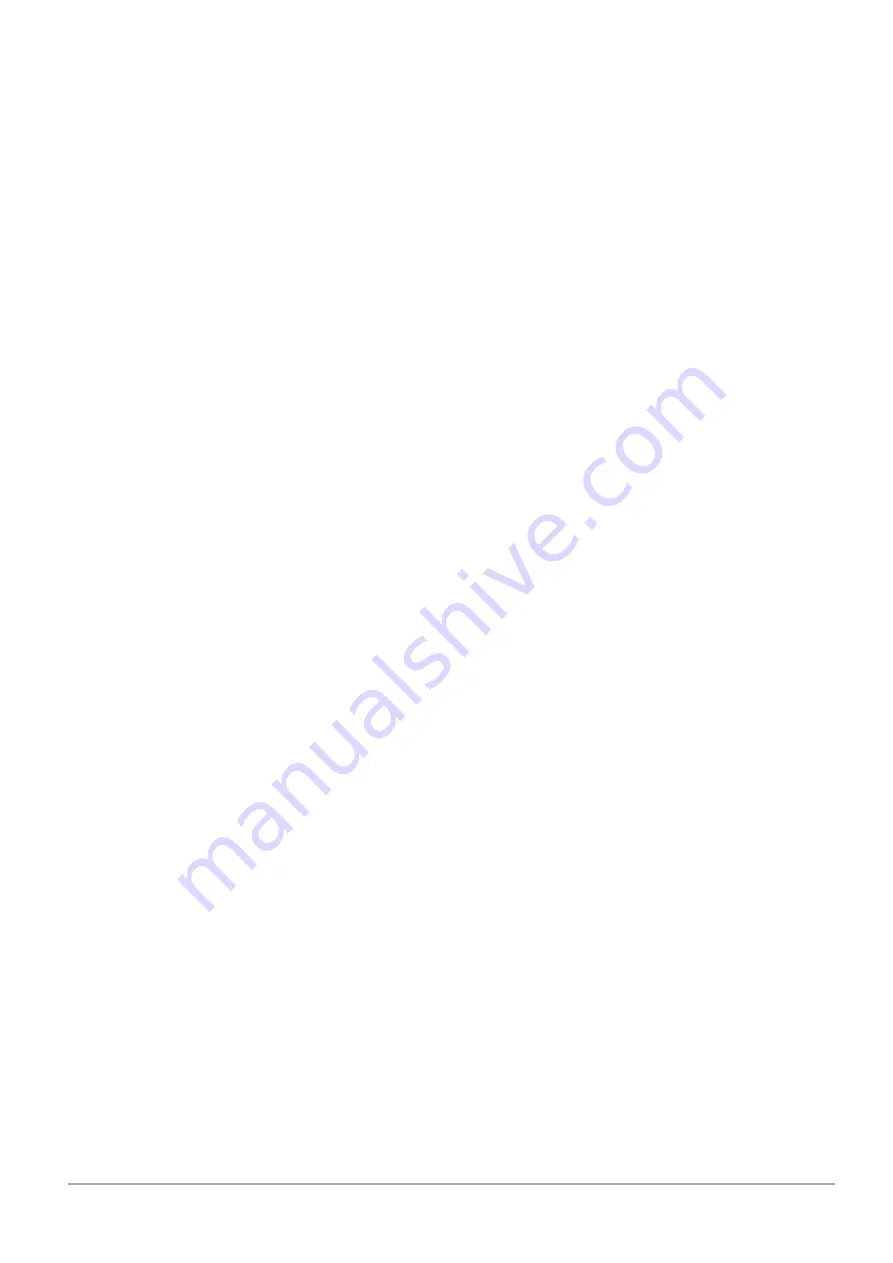
Page
42
of
44
3DGence Material Management System | version 1 | 03.2022
X GLOSSARY
ABS
(polyacrylonitrile-butadiene-styrene) - one of the main consumables of 3D printers, next to PLA. It is characterised by high
impact strength, hardness and scratch resistance. It is not resistant to UV radiation. Soluble in acetone, which allows post-
production of prints by acetone vaporisation. ABS prints can also be glued together with an ABS solution in acetone. ABS has a
fairly significant thermal shrinkage (up to 0.7%). The typical operating temperature for ABS printing is 220 -
250°C and about
100°C for the work platform. A heated workspace is necessary to maintain the dimensional consistency of the printed elements.
