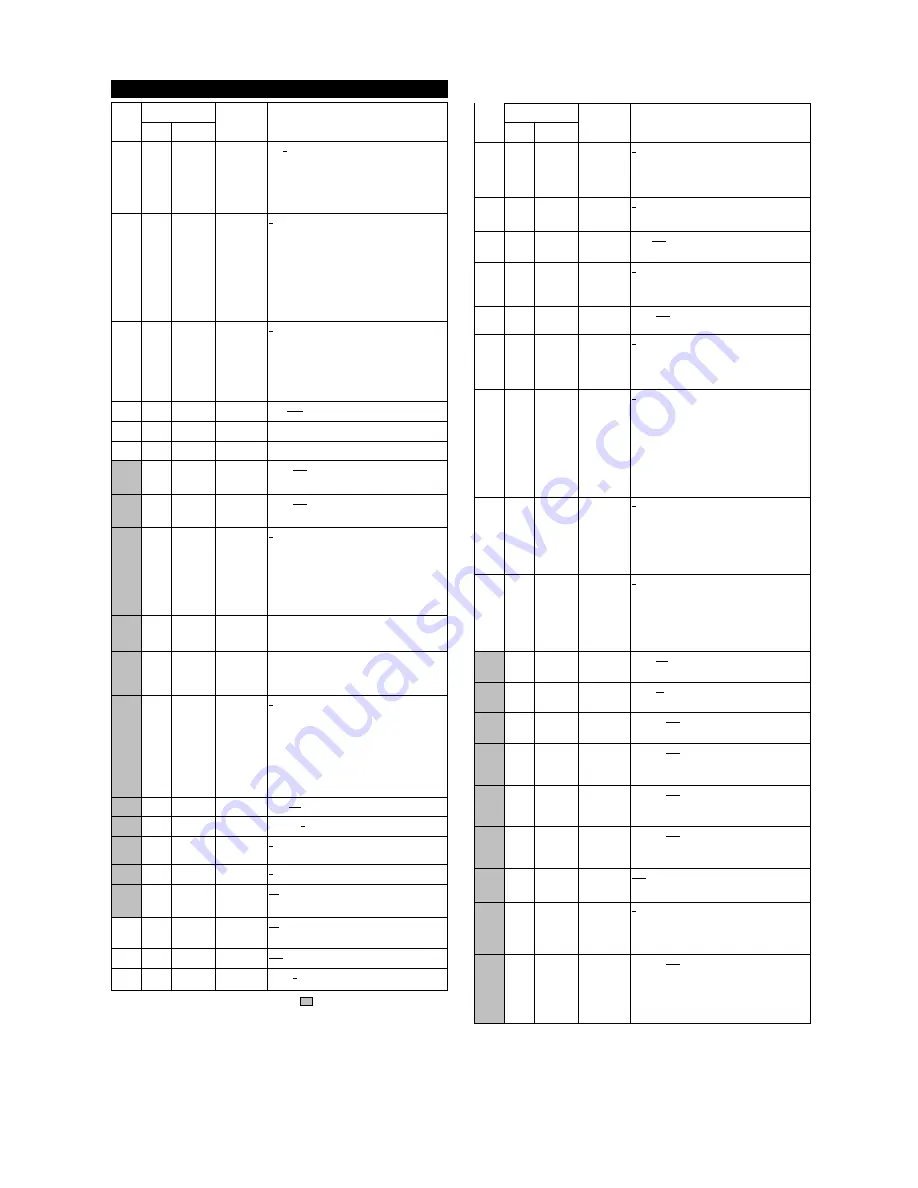
5-2
F: Fundamental Functions
Communication
address
Fcode
485
number
Link number
Function name
Setting range
f00
0h
80( 50 h) Data
protection
0 to 1
0 : Data change enable
1 : Data protection
This is a function to protect writing from the Keypad
panel.
