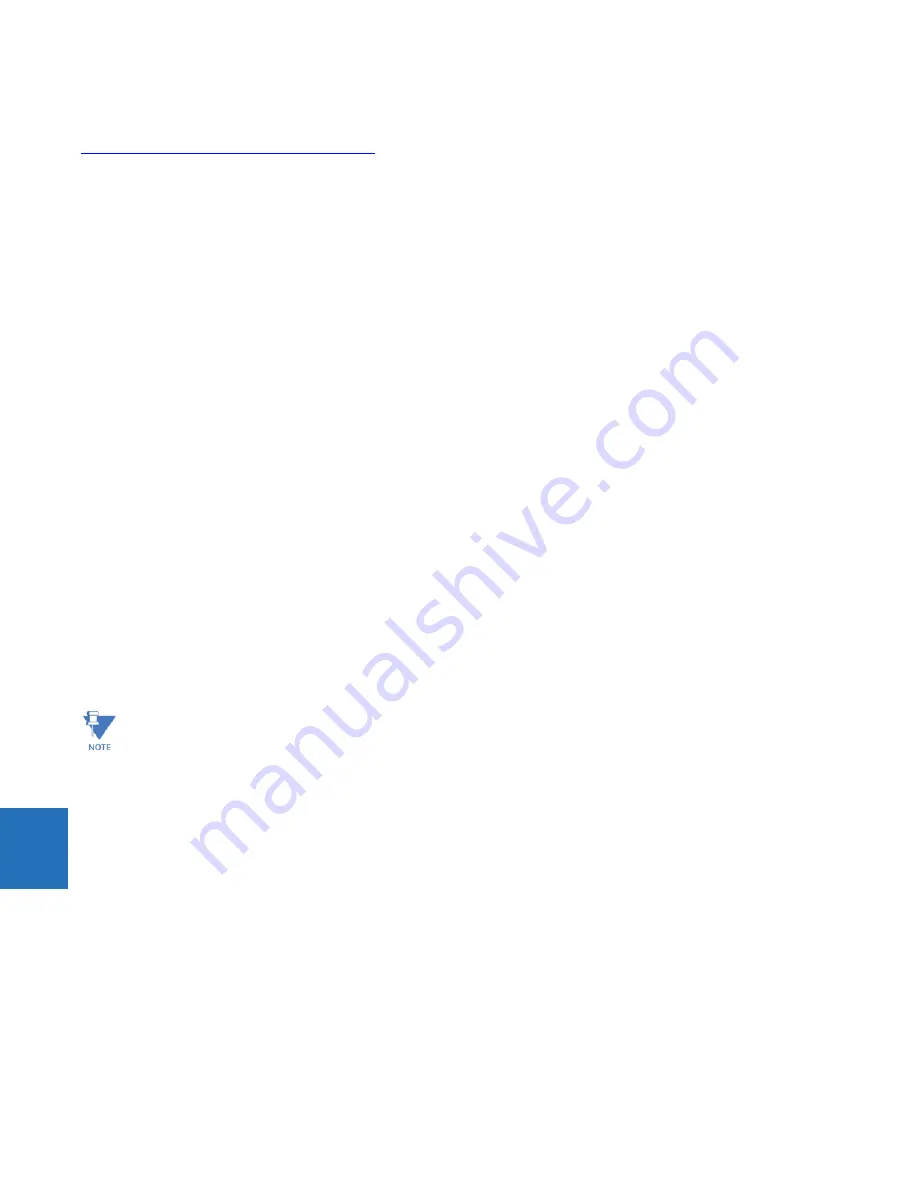
8-4
L30 LINE CURRENT DIFFERENTIAL SYSTEM – INSTRUCTION MANUAL
CURRENT DIFFERENTIAL (87L) SETTINGS
CHAPTER 8: APPLICATION OF SETTINGS
8
This software program is also useful for establishing test parameters. It is strongly recommended this program be
downloaded. Look for the "L90 Test Tool" on the GE Grid Solutions website, for example in the L90 support documents at
http://www.gegridsolutions.com/support/l90.htm
The differential characteristic is defined by four settings:
CURRENT DIFF PICKUP
,
CURRENT DIFF RESTRAINT 1
,
CURRENT DIFF
RESTRAINT 2
, and
CURRENT DIFF BREAK PT
(breakpoint). As is typical for current-based differential elements, the settings are
a trade-off between operation on internal faults against restraint during external faults.