Adhesion
–
in the context of 3D printing, the adhesion of the print to the working platform of the device. Insufficient adhesion
of the printout may result in partial or complete detachment of the printout from the table during printer operation. Grease
or dirt on the table adversely affects adhesion.
Bridge
–
a part of the model printed in the air, suspended between two parts of the print. It is subject to special recalculation
when preparing the file for printing. If the bridge is too long, it may become deformed. In such cases, the printing element
must be supported by supporting structures.
Brim
–
a way to improve the adhesion of prints to the working platform. It consists in increasing the area of adhesion to the
platform by generating additional, external contours of the actual solid at the level of the first print layer. The more contour
lines are added, the greater the area of adhesion. Usually between 5 and 20 additional contours (brim lines) are used. The brim
should be used if there are problems with the print peeling off the working platform.
CAD (Computer Aided Design)
–
a collective term for various computer-aided design processes. The CAD methodology is used
in mechanical, electrical, medical and architectural engineering, among others. The CAD methodology is based on geometric
modelling to create a two- or three-dimensional representation of the component being designed. Multiple CAD software
packages are available to suit your needs and requirements. Models in STL or OBJ formats are exported from these programs
for 3D printing. The most popular are: SolidWorks, Inventor, PTC Creo, CATIA, Rhino, SolidEdge - however, there are many
others.
Curling
–
a negative phenomenon occurring during 3D printing with the FFF technique. Curling can most often be seen when
printing overhangs or sharply folded elements of solids. It consists of curling up the edges of the print. In extreme cases it can
lead to print failure. However, it always adversely affects the visual aspect, especially of the bottom surfaces of the print. It
also leads to the print head colliding with the print during operation. The primary method to combat curling is to actively cool
the print. If running the fans does not help, it is worth reducing the print speed.
Model slicing
–
a process to generate paths and instructions for the printer (machine code) from a 3D model. At the slicer level,
settings such as layer height, print speed, fill density, solid wall thickness or temperatures for the nozzle and working platform
are selected. In addition, you can choose the use and density of supports and one of several ways to improve the adhesion of
the print to the working platform (e.g. raft or brim). The 3DGence INDUSTRY F350 printer uses the 3DGence SLICER 4.0
software, where settings for different modules and resolutions have been defined. The final result of the slicers is a machine
code representing the given 3D model in the form of a G-code which is interpreted by the printer's electronics.
Nozzle
- the part of the print head that is in direct contact with the printout. When heated to the correct temperature, it
liquefies the material and forms a plastic thread with the nominal diameter of the nozzle. The nozzle output diameter affects
the available resolutions, speed and accuracy of the print.
Extruder
–
a part of the 3D printer working in the FFF technology. Its task is to feed the filament at a precisely defined rate and
thus quantity. The 3DGence INDUSTRY F350 is fitted with a Direct type of extruder. This means that the extruder motors are
located directly above the printing module, feeding the material to the print heads via sleeves.
Endstop / limit switch / end position sensor
–
an optoelectronic switch that limits the movement of the 3D printer beyond the
maximum allowed movement. The optical endstop does not require physical contact with the corresponding cutter which
guarantees a long service life. However, attention should be paid to its sensitivity to bright light sources which may cause false
activation.
Filament
–
a common term for FFF printing material. Filament is a wire made of a thermoplastic material (PLA, ABS, HIPS, PC,
Nylon and others) within a certain tolerance. The filament is wound on a spool. Important parameters when choosing a filament
are the manufacturing tolerance and the way it is protected from moisture (preferably the filament is vacuum-packed with a
moisture absorber). The large diameter of the spool hub will ensure that the entire length can be used - excessive bending of