The protection of writing from the link (T-Link, RS485,
etc.) is defined with H29 "Link function protection".
f01
1h
( h) Speed setting
N1
0 to 7
0 : KEYPAD operation (
∧
and
∨
key)
1 : Analog input (0 to ±10VDC)
2 : Analog input (0 to +10VDC)
3 : UP/DOWN control 1 (initial speed = 0 r/min)
4 : UP/DOWN control 2 (initial speed = last value)
5 : UP/DOWN control 3 (initial speed = Creep
speed 1 or 2)
6 : DIA card input
7 : DIB card input
f02
2h
( h) Operation
method
0 to 1
The method of operation is set.
0 : KEYPAD operation (FWD or REV or STOP key)
(LOCAL)
1 : FWD or REV signal input (REMOTE)
The change of REMOTE/LOCAL is possible also by
RST+STOP key to the keypad panel. This operation
corresponds to writing data of F02.
f03
3h
81( 51 h) M1 Maximum
speed
50 to 1500 to 24000 r/min
f04
4h
82( 52 h) M1-Rated
speed
50 to 24000 r/min
f05
5h
83( 53 h) M1-Rated
voltage
80 to 999 V
f07
7h
84( 54 h) Acceleration
time 1
0.01 to 5.00 to 99.99s
100.0 to 999.9s
1000 to 3600s
f08
8h
85( 55 h) Deceleration
time 1
0.01 to 5.00 to 99.99s
100.0 to 999.9s
1000 to 3600s
f10
Ah
86( 56 h) M1 Electronic
thermal
overload relay
(Select)
0 to 2
The motor overheating protection operates by using
NTC thermistor with the motor only for VG. In this
case, please make setting F10 Electronic thermal
"Inactive".
0 : Inactive (When you use the motor only for VG)
1 : Active (for 4-pole standard motor, with self-cooling
fan)
2 : Active (for Inverter motor, with separate cooling fan)
f11
Bh
87( 57 h) M1 Electronic
thermal
overload relay
(Level)
0.01 to 99.99A
100.0 to 999.9A
1000 to 2000A
f12
Ch
88( 58 h) M1 Electronic
thermal
overload relay
(Thermal time
constant)
0.5 to 75.0 min
f14
Eh
( h) Restart mode
after
momentary
power failure
0 to 5
0 : Inactive (Trip and alarm when power failure occurs.)
1 : Inactive (Trip, and alarm when power recovers.)
2 : Inactive (Deceleration to stop, and trip and alarm.)
3 : Active (Smooth recovery by continuous operation
mode)
4 : Active (Momentarily stops and restarts at speed on
power failure)
5 : Active (Momentarily stops and restarts at starting
speed)
f17
11h
( h) Gain (terminal
12 input)
0.0 to 100 to 200.0 %
f18
12h
( h) Bias (terminal
12 input)
-24000 to 0 to 24000 r/min
f20
14h
89( 59 h) DC brake
(Starting
speed)
0 to 3600 r/min
f21
15h
90( 5A h) DC brake
(Braking level)
0 to 100 %
f22
16h
91( 5B h) DC brake
(Braking time)
0.0 to 30.0 s
0.0 : (Inactive)
0.1 to 30.0 s
f23
17h
92( 5C h) Starting speed
(Speed)
0.0 to 150.0 r/min
(The frequency is limited so as not to become 0.1Hz or
less. (When using sensoless or V/F control))
f24
18h
93( 5D h) Starting speed
(Holding time)
0.00 to 10.00 s
f26
1Ah
94( 5E h) Motor sound
(Carrier Freq.)
0.75 to 7 to 15 kHz
A factory setting value of 75kW or more is 10kHz.
Communication
address
Fcode
485
number
Link number
Function name
Setting range
f27
1Bh
95( 5F h) Motor sound
(Sound tone)
0 to 3
0 : level 0
1 : level 1
2 : level 2
3 : level 3
f36
24h
( h) 30RY
operation
mode
0 to 1
0 : The relay(30) exites on trip mode.
