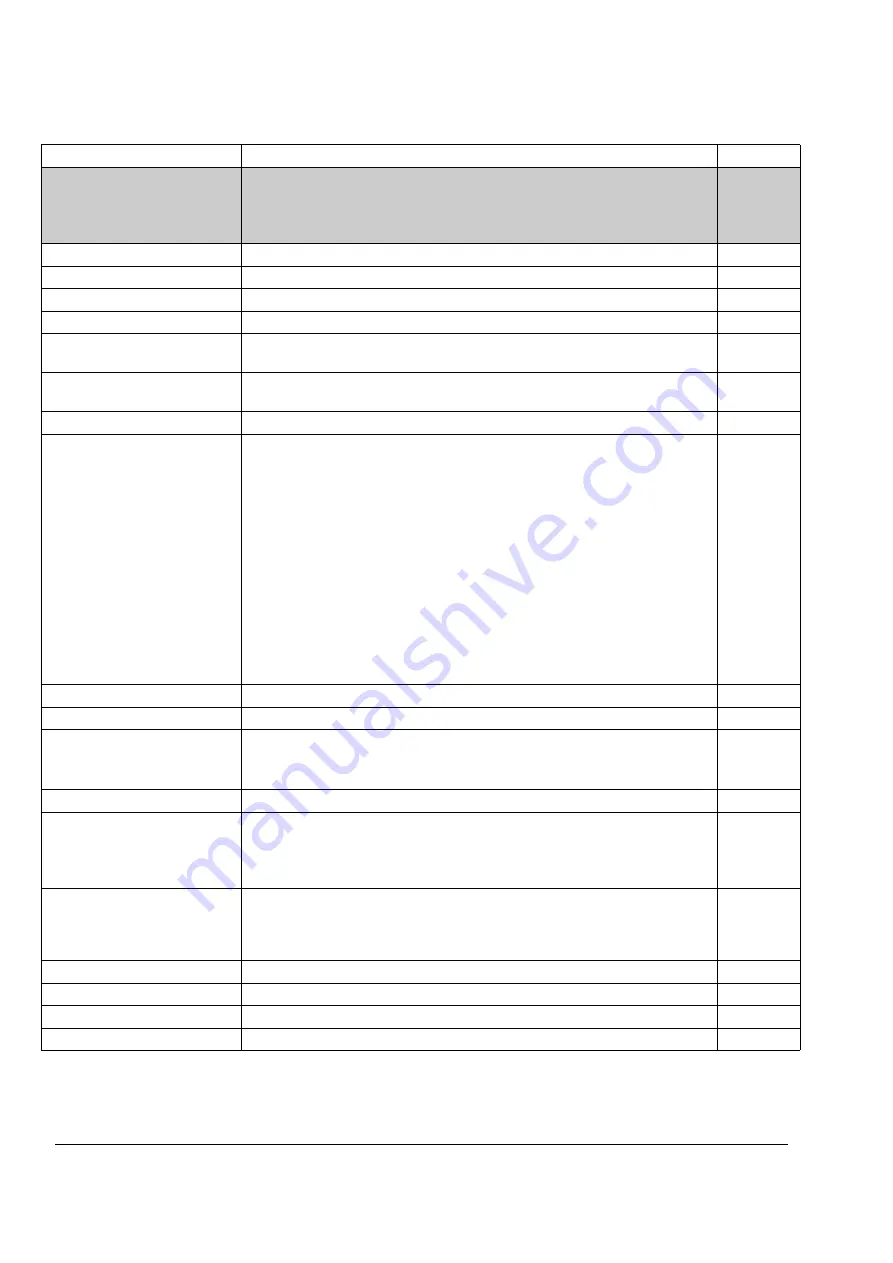
Actual signals and parameters
200
50 ENCODER MODULE
Encoder connection. Visible only when a pulse encoder module (optional) is
installed and activated with parameter
.
The settings will remain the same even though the application macro is
changed.
50.01
PULSE NR
States the number of encoder pulses per one revolution.
