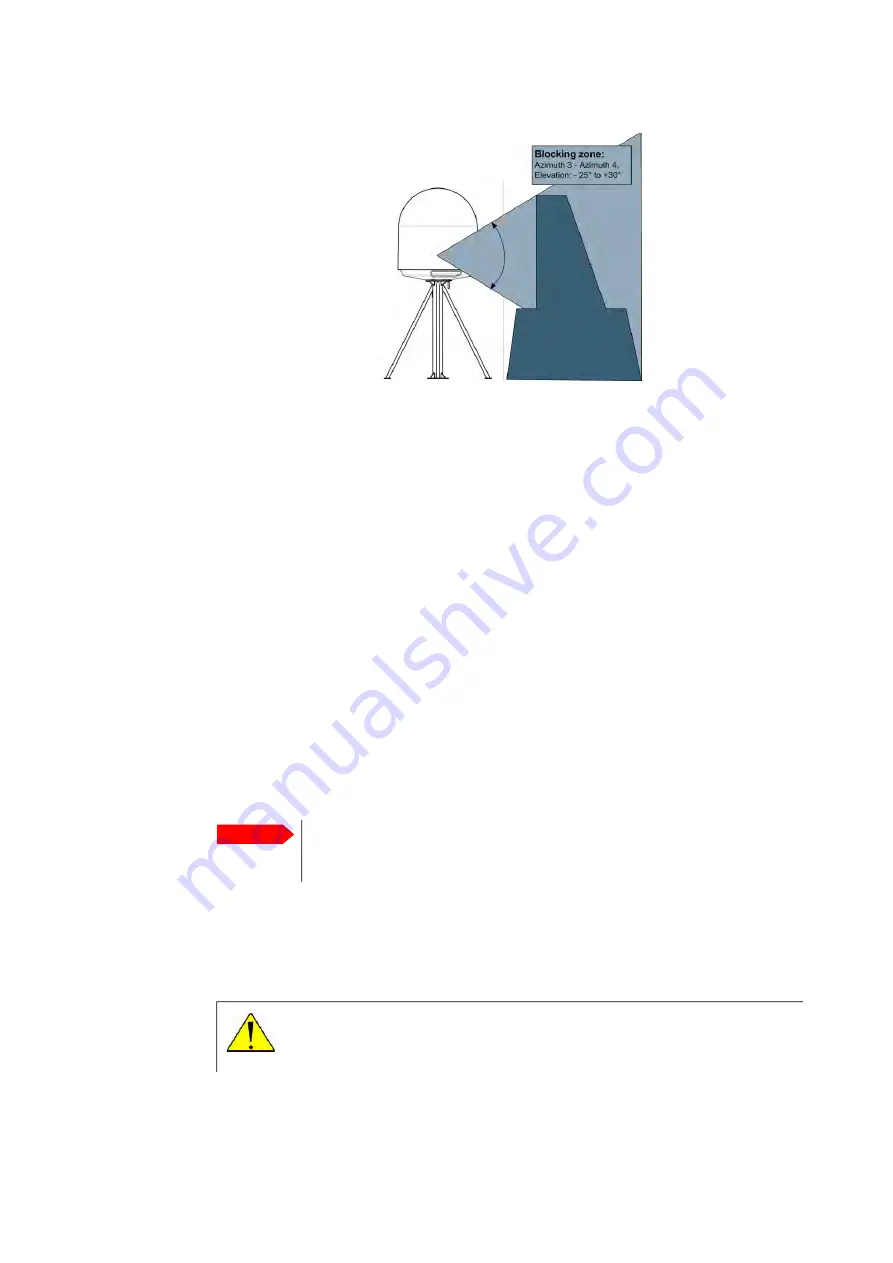
Site considerations
98-175666-C
Chapter 2: Installation
2-6
2.2.3 ADU mast flange and mast length
The system is designed for harsh environmental conditions at sea, both in regards to
vibration amplitude and speed. The antenna system performs optimally when
mounted on a properly designed foundation. When mounting the antenna the overall
goal is to establish a foundation which is as rigid as possible. However, in some
scenarios establishing a very rigid foundation can be difficult. This section aims at
defining the minimum design criterion for the mast. In addition, some specific design
suggestions are presented. Note that the design values given below depend on rigid
interfaces between antenna and ship, the values are furthermore given based on a
standard steel type (e.g. S235JR, S355JO).
The placement of the ADU must ensure a rigid structural connection to the hull or
structure of the ship. Parts of the ship with heavy resonant vibrations are not suitable
places for the ADU. A small platform or short mast must provide rigid support for the
ADU fastening bolts and a rigid interface to the ship. If it is necessary to use a tall mast,
you must stabilize the mast with bracing. In regards to stiffness the overall criterion is
that the first structural mode of the mast or foundation (where the antenna system is
mounted) should be above 30 Hz. All the designs presented in the following sections
respect this standard.
The ADU mast must carry the weight of the ADU unit, that is approximately105 kg (+
the weight of the mast flange) for the SAILOR 1000 XTR GX-R2 antenna and 37 kg (+ the
weight of the mast flange) for the SAILOR 600 XTR GX-R2 antenna. The mast must also
withstand on-board vibrations and wind speeds up to 110 knots on the radome, even
in icing conditions.
Figure 2-4: Blocking zone with no-transmit zones, elevation angle (example)
Important
An antenna mounted on a less stiff structure might be functional, but
could lead to a decrease in the operational lifetime of the antenna
system and possibly a decreased performance under operation
CAUTION!
Avoid sharp edges where the flange is in direct contact with
the radome. Round all edges as much as possible to avoid
damaging the surface of the radome.