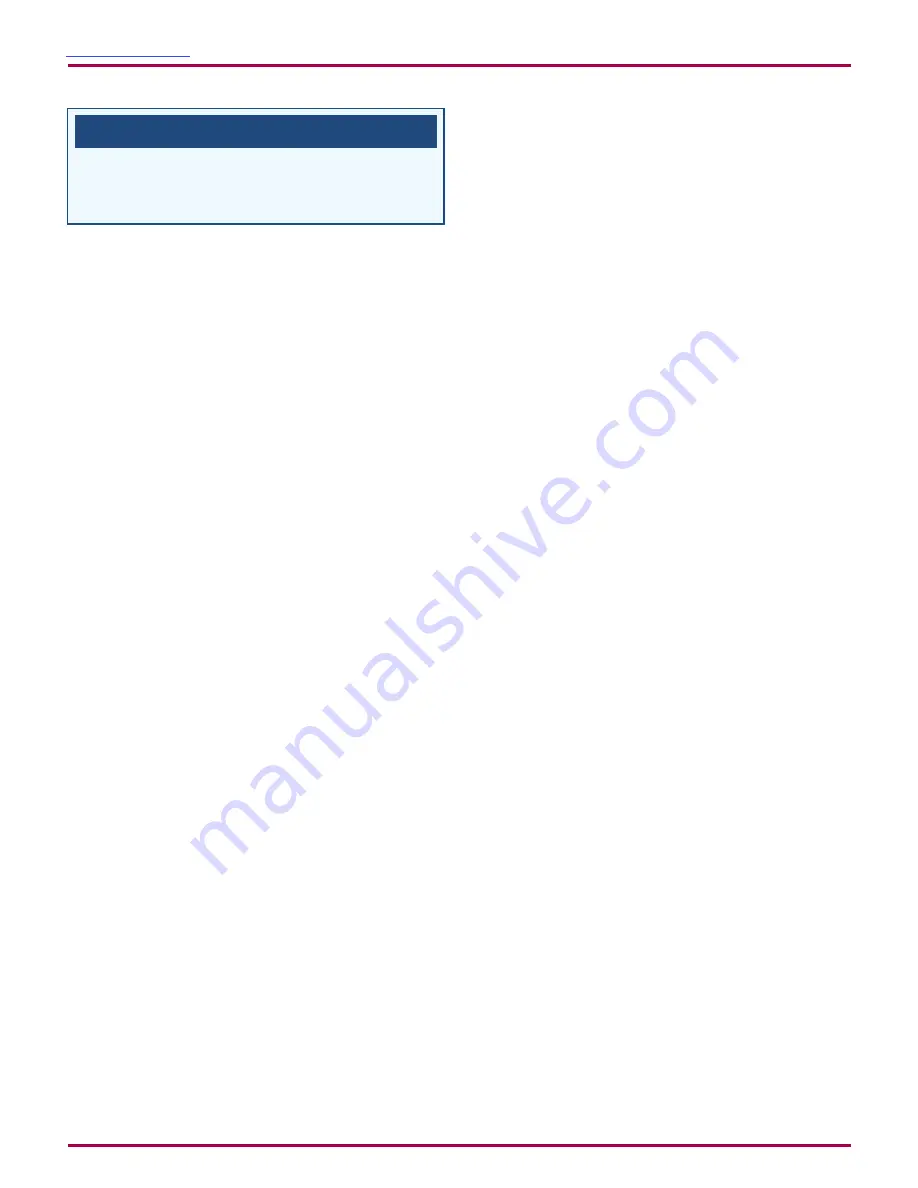
Maximum Flow Rate
This parameter has 2 possible meanings, dependent upon
how the GUN is configured.
- Manual Gun
This parameter is an alarm set point. If the total flow rate of
the mixed material to the spray GUN exceeds the amount
specified by this parameter, the GUN will shut OFF as the
result of a FLOW OUT OF RANGE FAULT.
- Automatic Gun
This parameter is used to scale the flow rate output for
the GUN's CHANNEL(s) to specify the desired flow rate
when a 10 VDC (or 20 ma) signal is applied to the analog
set point input.
