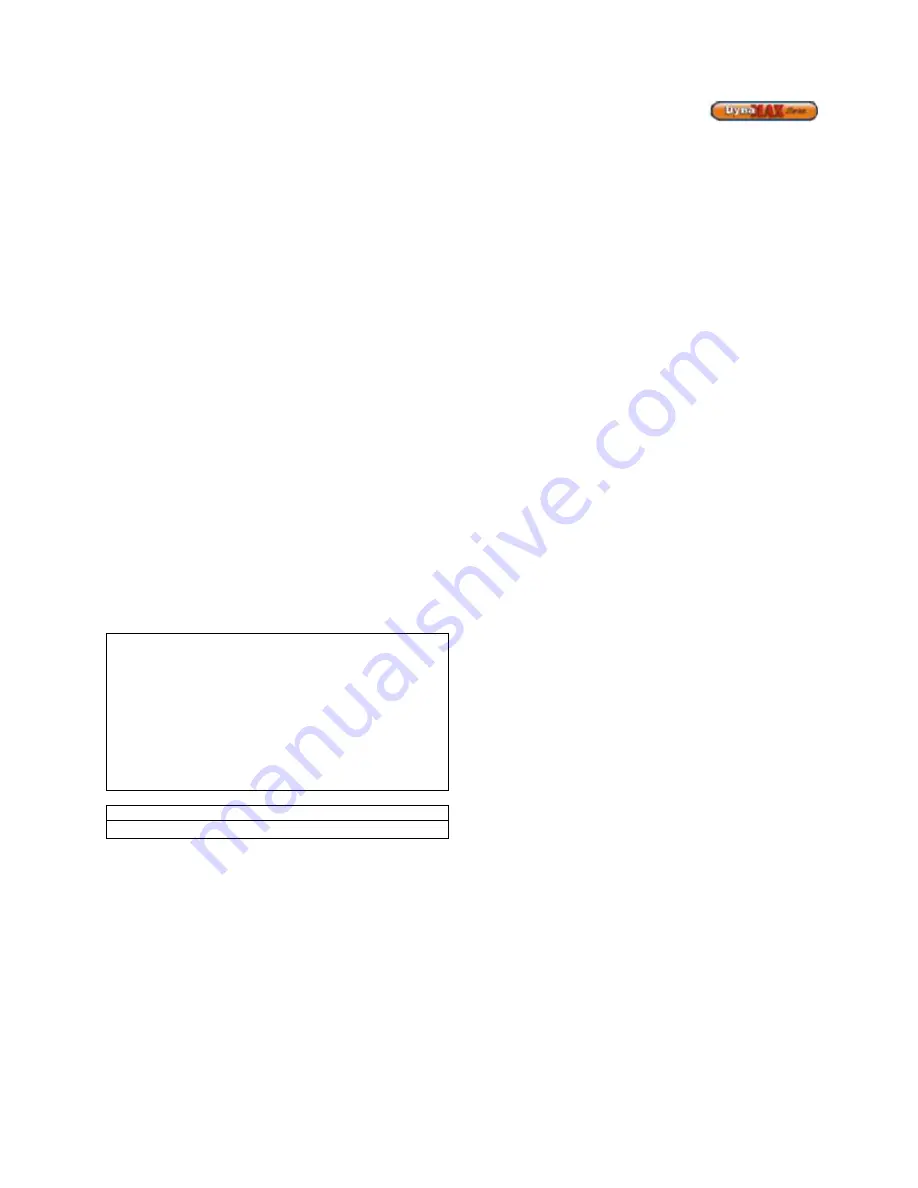
1
PART 1
GENERAL
INFORMATION
1.1
INTRODUCTION
The DynaMax HS boiler is a fan assisted boiler based on a
push through design which offers several venting options.
Heat output is controlled by a one to one air/gas ratio
control gas valve which provides seamless modulation. The
boiler provides central heating, domestic hot water or
combination heating with DHW priority at working pressure
up to 160 PSI. It is designed for use with a fully pumped
and pressurized water system. The boiler/water heater will
automatically modulate to provide heat outputs from 100%
down to approximately 20% of rated input.
The DynaMax HS utilizes a negative pressure gas valve.
The operation of the fan will generate a negative pressure
in the venturi, which draws in a matching amount of gas
through the valve.
During operation the DynaMax HS maintains steady state
efficiency across the entire range of modulation. Air and
gas are metered in precise proportion (1:1 Ratio) allowing
combustion characteristics which determine efficiency to
remain the same over the entire operating range.
The DynaMax HS is designed so that all of the sensible
heating value and most of the latent heat is being
transferred to the water.
