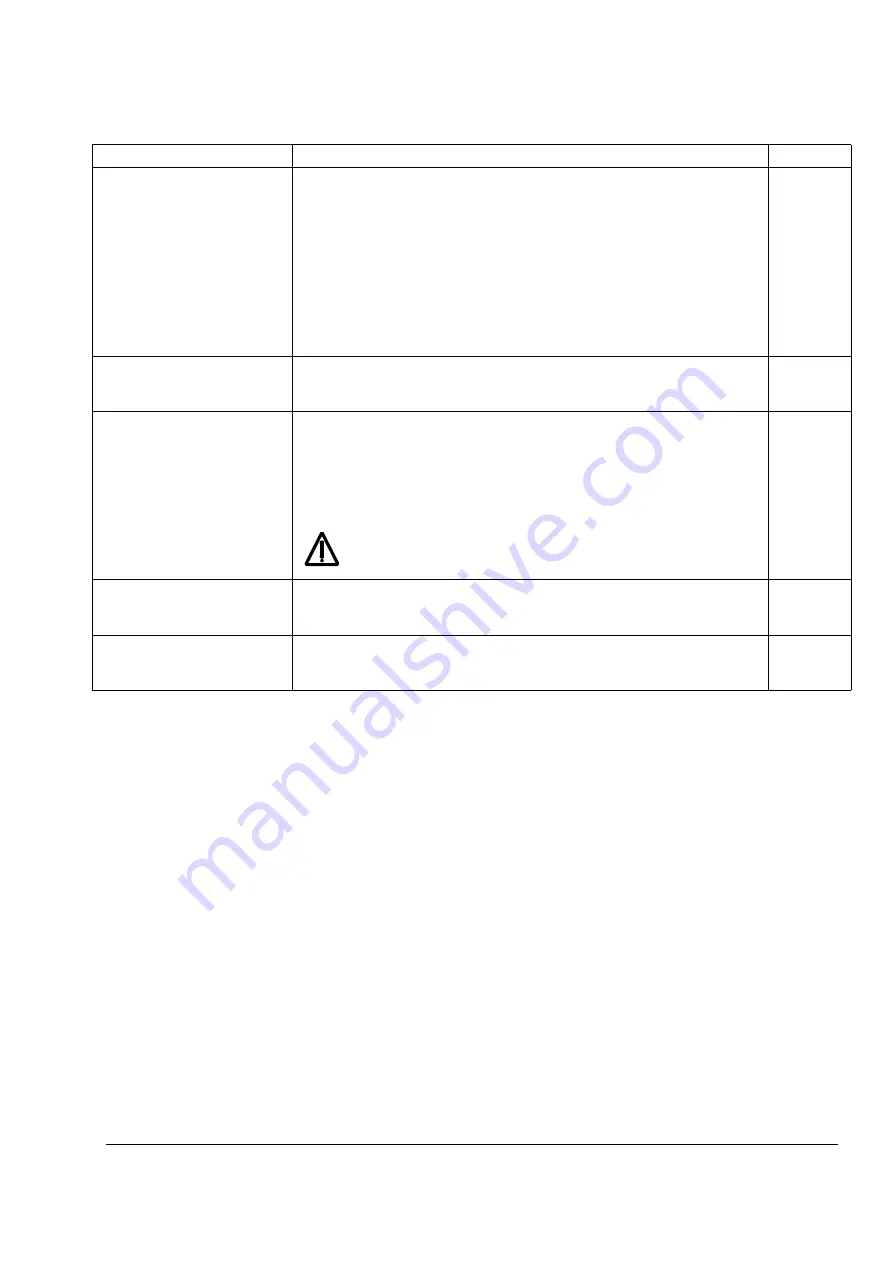
Actual signals and parameters
227
99.10
MOTOR ID RUN
MODE
Selects the type of the motor identification. During the identification, the drive
will identify the characteristics of the motor for optimum motor control. The ID
run procedure is described in chapter
Start-up and control through the I/O
Note:
The ID run (STANDARD or REDUCED) should be selected if:
- The operation point is near zero speed, and/or
- Operation at torque range above the motor nominal torque within a wide
speed range and without any measured speed feedback is required.
Note:
The ID run (STANDARD) cannot be performed if parameter
SCALAR.
ID MAGN
No ID run. The motor model is calculated at first start by magnetising the motor
for 20 to 60 s at zero speed. This can be selected in most applications. The
brake is kept closed during ID MAGN Run.
1
STANDARD
Standard ID run. Guarantees the best possible control accuracy. The ID run
takes about one minute. The brake is opened when STANDARD ID run is
selected. The brake gets closed once the STANDARD ID run is performed.
Note:
The motor must be de-coupled from the driven equipment.
Note:
Check the direction of rotation of the motor before starting the ID run.
During the run, the motor will rotate in the forward direction.
WARNING!
The motor will run at up to approximately 50 … 80% of the
nominal speed during the ID run. ENSURE THAT IT IS SAFE TO RUN
THE MOTOR BEFORE PERFORMING THE ID RUN!
2
99.11
DEVICE NAME
Defines the name for the drive or application. The name is visible on the
control panel display in the Drive Selection Mode.
Note:
The name can be
typed only by using a drive PC tool.
99.12
OEM SIGNAL
Defines the text for the OEM signal. The signal can be displayed on the control
panel display by selecting the actual parameter
Note:
The name can be
entered only by using a drive PC tool.
Index
Name/Selection
Description
FbEq
Содержание ACS 800 Series
Страница 1: ...ACS800 Firmware Manual Crane Control Program N697 ...
Страница 4: ......
Страница 26: ...Start up and control through the I O interface 26 ...
Страница 36: ...Quick start up guide 36 ...
Страница 52: ...Control panel 52 ...
Страница 105: ...Program features 105 Figure Control diagram for Shaft synchronisation executed in 20 ms ...
Страница 126: ...Program features 126 The figures below show speed limits according to different load conditions ...
Страница 128: ...Program features 128 ...
Страница 150: ...Application macros control location EXT1 EXT2 150 ...
Страница 228: ...Actual signals and parameters 228 ...
Страница 299: ...Adaptive Programming examples for crane control 299 ...
Страница 305: ...Adaptive Programming examples for crane control 305 ...
Страница 312: ...Adaptive Programming examples for crane control 312 The following figures show the previous example enlarged ...
Страница 314: ...Adaptive Programming examples for crane control 314 The following figures show the previous example enlarged ...
Страница 318: ...Analogue Extension Module 318 ...
Страница 332: ...Additional data actual signals and parameters 332 ...
Страница 333: ...DriveWindow 333 DriveWindow DriveWindow connected to the ACS800 RMIO RDCO board and channel CH3 ...
Страница 334: ...DriveWindow 334 ...
Страница 335: ...Control block diagrams 335 Control block diagrams ...
Страница 336: ...Control block diagrams 336 ...
Страница 337: ...Control block diagrams 337 ...
Страница 338: ...Control block diagrams 338 ...
Страница 340: ...www abb com drives www abb com drivespartners Contact us 3AFE68775230 Rev E EN 2012 09 25 ...