Minimum Flow Rate
This parameter has 2 possible meanings, dependent upon
how the GUN is configured.
- Manual GUN
This parameter is an alarm set point. If the total flow rate
of the mixed material to the spray GUN falls below the
amount specified by this parameter, the GUN will shut
OFF as the result of a FLOW OUT OF RANGE FAULT. If
no alarm is desired, set this parameter to zero (0) and the
feature will be disabled.
- Automatic GUN
This parameter is used to scale the flow rate output for
the GUN's CHANNEL(s) to specify the desired flow rate
when a 0 VDC (or 4.0ma) signal is applied to the analog
set point input.
Pot-Life Time
The time, in seconds, required for the mixed material being
used to set up or harden. This information is obtainable
from the manufacturer of the material. The controller will
determine if any mixed material is in the paint lines for longer
than the Pot-Life Time setting. It is recommended that this
time be somewhat less than the actual set up time to allow
time to clean the system in the event that the Pot-Life timer
expires. If the specified time expires, a Pot-Life alarm is
issued, warning the operator that this problem exists. The
NOTE
When operating in 2K mode, this parameter
relates to the total mixed material delivered through
the GUN.
Pot-Life alarm
does not
shut off the GUN, as this would
prevent the operator from triggering and expelling the mixed
fluid. The Pot-Life alarm status will remain until the expired
material has been purged.
Pot-Life checking may be disabled by entering a value of
zero seconds. Since previous versions of the DynaFlow
firmware and software used the value 999 minutes to
disable Pot-Life checking, the value of 999 seconds is not
permitted and will automatically be changed to zero sec-
onds. When upgrading DynaFlow firmware and software,
JOBs that specified any value other than 999 minutes must
be manually converted to seconds after the upgrade is
performed. A Pot-Life alarm may be cleared by entering
a Pot-Life Time of zero seconds.
MVR High Pressure (Master and Slave)
This parameter allows the operator to limit the maximum
pressure that the transducer is allowed to output to the fluid
regulator in any mode.
MVR Low Pressure (Master and Slave)
This parameter allows the operator to set the low limit on
the pressure sent to the fluid regulator while in the Run or
Load modes. It can be used to cause a faster response
by the transducer/regulator system. It should be adjusted
so that the regulator valve is just short of opening. With a
standard MVR valve, this value should never exceed 30
psi. If this value is too high, continuous FLOW TOO HIGH
faults will occur.
When a GUN is configured for two-component operation
and the Ratio is 99.0:1, or greater, the GUN is said to be
operating in pseudo single-component mode. In this case,
the slave (catalyst) CHANNEL is NOT set to MVR LOW
when the GUN is placed in either Run or Load modes.
However, if the slave (catalyst) CHANNEL is specified as
a clean CHANNEL, it will be turned on to MVR HIGH in
Clean mode.
MVR High and MVR Low Effect On PID Operation
The PID will only output transducer pressures between
MVR LOW and MVR HIGH.
Pulses/Liter (Master and Slave)
The number of pulses sent from the flow meter to the con-
troller for each unit of fluid flow. Each pulse represents a
volume of fluid and is dependent on flow meter size. This
value can be verified or adjusted during a calibration process
to achieve the best accuracy (See "Calibration Mode" in the
"Operation" section of this manual). The calibration of all
LN-9400-00-R11 (08/2018)
35 / 96
www.carlisleft.com
OPERATION
Содержание Ransburg DynaFlow 77376
Страница 13: ...Figure 1 Block Diagram Return To Contents LN 9400 00 R11 08 2018 13 96 www carlisleft com INTRODUCTION...
Страница 90: ...Fluid Panel Sheet 1 Return To Contents LN 9400 00 R11 08 2018 90 96 www carlisleft com APPENDIX...
Страница 91: ...Fluid Panel Sheet 2 Return To Contents LN 9400 00 R11 08 2018 91 96 www carlisleft com APPENDIX...
Страница 92: ...Fluid Panel Sheet 3 Return To Contents LN 9400 00 R11 08 2018 92 96 www carlisleft com APPENDIX...