1.2
SPECIAL INSTRUCTIONS TO OWNER
This manual supplies information for the installation,
operation and servicing of the appliance. It is strongly
recommended that this manual be reviewed completely
before proceeding with an installation
CAUTION
It is important that all gas appliances are installed by a
qualified installer/technician. It is in your own interest and
that of safety to ensure that all local codes, and all the
following “NOTES” and “WARNINGS” are complied with.
Installing, servicing or adjusting this appliance should be
performed only by a qualified installer/technician that is
trained by Camus Hydronics. The serviceman must utilize a
combustion analyzer with CO
2
, CO, and draft gauge, to set
the
appliance
according
to
Camus
Hydronics’
recommendations, prior to commissioning.
NOTE
RETAIN THIS MANUAL FOR FUTURE REFERENCE
1.3
CHECKING EQUIPMENT
Check for signs of shipping damage upon receiving
equipment. Pay particular attention to parts accompanying
the boiler, which may show signs of being hit or otherwise
being mishandled. Verify total number of pieces shown on
packing slip with those actually received. In case there is
damage or a shortage, immediately notify carrier.
1.4
DISPLAY UNIT
The display unit will indicate status and will display selected
temperature. Refer to Part 6 Control Panel, which provides
details to modes and error codes displayed on the
appliance.
1.5
SEQUENCE OF OPERATION
1) Power switch is placed in the “ON” position.
2) Minimum 120 VAC 60Hz single phase (15A circuit) is
supplied to the DynaMax HS field connection board.
3) 24Vac power is supplied to the DynaMax HS Controller
which provides all setup and ignition control functions.
4) After the appliance water pump starts, flow is proven
by the flow proving device or flow switch. The normally
open dry contacts in the low water cutoff (LWCO), if
supplied, is to be wired in series with the normally open
contacts of the flow proving device.
5) Locate the probe type LWCO in the piping at least
some distance above the boiler/ inlet connection. In all
cases check with local codes.
6) Depending on the selected mode, the appliance
operates as a master or slave configuration.
7) The DynaMax HS controller initiates a startup
sequence once it receives a heat demand.
8) The DynaMax HS controller energizes the on-board
pump and starts to ramp up the voltage to the
electrically commutated DC motor of the combustion
fan.
9) The fan will run at pre-purge speed until the pre-purge
timer is satisfied. Once this is complete the DynaMax
HS controller provides a signal to ignition fan speed.
10) The DynaMax HS controller goes through internal
safety checks and if this is satisfied the ignition
sequence begins.
11) The DynaMax HS controller supplies voltage to the
air/gas ratio control valve. The air/gas ratio control
valve senses the pressure across the venturi and
supplies gas to pre-mix with air.
12) The igniter will spark for 4 seconds, with the gas valve
opened, and the fan running at ignition speed.
13) Spark igniter lights the air/gas mixture. The DynaMax
HS controller looks for a minimum flame rectification
signal of 0.8Vdc from the flame sensor. If the signal is
present the DynaMax HS Controller will allow the gas
valve to remain open. The burner is now firing at
starting input rate.
14) Boiler will modulate to the correct fan speed to meet
heat demand. The modulation rate is controlled via
pulse width modulation (PWM) signal.
15) Fan speed will slowly decrease as heat request nears
the heat demand. If heat demand is sustained for a
long duration of time the boiler will get to a point of
steady-state and the fan will rotate at constant speed.
16) When the heat demand is satisfied or is removed the
burner will shut off and the fan speed will ramp up to
the preset post-purge speed until the post-purge timer
is satisfied.
17) The boiler will then go into standby as it waits for the
next heat demand.
1.5.1
Heat Transfer Process
1) Burner input continues to increase until inlet water
temperature reaches the setpoint temperature.
2) Burner input may stabilize at a fixed rate where
demand equals input.
3) Burner input will decrease rate when outlet water
temperature approaches temperature Setpoint.
Содержание DynaMax DMH081
Страница 2: ......
Страница 12: ...7 Figure 5 DynaMax HS Wall Hung Service Clearances Figure 6 DynaMax HS Floor Mount Service Clearances...
Страница 68: ...65 PART 14 EXPLODED VIEW PARTS LIST DYNAMAX HS WALL HUNG...
Страница 69: ...66 DYNAMAX HS FLOOR MOUNT...
Страница 76: ...73 PART 15 ELECTRICAL DIAGRAMS 15 1 DM 80 299 INTERNAL WIRING DIAGRAM...
Страница 77: ...74 15 2 DM 399 800 INTERNAL WIRING DIAGRAM...
Страница 78: ...75...