8.2.2 Current differential pickup
This setting establishes the sensitivity of the element to high impedance faults, and it is therefore good to choose a low
level, but this can cause maloperation for an external fault causing CT saturation. The selection of this setting is influenced
by the decision to use charging current compensation. If charging current compensation is Enabled, set pickup to a
minimum of 150% of the steady-state line charging current, to a lower limit of 10% of CT rating. If charging current
compensation is Disabled, set pickup to a minimum of 250% of the steady-state line charging current to a lower limit of
10% of CT rating.
If the CT at one terminal can saturate while the CTs at other terminals do not, increase this setting by approximately 20 to
50% (depending on how heavily saturated the one CT is while the other CTs are not saturated) of CT rating to prevent
operation on a close-in external fault.
8.2.3 Current differential restraint 1
The
CURRENT DIFF RESTRAINT 1
setting controls the element characteristic when current is below the breakpoint, where CT
errors and saturation effects are not expected to be significant. The setting is used to provide sensitivity to high
impedance internal faults, or when system configuration limits the fault current to low values. A setting of 10 to 20% is
appropriate in most cases, but increase this to 30% if the CTs can perform quite differently during faults.
8.2.4 Current differential restraint 2
The
CURRENT DIFF RESTRAINT 2
setting controls the element characteristic when current is above the breakpoint, where CT
errors and saturation effects are expected to be significant. The setting is used to provide security against high current
external faults. A setting of 30 to 40% is appropriate in most cases, but increase this to 70% if the CTs can perform quite
differently during faults.
8.2.5 Current differential break point
The
CURRENT DIFF BREAK PT
setting controls the threshold where the relay changes from using the restraint 1 to the
restraint 2 characteristics. Two approaches can be considered, as follows:
•
Program the setting to 150 to 200% of the maximum emergency load current on the line, on the assumption that a
maintained current above this level is a fault
•
Program the setting below the current level where CT saturation and spurious transient differential currents can be
expected
The first approach gives comparatively more security and less sensitivity; the second approach provides less security for
more sensitivity.
8.2.6 CT tap
If the CT ratios at the line terminals are different, the
CURRENT DIFF CT TAP 1(2)
setting must be used to correct the ratios to
a common base. In this case, modify the
CURRENT DIFF BREAK PT
and
CURRENT DIFF PICKUP
settings because the local
current phasor is used as a reference to determine which differential equation is used, based on the value of local and
Assigning the same value to the
CURRENT DIFF RESTRAINT 1(2)
settings reverts dual slope bias characteristics into
single slope bias characteristics.
Содержание L30
Страница 10: ...x L30 LINE CURRENT DIFFERENTIAL SYSTEM INSTRUCTION MANUAL TABLE OF CONTENTS ...
Страница 14: ...1 4 L30 LINE CURRENT DIFFERENTIAL SYSTEM INSTRUCTION MANUAL FOR FURTHER ASSISTANCE CHAPTER 1 INTRODUCTION 1 ...
Страница 126: ...3 68 L30 LINE CURRENT DIFFERENTIAL SYSTEM INSTRUCTION MANUAL CONNECT TO D400 GATEWAY CHAPTER 3 INSTALLATION 3 ...
Страница 214: ...4 88 L30 LINE CURRENT DIFFERENTIAL SYSTEM INSTRUCTION MANUAL FLEXLOGIC DESIGN USING ENGINEER CHAPTER 4 INTERFACES 4 ...
Страница 582: ...7 16 L30 LINE CURRENT DIFFERENTIAL SYSTEM INSTRUCTION MANUAL TARGETS MENU CHAPTER 7 COMMANDS AND TARGETS 7 ...
Страница 598: ...9 6 L30 LINE CURRENT DIFFERENTIAL SYSTEM INSTRUCTION MANUAL TESTING CHAPTER 9 COMMISSIONING 9 ...
Страница 622: ...10 24 L30 LINE CURRENT DIFFERENTIAL SYSTEM INSTRUCTION MANUAL FAULT LOCATOR CHAPTER 10 THEORY OF OPERATION 10 ...
Страница 670: ...A 18 L30 LINE CURRENT DIFFERENTIAL SYSTEM INSTRUCTION MANUAL FLEXANALOG ITEMS APPENDIX A FLEXANALOG OPERANDS A ...
Страница 678: ...C 6 L30 LINE CURRENT DIFFERENTIAL SYSTEM INSTRUCTION MANUAL COMMAND LINE INTERFACE APPENDIX C COMMAND LINE INTERFACE C ...
Страница 682: ...D 4 L30 LINE CURRENT DIFFERENTIAL SYSTEM INSTRUCTION MANUAL REVISION HISTORY APPENDIX D MISCELLANEOUS D ...
Страница 686: ...iv L30 LINE CURRENT DIFFERENTIAL SYSTEM INSTRUCTION MANUAL ABBREVIATIONS ...