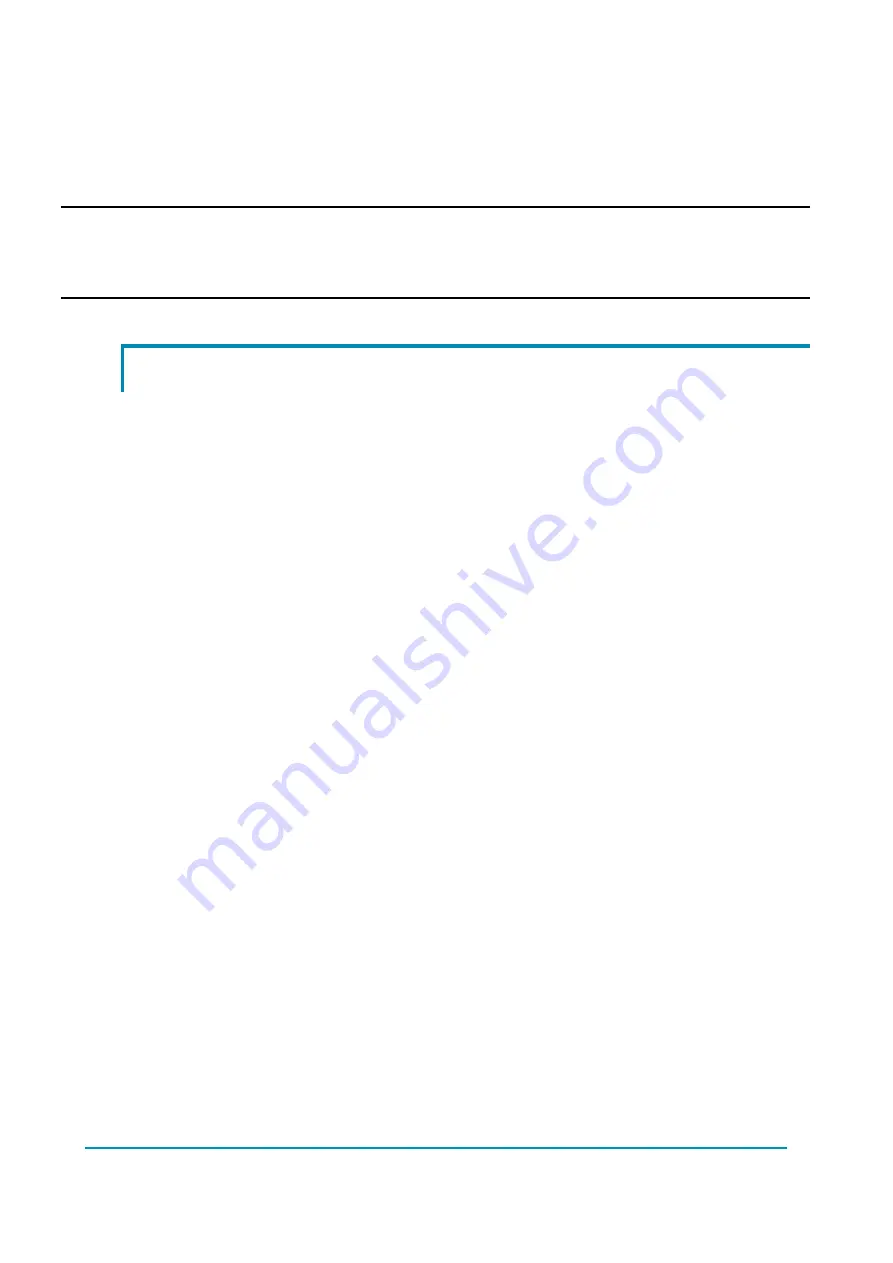
AFMNA0AA – EPS-BLI HYG – User Manual
Page – 19/75
7 INSTALLATION
PROCEDURE
For mass production cautions on correctness of the connecting drawing (according
figure 10-1) and of the mechanical installation are recommended.
U
For the correctness of the installation and for minimizing the risk of troubles,
please read and adopt accurately advices of topic 14 (installation requirements &
recommendations).
7.1 Prototype installation procedure
This procedure is relative to the connecting drawings in Figure 10-1. It is valid for both
steered wheel with and without mechanical hard stops. When mechanical hard stops are
present, cautions must be taken in order the angle of the steered wheel to be electrically
controlled and limited with margin before impacting the hard stops.
It describes the step by step installation procedure to get the prototype working.
For every truck released on the field, the correct installation set-up is already known and
so only quick set-up is required (see 8.2).
Carry out the procedure in the following order.
Step1
Lift up the steered wheel from the floor.
Step2
Connect the parts as for the connecting drawing in Figure 10-1 except for the
PBATT connections. Up to three wires 1.5 mm
2
for NBATT are foreseen (same
for PBATT). Total current rating for three 1.31 mm
2
PVC wires is about 36 A @
Tamb = 40°C. Total current rating for two 1.31 mm
2
PVC wires is about 26.5 A
@ Tamb = 40°C. Total current rating for three pins of the AMPSEAL connector
in the tin plated part number is 21 A (bottleneck).
Step3
Move mechanically the steered wheel in the straight ahead orientation.
Step4
Switch on the key and with the Zapi Can Console (or with the Zapi hand set in
a remote mode from another unit in the truck) check the reading CENTER
WHEEL SW in the tester menu is ON (meanwhile the steered wheel is straight
ahead). If it is not, there is a problem in the steered wheel sensor.
Step5
With the Zapi PC CAN Console (or with the Zapi hand set in a remote mode
from another unit in the truck) check the adjustment SET STEER 0-POS is 0°.
Step6
With the Zapi PC CAN Console (or with the Zapi hand set in a remote mode
from another unit in the truck) set parameters 1ST ANGLE GAIN and 2ND
ANGLE GAIN to values compatible with the position of the mechanical hard
stops (to avoid the steered wheel impacts the mechanical hard stops).
Step7
Connect the battery to the controller.
Step8
Switch on the key. The system should start steering.
Step9
Turn to topic 8 SETTING THE E-STEERING MOTOR CONTROLLER.