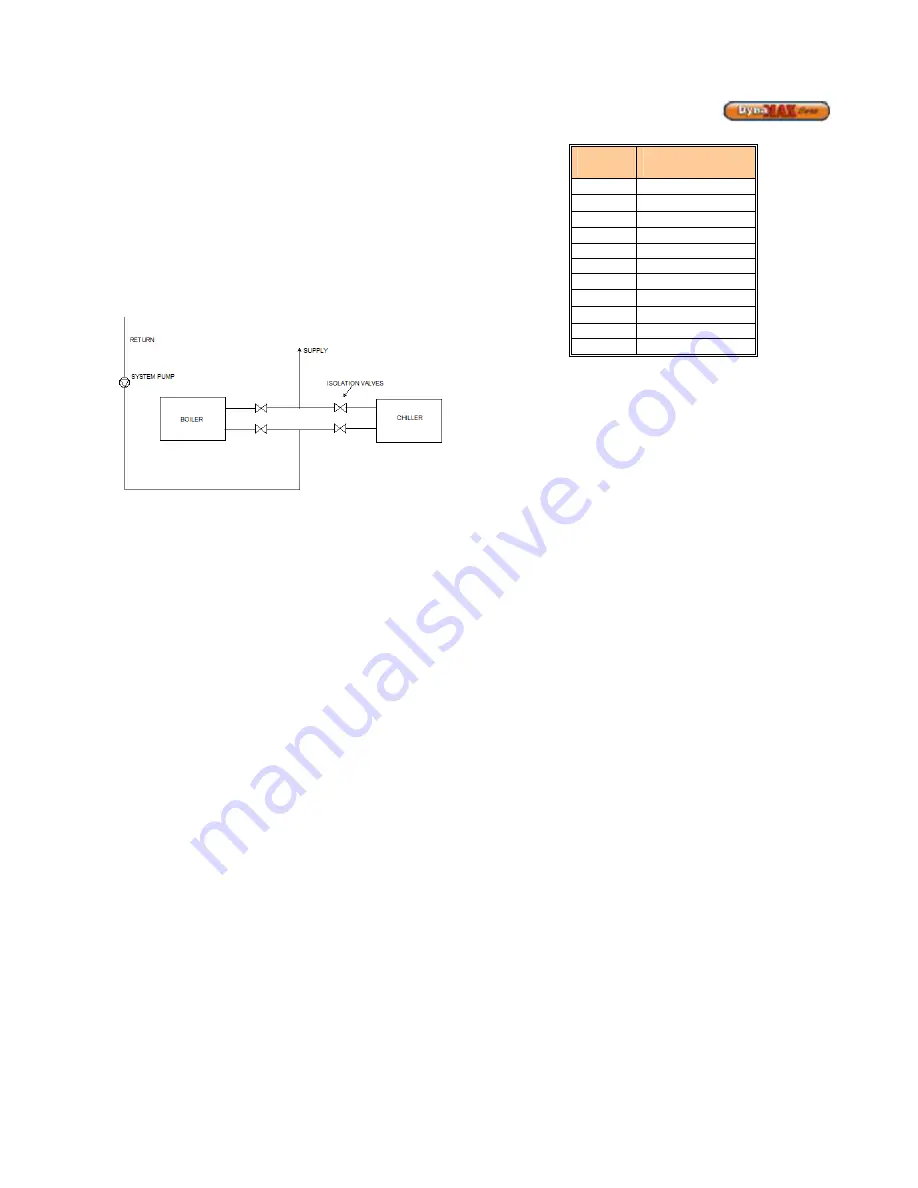
16
shelter will help to minimize nuisance problems with
electrical connections and will allow easier servicing of
the appliance under severe weather conditions.
4.2
WARNING REGARDING CHILLED WATER
SYSTEMS
When an appliance is connected to an air conditioning
system where the same water is used for heating and
cooling, the chiller must be piped in parallel with the
appliance. Appropriate isolation valves; manual or motorized
must be provided to prevent the chilled water from entering
the appliance.
