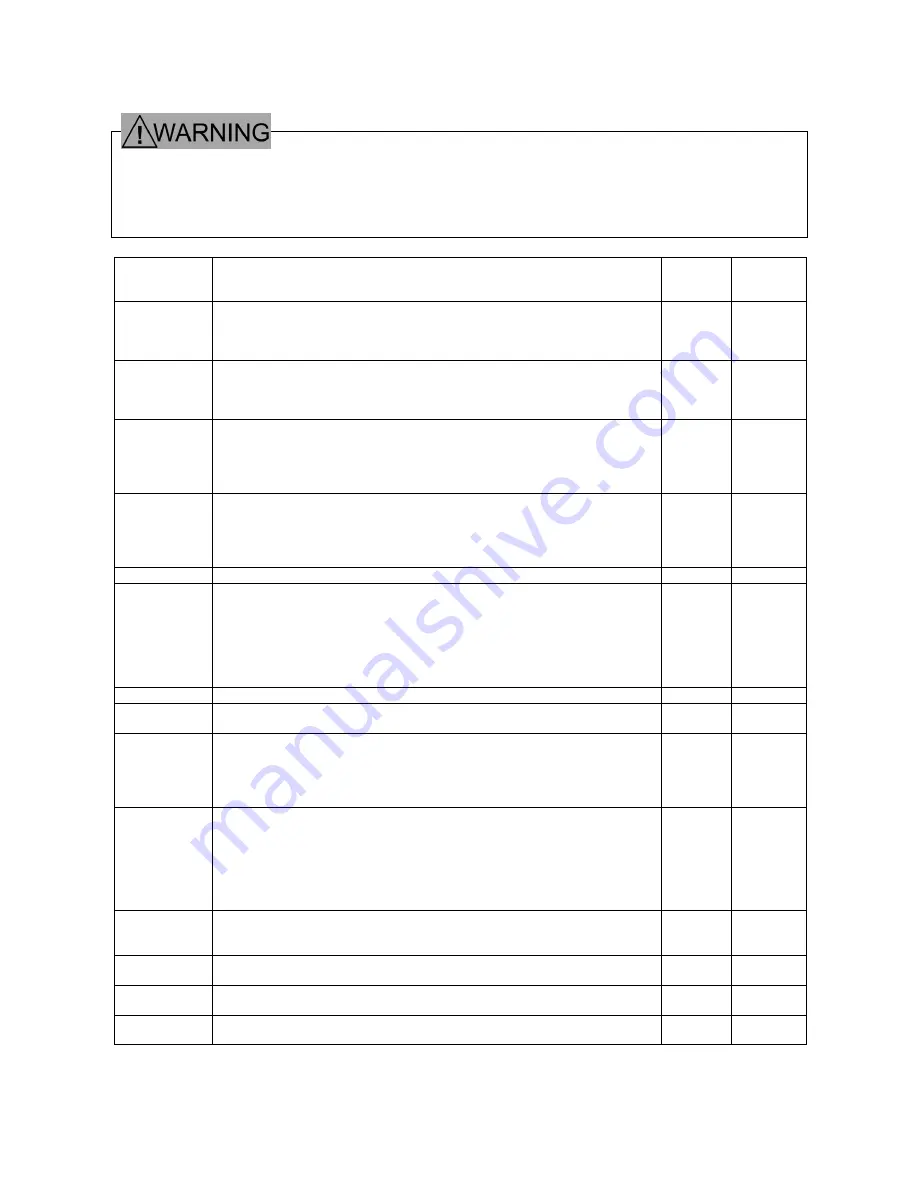
6-1
6. List of Inverter Protective Functions
·
The motor coasts when an alarm is issued. Install a brake on the driven machine side if you need to stop
the motor.
An accident may occur.
·
When you reset the inverter while applying the operation command, the motor restarts suddenly. Make
sure the operation command is turned off before you restart.
Function
Description
Display
Related
function
code
DB resistor
overheating
When the built-in braking resistor overheats, the inverter stops discharging and
running.
You must set the function codes E35 to 37 corresponding to the resistor (built-
in/external).
dbh
E35 - 37
DC fuse blown
When a fuse at the main DC circuit blows due to a short-circuit in the IGBT
circuit, the inverter stops operation. This function prevents secondary
disaster. A damage to the inverter is suspected and contact FUJI
immediately.
dcf
Ground fault
Activated by a ground fault in the inverter output circuit. If a large current
flows due to ground fault, the overcurrent protective function may operate to
protect the inverter. Connect a separate earth-leakage protection relay or an
earth-leakage circuit breaker for accident prevention such as human damage
and fire.
ef
Excessive
position
deviation
Activated when the position deviation between the reference and the detected
values exceeds the function code o18 "Excessive deviation value" in
synchronized operation.
The option code "o" becomes valid and is displayed on the KEYPAD panel
after installing options.
d0
o18
Memory error
Activated when a fault such as "write error" occurs in the memory.
er1
KEYPAD panel
communication
error
Activated if a communication error is detected between the inverter control
circuit and the KEYPAD panel when the start/stop command from the KEYPAD
is valid (function code F02
=
0).
Note: KEYPAD panel communication errors do not indicate the alarm display
and issue the alarm relay output when the inverter is operated by external
signal input or the link function.
The inverter continues operating.
er2
F02
CPU error
Activated when a CPU error occurs due to noise.
er3
Network error
Activated if a communication error occurs due to noise when the inverter is
operated through T- Link, SX bus or field bus.
er4
o30,31
RS485
communication
error
Activated if:
- RS485 communication error occurs while the function code H32 is set to 0 to
2.
- A disconnection continues for more than the specified period of 0.1 to 60.0
with the function code H38.
er5
H32,H33
H38
Operation
procedure error
Activated if multiple network options (T- Link, SX bus, and field bus) are
installed. Though you can install multiple SI, DI and PG options, this error is
issued if the two SW settings are identical.
Activated when you use H01 and H71 to start auto-tuning while either [BX],
[STOP1], [STOP2], or [STOP3] is ON. Activated when you do not turn ON the
FWD key on the KEYPAD panel for more than 20 sec after you selected the
auto-tuning operation of H01 and H71.
er6
Output wiring
error
Activated when the measured data are out of the motor characteristic data
range during executing tuning or the wires are not connected in the inverter
output circuit.
er7
H01,H71
A/D converter
error
Activated when an error occurs in the A/D converter circuit.
er8
Speed
disagreement
Activated when the deviation between the speed reference (speed setting) and
the motor speed (detected speed, predicted speed) becomes excessive.
er9
UPAC error
Activated when a hardware failure in the UPAC option, a communication error
with the controller part of the inverter or a backup battery exhaustion occurs.
era
Содержание 5000VG7S Series
Страница 7: ...0 6 Warning Label Position for Inside the Inverter...
Страница 23: ...2 5 Basic Wiring Diagram Figure 2 3 1 Basic Wiring Diagram...
Страница 36: ...2 18 l Control circuit terminals Control circuit terminals Screw size M3...
Страница 94: ...9 4 FS5941 40 47 Figure 9 1 FS5941 60 52 FS5941 86 52 Figure 9 2...
Страница 96: ...9 6 RF3280 F11 RF3400 F11 Figure 9 5 RF3880 F11 Figure 9 6 6 6 Figure 9 7 F200160...