1 : The relay(30) exites on normal mode.
f37
25h
96( 60 h) Stop speed
(Level)
0.0 to 10.0 to 150.0 r/min
(The frequency is limited so as not to become 0.1Hz or
less. (When using sensoless or V/F control))
f38
26h
97( 61 h) Stop speed
(Detection
method)
0 to 1
0 : Reference value
1 : Detected value
It is fixed 0 to use the V/F control.
f39
27h
98( 62 h) Stop speed
(Zerospeed
holding time)
0.00 to 0.50 to 10.00 s
f40
28h
99( 63 h) Torque limiting
mode 1
0 to 3
0 : Torque limiting invalid
1 : Torque limiting
2 : Power limiting
3 : Torque current limiting
f41
29h 100( 64 h) Torque limiting
mode 2
0 to 3
0 : Same limiting level (level 1) for 4 quadrants
1 : Drive torque limiting (level 1),
and Brake torque limiting (level 2)
2 : Upper torque limiting (level 1),
and Lower torque limiting (level 2)
3 : Same limiting level for 4 quadrants
(level 1 and level 2 changeover)
Level 1 and 2 is the data setting of the definition by F42,
43 ahead.
f42
2Ah 101( 65 h) Torque limiter
value
(level 1)
selection
0 to 5
0 : Internal preset value by F44
1 : Ai terminal input value [TL-REF1]
2 : DIA card input
3 : DIB card input
4 : Link enabled
5 : PID output
f43
2Bh 102( 66 h) Torque limiter
value
(level 2)
selection
0 to 5
0 : Internal preset value by F45
1 : Ai terminal input value [TL-REF2]
2 : DIA card input
3 : DIB card input
4 : Link enabled
5 : PID output
f44
2Ch 103( 67 h) Torque limiter
value
(level 1)
-300 to 150 to 300 %
f45
2Dh 104( 68 h) Torque limiter
value
(level 2)
-300 to 10 to 300 %
f46
2Eh 105( 69 h) Mechanical
loss
compensation
-300.00 to 0.00 to 300.00 %
This is used when mechanical loss of the load makes
amends.
f47
2Fh 106( 6A h) Torque bias
set 1
-300.00 to 0.00 to 300.00 %
This set value can be added to the torque reference
value.
TB1, 2 and 3 are switched by DI and are used.
f48
30h
( h) Torque bias
set 2
-300.00 to 0.00 to 300.00 %
This set value can be added to the torque reference
value.
TB1, 2 and 3 are switched by DI and are used.
f49
31h
( h) Torque bias
set 3
-300.00 to 0.00 to 300.00 %
This set value can be added to the torque reference
value.
TB1, 2 and 3 are switched by DI and are used.
f50
32h
( h) Torque bias
activation timer
0.00 to 1.00 s
( 300% / 1.00s )
Time up to 300% is set.
f51
33h 251( FB h) Torque
reference
monitor
(polarity)
0 to 1
Polarity selection of the data output related to torque
(AO, Keypad panel,code M)
0 : Display with torque polarity
1 : (+) for driving mode, and (-) for braking mode
f52
34h
( h) LED monitor
coefficient
(Display
coefficient A)
-999.00 to 1.00 to 999.00
The conversion coefficient to decide load axis rotation
speed and the display value at the line speed displayed
in LED are set.
Display value = Motor speed × (0.01 to 200.00)
The set data is effective only by 0.01 to 200.00 and
outside the range is invalid.
Underline indicates a factory setting.
Items without underline have different factory settings according to capacity.
You can change the setting of a function indicated by during operation.
You should stop operation to change the setting of other functions.
Содержание 5000VG7S Series
Страница 7: ...0 6 Warning Label Position for Inside the Inverter...
Страница 23: ...2 5 Basic Wiring Diagram Figure 2 3 1 Basic Wiring Diagram...
Страница 36: ...2 18 l Control circuit terminals Control circuit terminals Screw size M3...
Страница 94: ...9 4 FS5941 40 47 Figure 9 1 FS5941 60 52 FS5941 86 52 Figure 9 2...
Страница 96: ...9 6 RF3280 F11 RF3400 F11 Figure 9 5 RF3880 F11 Figure 9 6 6 6 Figure 9 7 F200160...