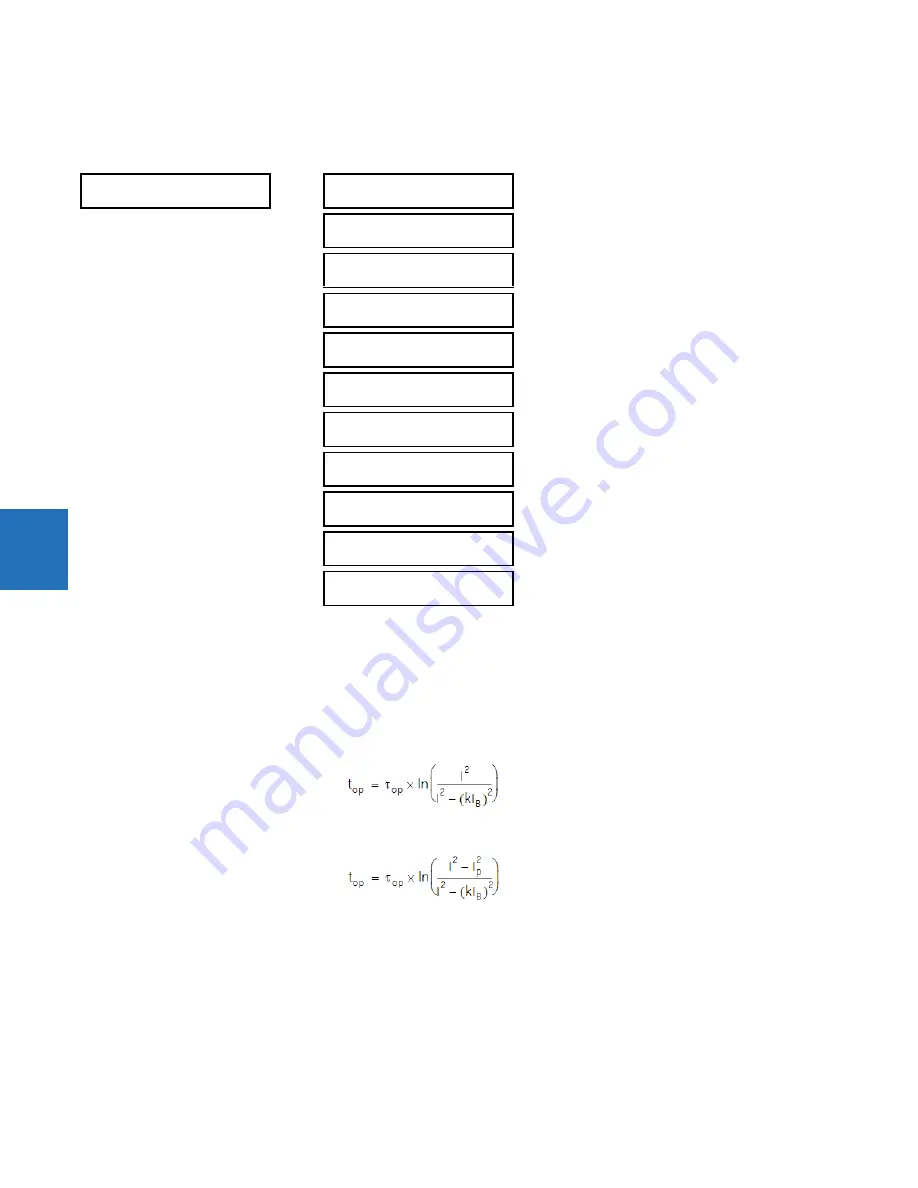
5-298
L30 LINE CURRENT DIFFERENTIAL SYSTEM – INSTRUCTION MANUAL
CONTROL ELEMENTS
CHAPTER 5: SETTINGS
5
5.8.11.6 Thermal overload protection (ANSI 49)
SETTINGS
CONTROL ELEMENTS
MONITORING ELEMENTS
THERMAL OVERLOAD PROTECTION
THERMAL PROTECTION 1(2)
The thermal overload protection element corresponds to the IEC 255-8 standard and is used to detect thermal overload
conditions in protected power system elements. Choosing an appropriate time constant element can be used to protect
different elements of the power system. The cold curve characteristic is applied when the estimated I
p
current is less than
10% of the base current. If I
p
current is greater or equal than 10% than the base current, then the hot curve characteristic
is applied. I
p
current is estimated with a fixed time constant for both cooling and heating that reaches to the final value in
two seconds on a step change (either step up or step down) signal.
