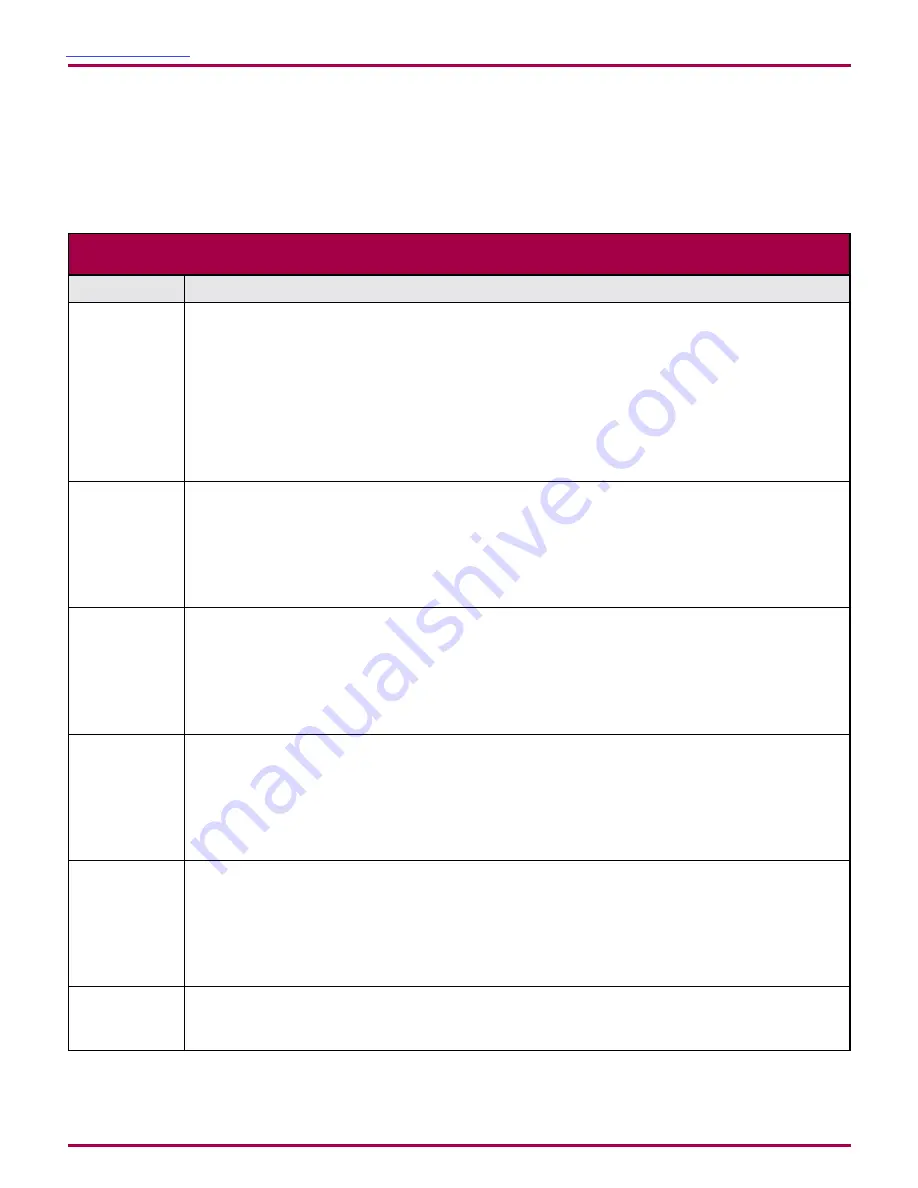
Discrete GUN I/O provides the input control and output status signals required to interface each GUN with a PLC or
similar controller, or other system control components. All GUN I/O can also be controlled or monitored through an ex-
ternal host controller operating through a serial data communications link or the state of each forced active through the
local OPERATOR INTERFACE/host controller.
Gun I/O
Description
GUN INPUTS
Input Signals
Trigger
Halt/Reset
Clean
Run
Gun Mask
Total Reset
For automatic applicators: Starts fluid flow when supplied a 24 VDC signal assuming that the GUN
has been put in run mode, is configured properly, and all other conditions are satisfied.
For manual GUNs: A Trigger signal is required for the LOAD mode. The Trigger signal can be
generated from an atomizing air flow switch. If a Trigger signal is received from the flow switch but
no fluid flow is recorded from the catalyst (slaved) CHANNEL, then a FLOW TOO LOW fault is
generated. This ensures that both material components are present to the GUN. If the dip switch,
Pos #1 on the Channel Card is on, then this input is not used. Fluid flow through the master channel
is used to indicate a TRIGGER ON condition.
Halt requires a pulsed signal of at least 0.25 seconds duration. It is used to stop the JOB # cur-
rently being executed or to stop a CLEAN/PURGE operation. GUN faults are also reset. While
in HALT mode, any new JOB # selection using the JOB # Strobe will be entered into the Queue.
The GUN will run the JOB # located in the Queue when a RUN signal is again supplied. The faults
can still be viewed in the ERROR LOG data table. Halt has no effect on the JOB # in the Queue
(Next JOB # to be run).
Clean requires a pulsed signal of at least 0.25 seconds duration. It forces the material regulators
controlled by the GUN parameters to the full open position. This permits the fluid system to be
cleaned. The removal of the GUN Enable signal or a HALT input signal is required to end the
CLEAN operation. Actual cleaning sequencing (PURGE) such as soft air push-out is performed
by the PLC, or other external controller. For details, refer to "Clean Mode" in the "Operation"
section of this manual.
This input will activate the GUN and will allow material flow if all other requirements are met. This
is identical to pushing the GUN ON switch on the OPERATOR INTERFACE PANELS. Run requires
a pulsed signal of at least 0.25 seconds duration. If this signal is reapplied once the JOB # has
been started, then it is ignored. When this signal is supplied following a HALT, the JOB # stored
in the queue will be activated. If no new JOB # was entered during the previous HALT, then the
JOB # located in the queue will not change and will be used again.
The Gun Mask input specifies whether a JOB # or toggled into GUN #n queue. This signal is
used in conjunction with the system PROGRAM SELECT and PROGRAM STROBE inputs.
A 24 VDC signal selects the GUN, a 0 VDC signal masks the GUN as ‘not used for the JOB #
selected’. Multiple gun masks can be asserted simultaneously if it is desired to load more than
one gun with the same JOB #.
Total Reset requires a pulsed signal of at least 0.25 seconds duration. This signal will reset the
daily and JOB totals for the GUN. The non-resettable total will not be effected.
(Continued On Next Page)
LN-9400-00-R11 (08/2018)
24 / 96
www.carlisleft.com
INSTALLATION
Содержание Ransburg DynaFlow 77376
Страница 13: ...Figure 1 Block Diagram Return To Contents LN 9400 00 R11 08 2018 13 96 www carlisleft com INTRODUCTION...
Страница 90: ...Fluid Panel Sheet 1 Return To Contents LN 9400 00 R11 08 2018 90 96 www carlisleft com APPENDIX...
Страница 91: ...Fluid Panel Sheet 2 Return To Contents LN 9400 00 R11 08 2018 91 96 www carlisleft com APPENDIX...
Страница 92: ...Fluid Panel Sheet 3 Return To Contents LN 9400 00 R11 08 2018 92 96 www carlisleft com APPENDIX...