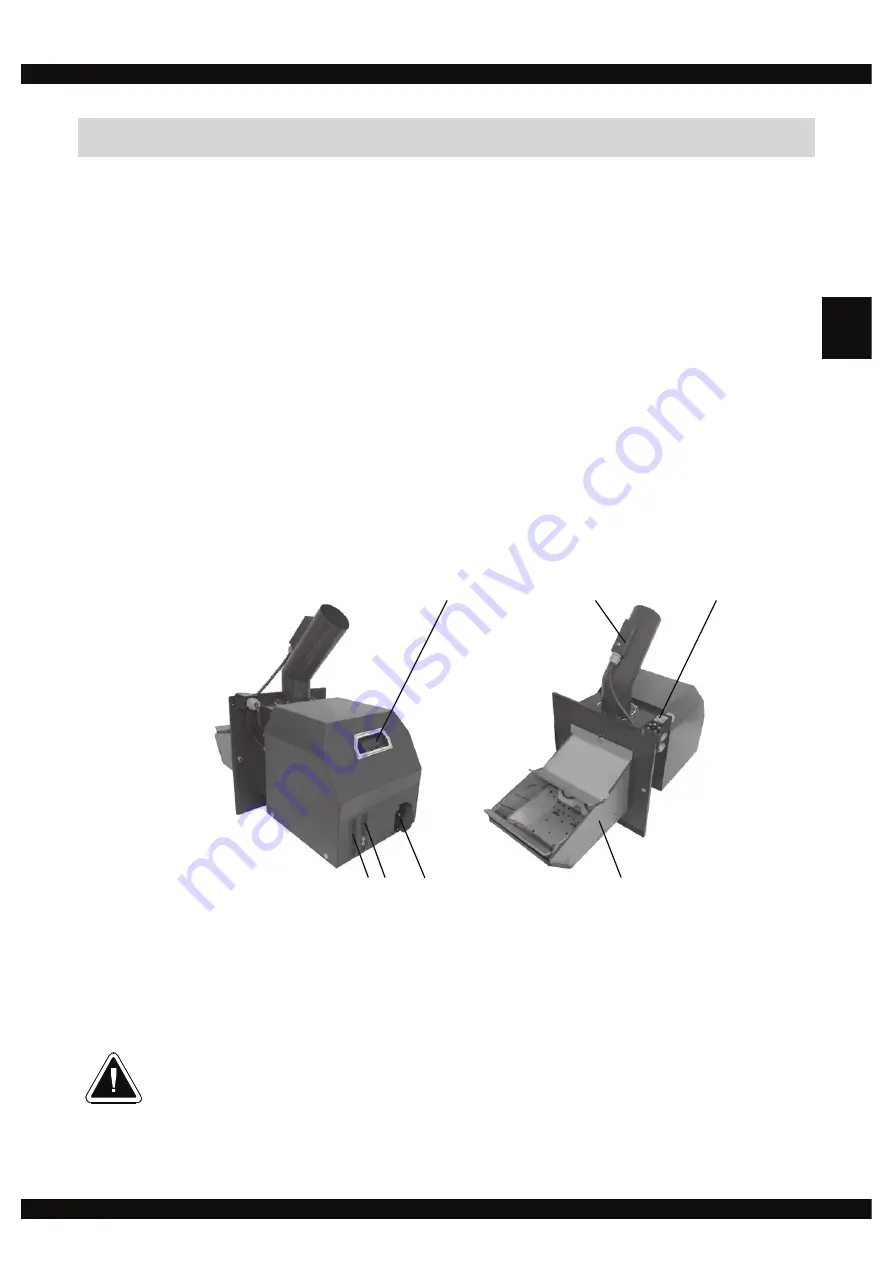
Operation and Maintenance Manual - GB
G
B
www.atmos.cz
GB-5
2. Design
Description
Heating with pellets with the use of the ATMOS A45 pellet burner has a lot in common with natural gas
or oil heating. However, there is a difference that burning of pellets produces a certain quantity of ashes that
must be removed from the burner and boiler in an interval to avoid impairment of efficiency or affecting the
functionality of the burner.
The ATMOS A45 pellet burner is supplied with automatic fuel ignition as standard. The assembly of the
burner, external conveyor and fuel bin work completely automatically during operation and is controlled by an
electronic control unit with the use of a flame sensor (photocell). In the burner body the fuel and combustion
air are supplied in such a way to ensure maximum efficiency and environment-friendliness of fuel burning.
Only high-quality pellets with the diameter of 6 to 8 mm and length of 5 to 25 mm should be fed into
the burner.
Pellets made of soft wood without bark, called white pellets, are considered as high quality
pellets.
Ashes are normally removed from the burner through the open door once every 7 to 30 days as necessary.
It is recommended to thoroughly clean the inner parts of the burner once a year; for this operation the burner
should be removed from the boiler. For ideal cleaning of the combustion chamber (pot) of the burner you can
use a special vacuum cleaner or a poker.
The burner consists of the following parts:
CAUTION
- For the A45 burner DRA50 external shaft conveyors with the length of 1,7, 2,5,
4 and 5m with the diameter of 80 mm and also DA50 external shaftless conveyors with the
lenght of 1,7 m with diameter of 90 mm are designed. If you use DA50 conveyors, there is nec-
esary to change the setup of the burner. Specifically the T4 and T6 parameters (T1 - increase,
T4 - increase, T6 - reduce, see table on the page 33).
1 - End switch
2 - Safety thermostat 95 °C
3 - Display of the electronic unit of
the burner
4 - Combustion chamber (mouth) of
the burner
5 - Socket for the external conveyor
6 - connector for interconnection cable between the
boiler and the burner (L1, L2, N, PE, R a R2)
7 - connector for connection of TS, TV, TK and TSV
sensors
3
6
5
2
4
1
7