The IEC255-8 cold curve is defined as follows:
Eq. 5-28
The IEC255-8 hot curve is defined as follows:
Eq. 5-29
where
t
op
= time to operate
τ
op
= thermal protection trip time constant
I = measured overload RMS current
I
p
= measured load RMS current before overload occurs
k = IEC 255-8 k-factor applied to I
B
, defining maximum permissible current above nominal current
I
B
= protected element base (nominal) current
THERMAL
PROTECTION 1
THERMAL PROTECTION 1
FUNCTION: Disabled
Range: Disabled, Enabled
THERMAL PROTECTION 1
SOURCE: SRC1
Range: SRC 1, SRC 2
THERMAL PROTECTION 1
BASE CURR: 0.80 pu
Range: 0.20 to 3.00 pu in steps of 0.01
THERMAL PROTECTION 1
k FACTOR: 1.10
Range: 1.00 to 1.20 in steps of 0.05
THERM PROT 1 TRIP
TIME CONST: 45 min
Range: 0 to 1000 min. in steps of 1
THERM PROT 1 RESET
TIME CONST: 45 min
Range: 0 to 1000 min. in steps of 1
THERM PROT 1 MINIM
RESET TIME: 20 min
Range: 0 to 1000 min. in steps of 1
THERM PROT 1 RESET:
Off
Range: FlexLogic operand
THERM PROT 1 BLOCK:
Off
Range: FlexLogic operand
THERMAL PROTECTION 1
TARGET: Self-reset
Range: Self-reset, Latched, Disabled
THERMAL PROTECTION 1
EVENTS: Disabled
Range: Disabled, Enabled
Содержание L30
Страница 10: ...x L30 LINE CURRENT DIFFERENTIAL SYSTEM INSTRUCTION MANUAL TABLE OF CONTENTS ...
Страница 14: ...1 4 L30 LINE CURRENT DIFFERENTIAL SYSTEM INSTRUCTION MANUAL FOR FURTHER ASSISTANCE CHAPTER 1 INTRODUCTION 1 ...
Страница 126: ...3 68 L30 LINE CURRENT DIFFERENTIAL SYSTEM INSTRUCTION MANUAL CONNECT TO D400 GATEWAY CHAPTER 3 INSTALLATION 3 ...
Страница 214: ...4 88 L30 LINE CURRENT DIFFERENTIAL SYSTEM INSTRUCTION MANUAL FLEXLOGIC DESIGN USING ENGINEER CHAPTER 4 INTERFACES 4 ...
Страница 582: ...7 16 L30 LINE CURRENT DIFFERENTIAL SYSTEM INSTRUCTION MANUAL TARGETS MENU CHAPTER 7 COMMANDS AND TARGETS 7 ...
Страница 598: ...9 6 L30 LINE CURRENT DIFFERENTIAL SYSTEM INSTRUCTION MANUAL TESTING CHAPTER 9 COMMISSIONING 9 ...
Страница 622: ...10 24 L30 LINE CURRENT DIFFERENTIAL SYSTEM INSTRUCTION MANUAL FAULT LOCATOR CHAPTER 10 THEORY OF OPERATION 10 ...
Страница 670: ...A 18 L30 LINE CURRENT DIFFERENTIAL SYSTEM INSTRUCTION MANUAL FLEXANALOG ITEMS APPENDIX A FLEXANALOG OPERANDS A ...
Страница 678: ...C 6 L30 LINE CURRENT DIFFERENTIAL SYSTEM INSTRUCTION MANUAL COMMAND LINE INTERFACE APPENDIX C COMMAND LINE INTERFACE C ...
Страница 682: ...D 4 L30 LINE CURRENT DIFFERENTIAL SYSTEM INSTRUCTION MANUAL REVISION HISTORY APPENDIX D MISCELLANEOUS D ...
Страница 686: ...iv L30 LINE CURRENT DIFFERENTIAL SYSTEM INSTRUCTION MANUAL ABBREVIATIONS ...