0 … 29999 ppr
Pulse number in pulses per round (ppr)
0 … 29999
50.02
SPEED MEAS MODE Defines how the encoder pulses are calculated.
A
-
-
B DIR
Channel A: positive edges calculated for speed. Channel B: direction.
0
A
-
-
-
Channel A: positive and negative edges calculated for speed. Channel B: not
used.
1
A
-
-
-
B DIR
Channel A: positive and negative edges are calculated for speed. Channel B:
direction.
2
A
-
-
-
B
-
-
-
All edges of the signals are calculated.
3
50.03
ENCODER FAULT
Defines the operation of the drive if a failure is detected in communication
between the pulse encoder and the pulse encoder interface module, or
between the module and the drive. Encoder supervision function activates if
either of the following conditions is valid:
-The difference between the estimated and measured speed is greater than
20% of the motor nominal speed.
- No pulses are received from the encoder within the defined time (see
parameter
) and the drive is simultaneously at the current or torque limit.
When the torque is zero or low, the shaft may not move and no pulses are
detected. This means that at low torque/current the missing-pulse-supervision
is not possible. Therefore there must be conditional torque or current limit in
the pulse supervision. Now the limit is the maximum torque/current, because
then the shaft is expected to move at least a little bit and at least some encoder
pulses are detected.
WARNING
The drive generates a warning indication.
0
FAULT
The drive trips on a fault, gives a fault indication and stops the motor.
65535
50.04
ENCODER DELAY
Defines the time delay for the encoder supervision function at start (See
parameter
Note
: It the delay is set to 0 ms, encoder supervision at start is disabled.
0 … 50000 ms
Time delay
0 … 50000
50.05
ENCODER DDCS CH Defines the fibre optic channel of the control board from which the drive
program reads the signals coming from the pulse encoder interface module.
The setting is valid only if the module is connected to the drive via the DDCS
link (that is not to the option slot of the drive).
CH 1
Signals via channel 1 (CH1). The pulse encoder interface module must be
connected to CH1 instead of CH2 in applications where CH2 is reserved by a
Master station (For example, a Master/Follower application). See also
parameter
1
CH 2
Signals via channel 2 (CH2). Can be used in most cases.
2
50.06
SPEED FB SEL
Defines the speed feedback value used in control.
INTERNAL
Calculated speed estimate
65535
ENCODER
Actual speed measured with an encoder
0
Index
Name/Selection
Description
FbEq
Содержание ACS 800 Series
Страница 1: ...ACS800 Firmware Manual Crane Control Program N697 ...
Страница 4: ......
Страница 26: ...Start up and control through the I O interface 26 ...
Страница 36: ...Quick start up guide 36 ...
Страница 52: ...Control panel 52 ...
Страница 105: ...Program features 105 Figure Control diagram for Shaft synchronisation executed in 20 ms ...
Страница 126: ...Program features 126 The figures below show speed limits according to different load conditions ...
Страница 128: ...Program features 128 ...
Страница 150: ...Application macros control location EXT1 EXT2 150 ...
Страница 228: ...Actual signals and parameters 228 ...
Страница 299: ...Adaptive Programming examples for crane control 299 ...
Страница 305: ...Adaptive Programming examples for crane control 305 ...
Страница 312: ...Adaptive Programming examples for crane control 312 The following figures show the previous example enlarged ...
Страница 314: ...Adaptive Programming examples for crane control 314 The following figures show the previous example enlarged ...
Страница 318: ...Analogue Extension Module 318 ...
Страница 332: ...Additional data actual signals and parameters 332 ...
Страница 333: ...DriveWindow 333 DriveWindow DriveWindow connected to the ACS800 RMIO RDCO board and channel CH3 ...
Страница 334: ...DriveWindow 334 ...
Страница 335: ...Control block diagrams 335 Control block diagrams ...
Страница 336: ...Control block diagrams 336 ...
Страница 337: ...Control block diagrams 337 ...
Страница 338: ...Control block diagrams 338 ...
Страница 340: ...www abb com drives www abb com drivespartners Contact us 3AFE68775230 Rev E EN 2012 09 25 ...