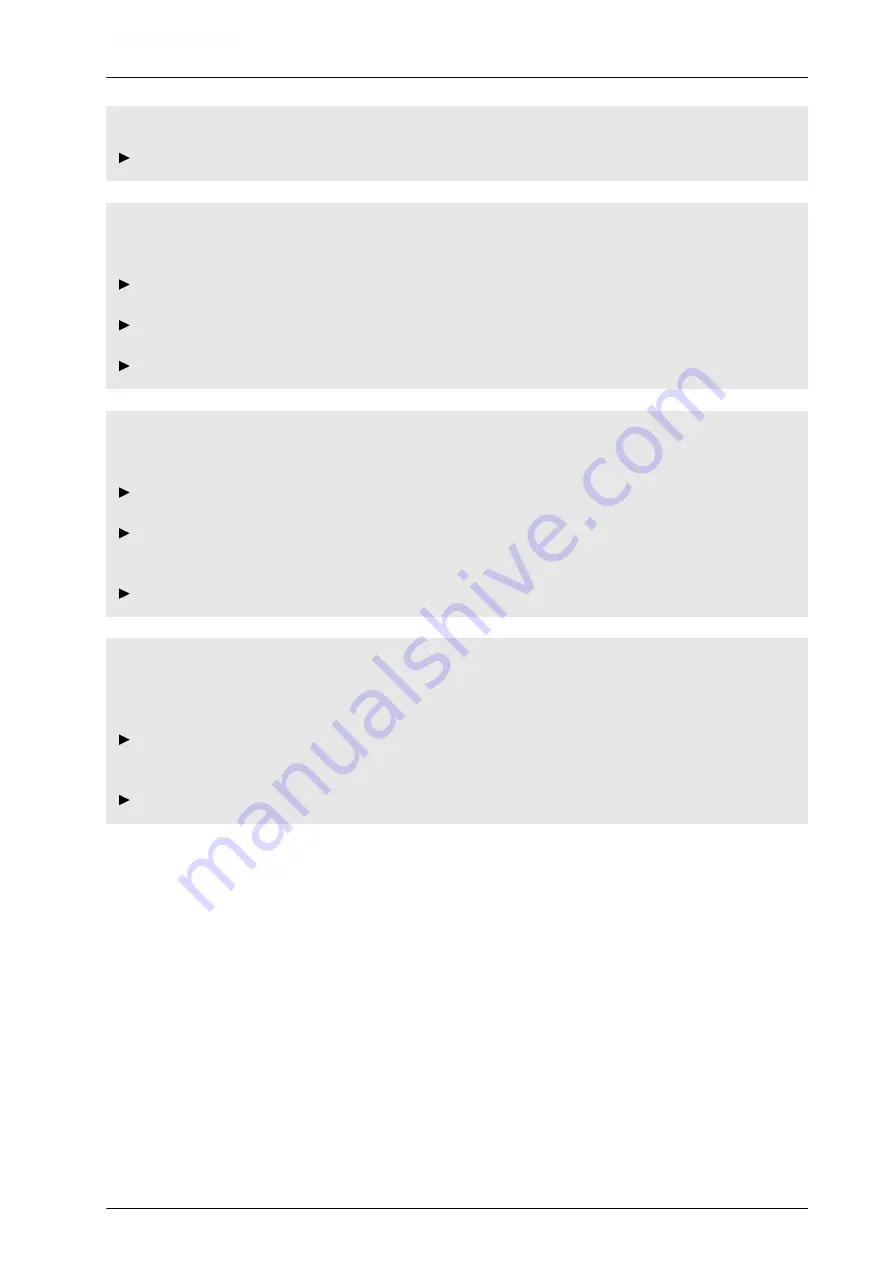
When driving on roads, risk of accident caused by uncontrolled lateral motions of the implement
Lock the tractor lower links for road travel.
Preparing the machine for road travel
If the machine is not properly prepared for road travel, it can result in serious traffic accidents.
Check the lighting and identification for road travel for proper function.
Remove coarse dirt from the implement.
Follow the instructions in the section "Preparing the implement for road travel".
Parking the implement
The parked machine can tip over. People can be crushed and killed.
Only park the machine on stable and even ground.
Before you perform setting or maintenance work,
make sure that the implement is in a stable position. In case of doubt, support the implement.
Follow the instructions in the section "Parking the implement".
Unsupervised parking
Parked tractors with coupled implements that are insufficiently secured and unsupervised represent danger
for people and playing children.
Before you leave the machine,
shutdown the tractor and the implement.
Secure the tractor and machine.
2 | Safety and responsibility
Basic safety instructions
MG6149-EN-GB | J.1 | 18.10.2022 | © AMAZONE
13