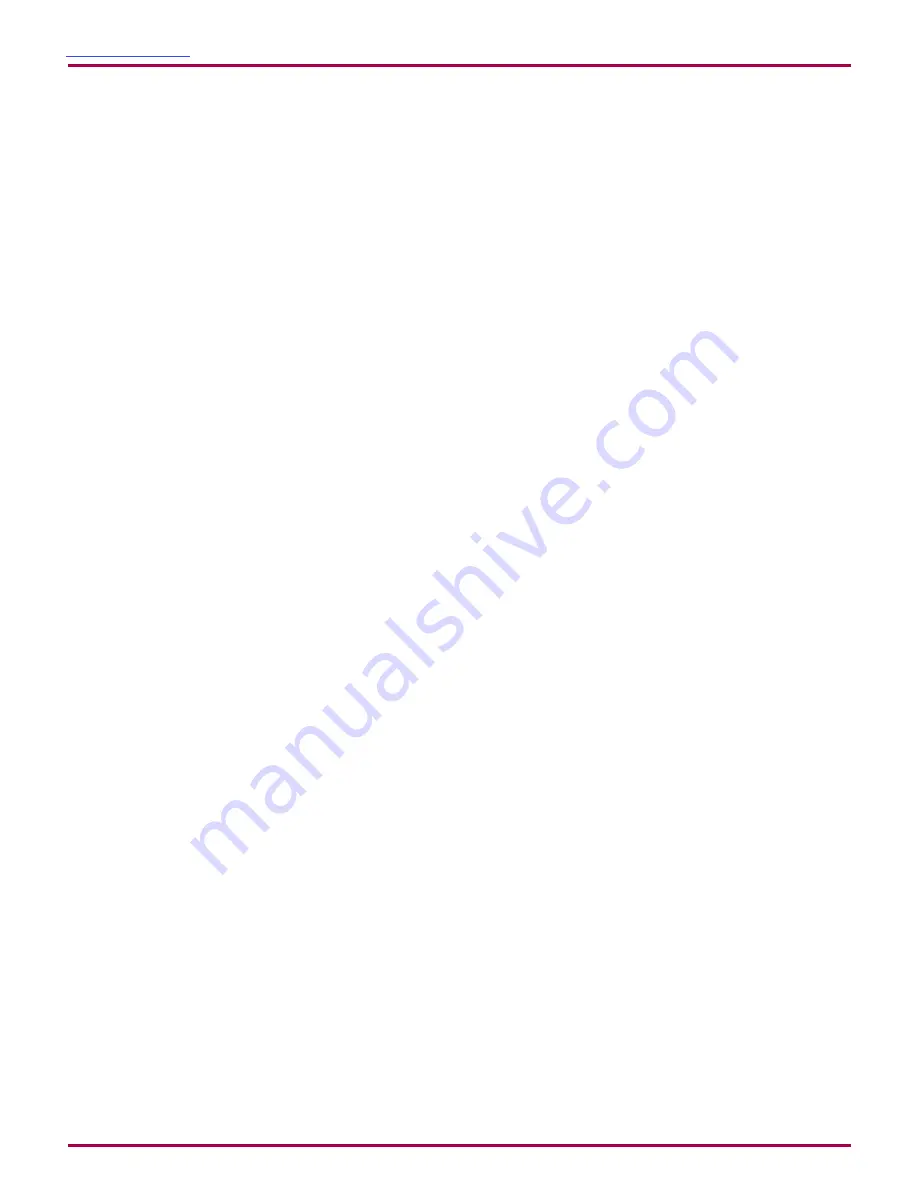
Configurable Operating Parameters
The design of the DynaFlow system allows it to be config-
ured to meet the specific requirements of each application.
The 8 available CHANNELs can be linked together, using
1 of 8 GUNs, to control the flow and mixing regulation of
two-component materials. The installed channels can be
configured to suit the application. If you are using single-com-
ponent coatings, the DynaFlow controller can support 8
separate single CHANNEL GUNs operating simultaneously.
If you are using two-component materials, then 4 separate
2-CHANNEL GUNs operating simultaneously can be sup-
ported. For example, you can use 4 CHANNELs assigned
to 2 GUNs to spray 2 dual component paints on automatic
machines, and 2 CHANNELs assigned to 1 GUN to spray
one dual component paint with a manual hand spray GUN.
In addition to the above, a GUN configured for two-compo-
nent operation can be dynamically changed to operate in
a single-component mode by simply setting the ratio JOB
parameter to 100. This allows a GUN to operate in either
dual or single-component modes by simply changing JOB
numbers.
The controlling parameters for each GUN and the CHAN-
NEL(S) assigned to that GUN, are called JOBs. The JOB
values define flow characteristics such as Target Flow
Rate, Mix Ratio, Flow Tolerance, etc. JOBs include all of
the parameters that may be dependent on the material
used. This offers the ability to optimize system control
as needed per material and then recall the settings each
time that material is requested. There are up to 100 JOB
#s for each GUN. By saving frequently used JOB #s to
memory you can later recall them by loading the number
representing that JOB #.
All of the JOB #s can be backed-up to, and restored from
a USB memory device. Reference the "Operator Interface
Users Manual" and "Program-mers Manual" for details on
data transfer operation and available formats.
The flow control unit includes one Interface Module and
up to 8 hardware PID control CHANNELs, 2 CHANNELs
located on each of the 4 possible Channel Modules. The
Interface Module will communicate to a host controller. The
host is one of the following:
• PLC using discrete I/O
• Allen-Bradley PLC using RIO
• Local Operator Interface using an RS-232C
communication port
3-K Operation
DynaFlow was designed for either single or two-compo-
nent operation. Three-component operation is possible
by configuring two, two-component, guns. The first Gun
is set up as follows:
Gun 1 =
Master Channel =
Material = Resin
Flow Controller = Color Change Value (CCV)
Flow Meter = Standard Gear-Type
Slave Channel =
Material = 2
nd
Component
Flow Controller = MVR, with appropriate size needle
Flow Meter = Piston or Gear, depending on min/max
flow rates (see Notes 4 and 5)
Operating Mode = Manual
The output of the first Gun is then fed into the Master
Channel input of the second Gun. The second Gun is
setup as follows:
Gun 2 =
Master Channel =
Material = Output of Gun 1 (Resin + 2
nd
Component)
Flow Controller = Color Change Value (CCV)
(see Notes 1, 2, and 3)
Flow Meter = Gear-Type
Slave Channel =
Material = 3
rd
Component
Flow Controller = MVR, with appropriate size needle
Flow Meter = Piston or Gear, depending on min/max
flow rates (see Notes 4 and 5)
Operating Mode = Manual or Auto
(see Notes 1, 2, and 3)
LN-9400-00-R11 (08/2018)
11 / 96
www.carlisleft.com
INTRODUCTION
Содержание Ransburg DynaFlow 77376
Страница 13: ...Figure 1 Block Diagram Return To Contents LN 9400 00 R11 08 2018 13 96 www carlisleft com INTRODUCTION...
Страница 90: ...Fluid Panel Sheet 1 Return To Contents LN 9400 00 R11 08 2018 90 96 www carlisleft com APPENDIX...
Страница 91: ...Fluid Panel Sheet 2 Return To Contents LN 9400 00 R11 08 2018 91 96 www carlisleft com APPENDIX...
Страница 92: ...Fluid Panel Sheet 3 Return To Contents LN 9400 00 R11 08 2018 92 96 www carlisleft com APPENDIX...