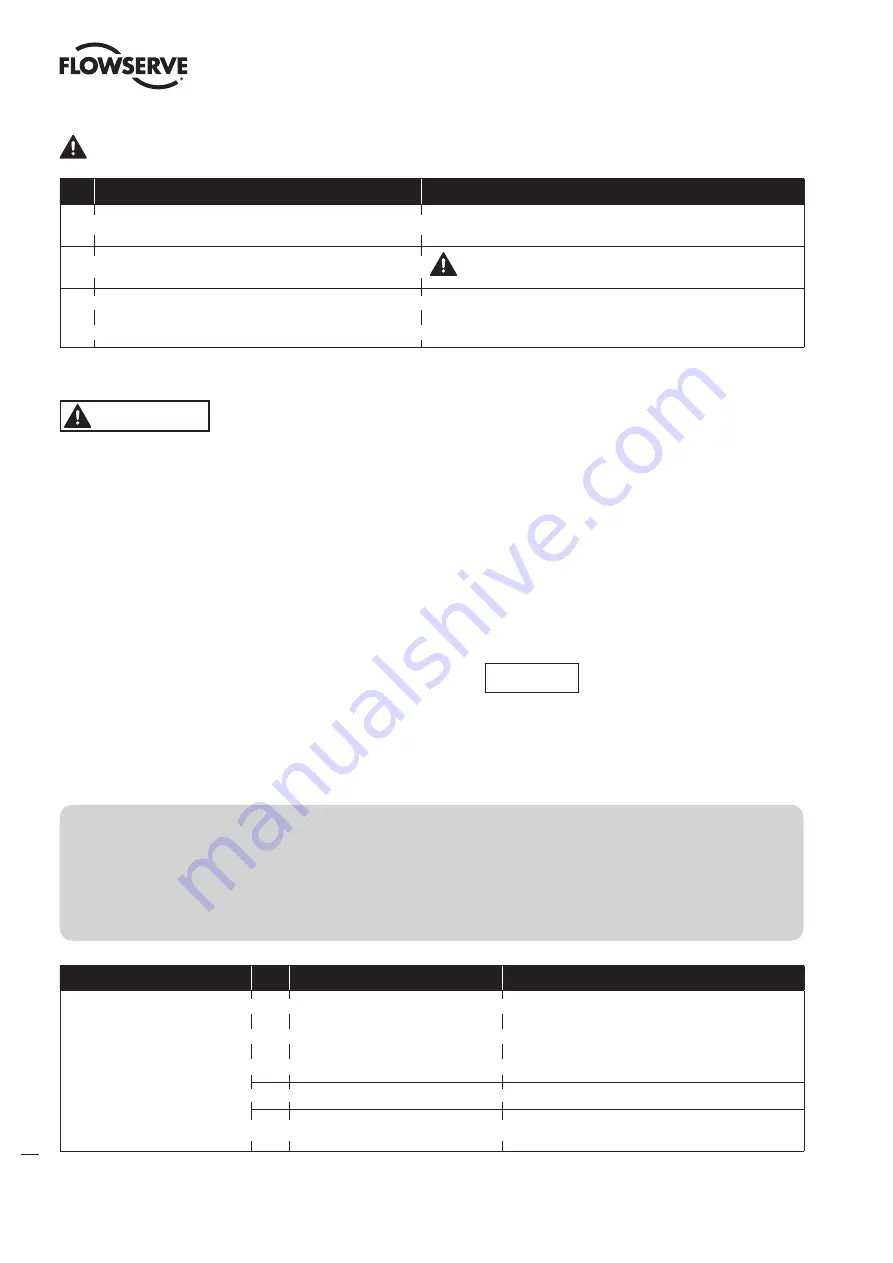
FlowAct Diaphragm Linear Actuator FCD VLENIMFACTA4 10/16
12
Prior to valve maintenance it is required that you check the following conditions to reduce the risk of malfunction and safety
related incidents.
No.
Check
Possible malfunction or safety related incident
1
Check for signs of leakage through the case bolting
and end flanges.
Tighten the case bolting nuts. See Section 14: Disassembly and
Reassembly for instructions. Also see Section 15.
2
Check if all nuts and bolts are securely fastened.
Avoid critical operating conditions if excess noise or
vibration levels occur during operation.
3
Check valve for smooth, full-stroke operation. Un-
steady stem movement could indicate an internal
valve problem.
Internal valve failure requires an immediate overhaul or actua-
tor replacement by qualified stuff.
Table 7: Basic safety massages for maintenance the valve
WARNING
Crushing hazard ! Failure to keep
hands, hair, and clothing away
from all moving parts when operating the control valve can
cause serious injury.
1. Clear all dirt and / or foreign material from the shaft
and control valve.
2. If leakage is detected, retighten the bolting.
3. Activities on the valve, see separate document.
4. Make sure all nuts and bolts are securely fastened.
5. If possible, stroke the valve and check for smooth,
full-stroke operation. Unsteady stem movement could
indicate an internal valve problem.
6. Make sure all accessory brackets and bolting are
securely fastened.
7. Check control valve health parameters:
• Characteristic curves of the valve with flow
• Upstream pressure
• Downstream pressure
into the control room.
NOTICE
Monitor trim and bonnet compo-
nents. If nominal and actual values
differ by more than 5%, maintenance may be required.
13 Troubleshooting
Contact customer service department or contract partner for any fault or defect found, otherwise
the manufacturer‘s guarantee shall be rendered null and void and the manufacturer released from
any responsibility. If the user performs the repairs, these User Instructions must be adhered to and
carried out in a competent manner. Original Equipment Manufacturer spare parts must be used to
make the repair.
Defect
No.
Possible Causes
Remedy
Stem does not move
1.1
• No energy supply (pneumatic air)
to actuator and accessories (posi-
tioner, air filter regulator, solenoid
valve, limit switch, and/ or special
accessories)
• Pneumatic actuators:
Check supply for leaks
Check air pressure (usually 6 bar; 88 psig)
1.2
• Mounted accessories do not work
• See User Instructions for accessory manufacturer
1.3
• Pneumatic actuator is defective
• Contact customer service department or contract
partner