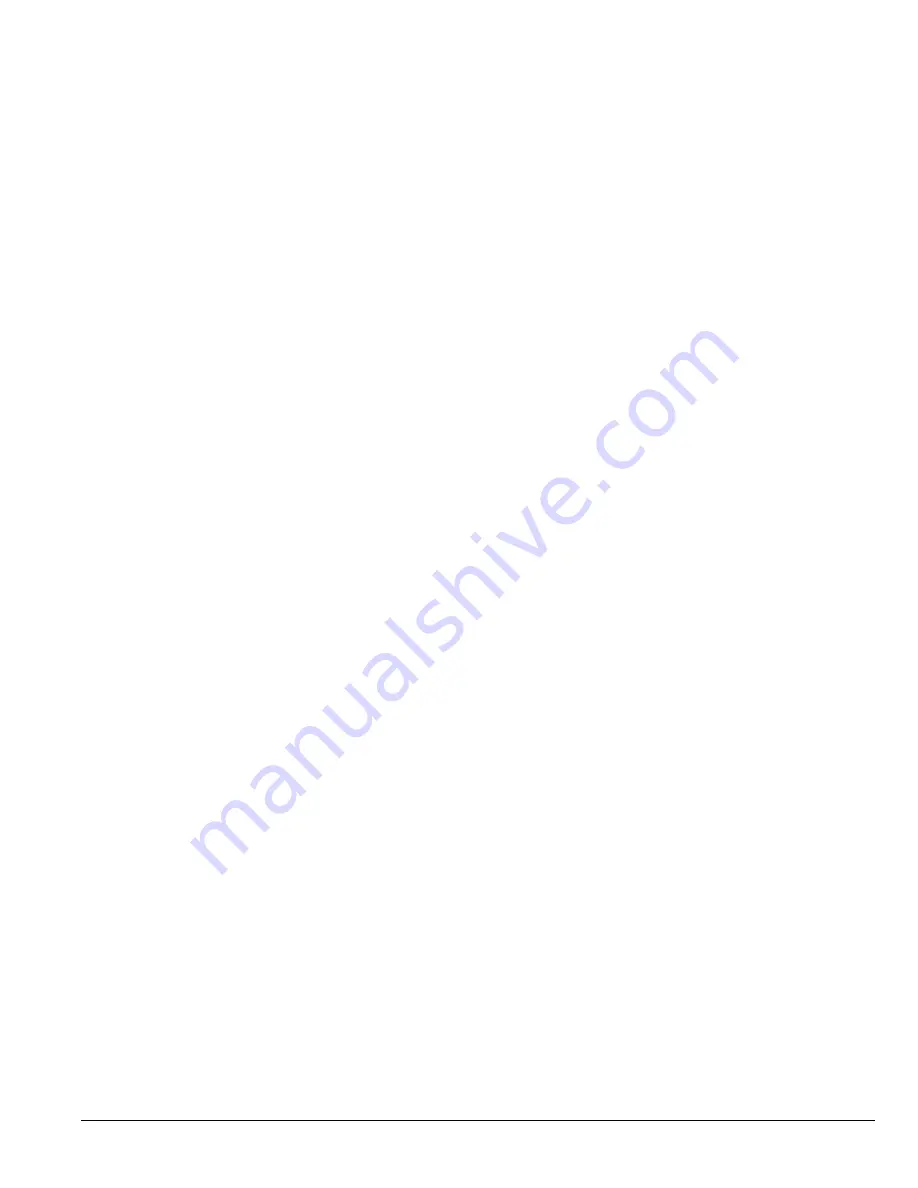
Control Wiring 5-27
MN765
5.12 Pre-Operation Checklist (Check of Electrical Items)
1. Verify AC line voltage at source matches control rating.
2. Inspect all power connections for accuracy, workmanship and tightness and compliance to codes.
3. Verify control and motor are grounded to each other and the control is connected to earth ground.
4. Check all signal wiring for accuracy.
5. Be certain all brake coils, contactors and relay coils have noise suppression. This should be an R-C filter for AC coils and
reverse polarity diodes for DC coils. MOV type transient suppression is not adequate.
5.13 Powerup Procedure
1. Remove all power from the control.
2. Verify that any enable inputs to J2-8 are open.
3. Disconnect the motor from the load (including coupling or inertia wheels).
4. Turn power on. Be sure there are no faults.
5. Set the Level 2 Output Limits block, “OPERATING ZONE” parameter as desired
(STD CONST TQ, STD VAR TQ, QUIET CONST TQ or QUIET VAR TQ).
6. If external dynamic brake hardware is used, set the Level 2 Brake Adjust block “Resistor Ohms” and “Resistor Watts”
parameters.
7. Enable the control (J2-8 connect to J3-24).
WARNING:
The motor shaft will rotate during this procedure. Be certain that unexpected motor shaft
movement will not cause injury to personnel or damage to equipment.
8. Select basic parameters from the main Keypad menu. Perform each step including “CALC MOTOR MODEL” (P2414).
9. Select “Advanced Prog”, Level 2 Blocks, Auto Tune, “One-Step Tuning” and run all tests.
10. Remove all power from the control.
11. Couple the motor to its load.
12. Verify freedom of motion of motor shaft.
13. Verify the motor coupling is tight without backlash.
14. Verify the holding brakes if any, are properly adjusted to fully release and set to the desired torque value.
15. Turn power on. Be sure no errors are displayed.
16. Execute “Speed Loop Tune” (Vector Mode Only).
17. Run the drive from the keypad using one of the following: the arrow keys for direct speed control, a keypad entered
speed or the JOG mode.
18. Select and program additional parameters to suit your application.
The control is now ready for use in the keypad mode. If a different operating mode is desired, refer to Chapter 5 Operating
Modes and Chapter 6 Using the Keypad.
Содержание VS1GV21-1B
Страница 1: ...10 11 Installation Operating Manual MN765 VS1GV AC Closed Vector Control...
Страница 12: ...2 2 General Information MN765...
Страница 16: ...3 4 Installing the Drive MN765...
Страница 78: ...6 16 Using the Keypad MN765...
Страница 132: ...9 14 Troubleshooting MN765...
Страница 169: ...Technical Specifications A 13 MN765 OM2000A11 Size B NEMA 4X Figure A 2 Drive Dimensions and Weights Continued...
Страница 172: ...A 16 Technical Specifications MN765...
Страница 200: ...E 2 Remote Keypad Mounting Template MN765...
Страница 201: ...Remote Keypad Mounting Template E 3 MN765...
Страница 202: ...E 4 Remote Keypad Mounting Template MN765...