Figure 19: Chilled Water System
4.3
INLET AND OUTLET CONNECTIONS
•
All water connections must meet
American National
Standard Pipe Threads (NPT).
•
For ease of service, install unions on inlet and outlet of
the appliance. The connection to the appliance marked
“Inlet” on the header should be used for return from the
system. The connection on the header marked “Outlet”
is to be connected to the supply side of the system.
4.4
MINIMUM PIPE SIZE REQUIREMENTS
Minimum water pipe connections are as follows for DynaMax
HS single unit installations. The equivalent number of
straight feet of pipe for each valve and fitting in the
connecting piping must be considered to properly arrive at
the total equivalent feet of straight pipe in the field installed
piping to the appliance. Consult factory if longer piping
distances are required for a specific application. It is
recommended to use copper piping for all system piping to
reduce the possibility of the formation of deposits, which may
result in heat exchanger starvation.
System pipe size must be in accordance with Table 10, and
between supply and return lines, must not exceed 50 feet of
equivalent length. Connection sizes at the heater are given
in Tables 3 & 5. Any reduction in recommended pipe size
may decrease flow resulting in high temperature rise across
the heat exchanger, boiler noise, flashing to steam and non-
warrantable heat exchanger damage.
Table 10: Minimal System Pipe Size
Input
[BTU/hr]
Water Size, NPT
[in.]
80,000
1
100,000
1
150,000
1
199,000
1 1/4
250,000
1 1/4
299,000
1 1/2
399,000
2
500,000
2
600,000
2
700,000
2
800,000
2
4.5
HEAT EXCHANGER
This appliance uses precision formed stainless steel tubing
to maximize the heat transfer process and to achieve 97%
steady-state efficiency. The DynaMax HS is designed to
withstand 160 PSIG working pressure.
A factory installed circulating pump ensures proper water
flow during burner operation and creates enough velocity
inside the stainless steel tubes and headers that prevents
scaling.
Installing a strainer upstream of the heat exchanger will
reduce the likelihood of tubes from being blocked by debris.
4.6
LOW WATER TEMPERATURE SYSTEMS
In applications where the heating system requires supply
water temperatures below 110°F, connections may be made
directly to the DynaMax HS. At incoming temperatures of
80
o
F or lower the DynaMax HS achieves maximum
efficiency. Inlet temperatures must not drop below 40
o
F to
prevent freezing.
4.7
PIPING ARRANGEMENTS
4.7.1
Field Supplied Components
1) Boiler system piping
Boiler system piping MUST be sized according to
Table 10. Reducing the pipe size can restrict the
flow rate through the boiler, causing boiler damage
and will void the manufacturer’s warranty.
2) Isolation Valves
Use only full port ball valves. Failure to supply full
port ball valves may result in reduced flow rate
through the boiler, causing boiler damage and will
void the manufacturer’s warranty.
3) Anti-Scald Mixing Valve
An anti-scaled mixing valve is recommended when
DHW storage is above 120
o
F.
4) Unions
Recommended for ease of serviceability.
5) System Temperature Sensor
A system temperature sensor is to be installed in
the main header at a point to detect controlled
temperature and where it will not lead to short-
cycling of the boiler.
An instantaneous water heater is designed to deliver hot
water without the use of a storage tank. It is suitable for
applications with variable load such as restaurants,
Содержание DynaMax DMH081
Страница 2: ......
Страница 12: ...7 Figure 5 DynaMax HS Wall Hung Service Clearances Figure 6 DynaMax HS Floor Mount Service Clearances...
Страница 68: ...65 PART 14 EXPLODED VIEW PARTS LIST DYNAMAX HS WALL HUNG...
Страница 69: ...66 DYNAMAX HS FLOOR MOUNT...
Страница 76: ...73 PART 15 ELECTRICAL DIAGRAMS 15 1 DM 80 299 INTERNAL WIRING DIAGRAM...
Страница 77: ...74 15 2 DM 399 800 INTERNAL WIRING DIAGRAM...
Страница 78: ...75...