...
Страница 126: ...3 68 L30 LINE CURRENT DIFFERENTIAL SYSTEM INSTRUCTION MANUAL CONNECT TO D400 GATEWAY CHAPTER 3 INSTALLATION 3 ...
Страница 214: ...4 88 L30 LINE CURRENT DIFFERENTIAL SYSTEM INSTRUCTION MANUAL FLEXLOGIC DESIGN USING ENGINEER CHAPTER 4 INTERFACES 4 ...
Страница 582: ...7 16 L30 LINE CURRENT DIFFERENTIAL SYSTEM INSTRUCTION MANUAL TARGETS MENU CHAPTER 7 COMMANDS AND TARGETS 7 ...
Страница 598: ...9 6 L30 LINE CURRENT DIFFERENTIAL SYSTEM INSTRUCTION MANUAL TESTING CHAPTER 9 COMMISSIONING 9 ...
Страница 622: ...10 24 L30 LINE CURRENT DIFFERENTIAL SYSTEM INSTRUCTION MANUAL FAULT LOCATOR CHAPTER 10 THEORY OF OPERATION 10 ...
Страница 670: ...A 18 L30 LINE CURRENT DIFFERENTIAL SYSTEM INSTRUCTION MANUAL FLEXANALOG ITEMS APPENDIX A FLEXANALOG OPERANDS A ...
Страница 678: ...C 6 L30 LINE CURRENT DIFFERENTIAL SYSTEM INSTRUCTION MANUAL COMMAND LINE INTERFACE APPENDIX C COMMAND LINE INTERFACE C ...
Страница 682: ...D 4 L30 LINE CURRENT DIFFERENTIAL SYSTEM INSTRUCTION MANUAL REVISION HISTORY APPENDIX D MISCELLANEOUS D ...
Страница 686: ...iv L30 LINE CURRENT DIFFERENTIAL SYSTEM INSTRUCTION MANUAL ABBREVIATIONS ...