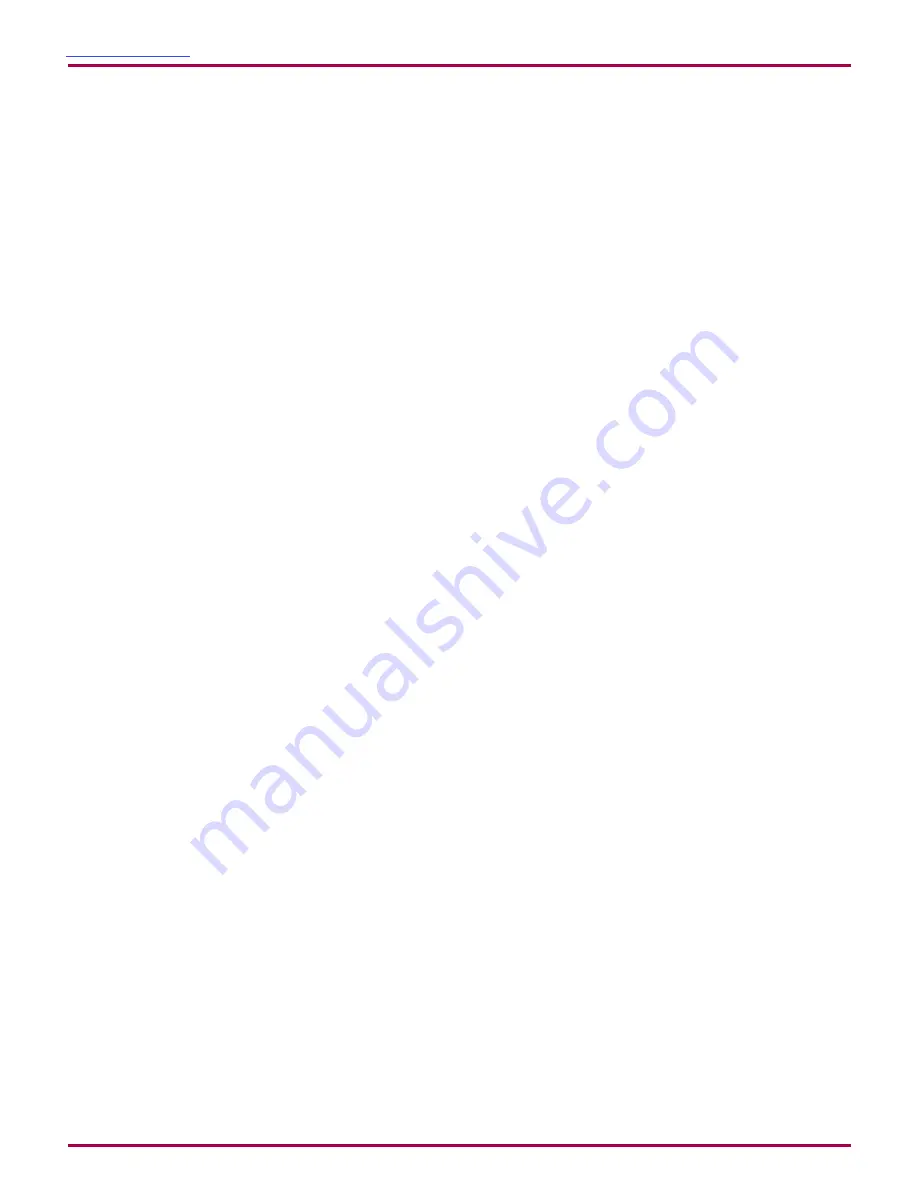
Deadband
This represents a flow range above and below the set point
value in which the PID control is suspended. This keeps
the control output from continually changing and produces
stability when close to the requested value.
Proportional Action (Kp)
Proportional action simply means that the controller output
changes in proportion to the error between the set point
and the actual flow. It is also commonly referred to as
gain, proportional gain and proportional band to name a
few. If the proportional gain is set too high, the system will
oscillate. If set too low, the fluid flow will "wonder" due to
a lack of responsiveness.
Integral Action (Ki)
The Integral element of the PID controller forces the actual
output (flow) to match the desired by utilizing the sum of
the error in flow rate.
Integral action is proportional to the sum of the error. This
term is needed to remove long term, or steady-state error
that cannot be removed by the proportional term.
Integral action is the most important factor governing control
near the set point. The integral term changes the control
output as a result of a continuing error between set point
and actual. The integral term will continue to shift the output
until the actual flow rate falls within the Deadband value.
Integral action will also effect transition response times.
The greater the change in requested flow rate, the more
the integral action will effect the response time.
The integral gain, Ki, must be chosen such that oscillations
do not occur. Increased integral gain will cause faster
response times, but can lead to process instability and
uncontrolled oscillations.
Derivative Action (Kd)
Derivative action is proportional to the rate of change of
the error. The derivative term dampens, or slows down
process overshoot and improves the response to changes
in the process being controlled. Another way to view this
term is that it “anticipates” or leads what is happening with
the actual flow.
Derivative action provides a sudden shift in the control output
as a result of a quick change in the actual flow (transient)
or set point. If the actual flow drops quickly, the derivative
term will provide a large change in the output in an attempt
to correct the perturbation before it goes too far.
Derivative action should be associated more with transient
response control and less with overshoot inhibition such
as during start-up, or trigger ON.
Oscillation due to derivative action is typically a cyclic
“wander” away from the set point.
Putting It All Together
The optimum PID controller settings are determined based
on the application. Types of applications that will effect PID
considerations are:
• Dynamic control of flow rate while spraying parts -
robot mounted
• Short GUN trigger times
• Long trigger times - constant flow rate requested
during entire part
• Precise 2K mixing ratio required at all times
• Low flow rate applications
• Applicators mounted on oscillators or reciprocators
that may produce cyclic back pressures within the
fluid lines
• Systems with piston pump type supplies
• Long pilot line lengths from fluid regulator to
transducer
General Guidelines
1. The type of fluid regulator represents the larg-est overall
impact on system response. The following table lists
control settings for various fluid regulators that should
result in stable control. The determination of these
parameters was based upon worst case conditions and
therefore constitutes “conservative” control response.
It isRecommended to start with these values and
confirm stable response before trying to achieve faster
response from the system. Generally, when adjusting
the Proportional (Kp) and Integral (Ki) gain parameters,
adjust both up or down proportional to themselves. In
other words, if faster response is desired and the system
is currently operating stable, assume the starting Kp
value is 500 and the starting Ki value is 2000. You would
adjust the Kp value to 550 (10% increase) and the Ki
value to 2200 (also a 10% increase). The deadband
parameter should be kept to 1 and the differential gain
(Kd) at 0.
LN-9400-00-R11 (08/2018)
54 / 96
www.carlisleft.com
PARTS IDENTIFICATION
Содержание Ransburg DynaFlow 77376
Страница 13: ...Figure 1 Block Diagram Return To Contents LN 9400 00 R11 08 2018 13 96 www carlisleft com INTRODUCTION...
Страница 90: ...Fluid Panel Sheet 1 Return To Contents LN 9400 00 R11 08 2018 90 96 www carlisleft com APPENDIX...
Страница 91: ...Fluid Panel Sheet 2 Return To Contents LN 9400 00 R11 08 2018 91 96 www carlisleft com APPENDIX...
Страница 92: ...Fluid Panel Sheet 3 Return To Contents LN 9400 00 R11 08 2018 92 96 www carlisleft com APPENDIX...