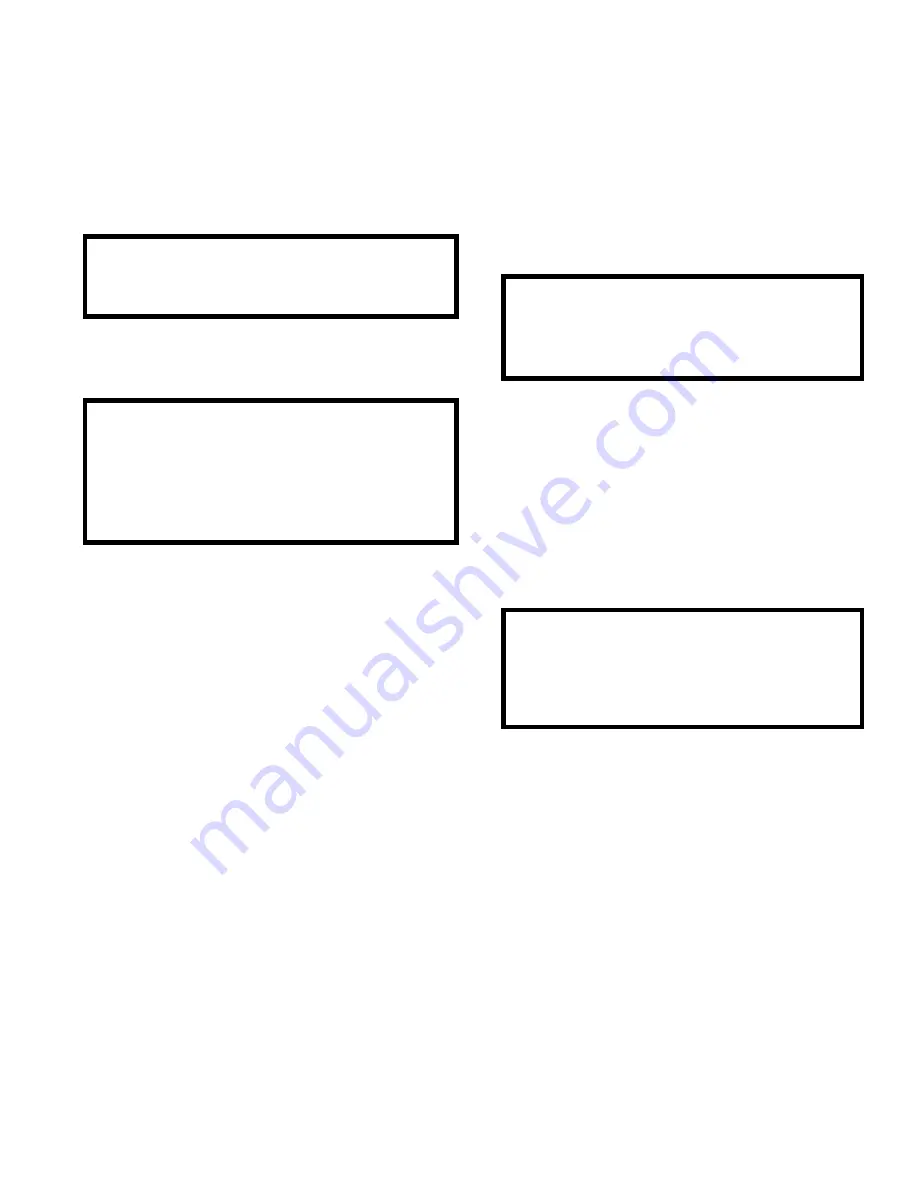
S-Series Technical Manual
81
Cambridge Air Solutions
GAS VALVE CLEANING
All solenoid valves should be cleaned periodically.
The time between cleanings will vary depending on
the medium and the service conditions. In general,
if the voltage to the coil is correct, sluggish valve
operation, excessive noise, or leakage will indicate
that cleaning is required. Refer to the Gas Valve Leak
Check procedure (page 58).
m
WARNING:
In the extreme case, the valve may fail to open or
fully close.
IMPORTANT
It is not necessary to remove the valve from the gas
train for cleaning.
m
WARNING:
Before servicing the valve, turn off the electrical
power, close the upstream manual gas valve,
depressurize
the
valve, extinguish all open flames
and avoid any type of sparking or ignition. Vent
hazardous or combustible fumes to a safe area.
ASCO Gas Valves: Series 8214
Disassemble the valve (page 82) and clean all parts as
follows:
IMPORTANT
If parts are worn or damaged, install a complete
ASCO Rebuild Kit.
1. Remove the solenoid enclosure.
2. Remove the bonnet screws, valve bonnet, bonnet
gasket, core/diaphragm subassembly and body
gasket.
3. Lubricate the bonnet gasket and body gasket with a
light coat of Dow Corning
®
200 Fluid lubricant or
an equivalent high-grade silicone fluid.
4. Apply a light coat of RemGrit TFL 50
®
Dry
Lubricant to: the valve seat; the valve body surface
where the diaphragm assembly contacts the valve
body and body gasket; and the internal surface of
the valve bonnet where the diaphragm assembly
contacts the bonnet when the valve is in the
energized (open) position.
IMPORTANT
If the valve has been disassembled for inspection
and cleaning only and a Rebuild Kit is not being
installed, lubricate the following with RemGrit TFL
50
®
Dry Lubricant:
• Diaphragm assembly on both sides
• Main disc at base of core/diaphragm sub-assembly
• Pilot disc at base of core assembly
m
CAUTION:
Do not distort the hanger spring between the core
assembly and the diaphragm assembly when
lubricating the pilot disc.
5. Replace the body gasket and the core/diaphragm
subassembly with the closing spring attached.
Locate the bleed hole in the core/diaphragm sub-
assembly approximately 30˚ counterclockwise from
the valve inlet.
6. Replace the valve bonnet and the bonnet screws.
Torque the screws in a crisscross manner to 100
± 10 in-lbs. Replace the solenoid and make the
electrical hookup.
m
WARNING:
Before returning to service, check the valve for
proper operation and perform Gas Valve Leak
Check and Gas Train Leak Check procedures
(page 27-28).
ORDERING INFORMATION FOR ASCO
REBUILD KITS
Parts marked with an asterisk (*) in the exploded
views are supplied in Rebuild Kits.
When ordering Rebuild Kits for ASCO valves,
order the Rebuild Kit number stamped on the valve
nameplate. If the number of the kit is not visible,
order by indicating the number of kits required,
and the Catalog Number and Serial Number of the
valve(s) for which they are intended.
Содержание S Series
Страница 93: ...S Series Technical Manual 91 Cambridge Air Solutions REFERENCE ELECTRICAL CONTROL ENCLOSURE ISOMETRIC DRAWING ...
Страница 100: ...Cambridge Air Solutions 98 S Series Technical Manual REFERENCE BUILDING AUTOMATION SYSTEM ...
Страница 112: ...Cambridge Air Solutions 110 S Series Technical Manual MAINTENANCE LOG MODEL NO SERIAL NO Date Activity Technician ...
Страница 113: ...MAINTENANCE LOG MODEL NO SERIAL NO Date Activity Technician ...
Страница 114: ...Cambridge Air Solutions 112 S Series Technical Manual ...
Страница 116: ...760 Long Road Crossing Dr Chesterfield MO 63005 Phone 636 532 2233 800 899 1989 Fax 636 530 6133 www cambridgeair com ...