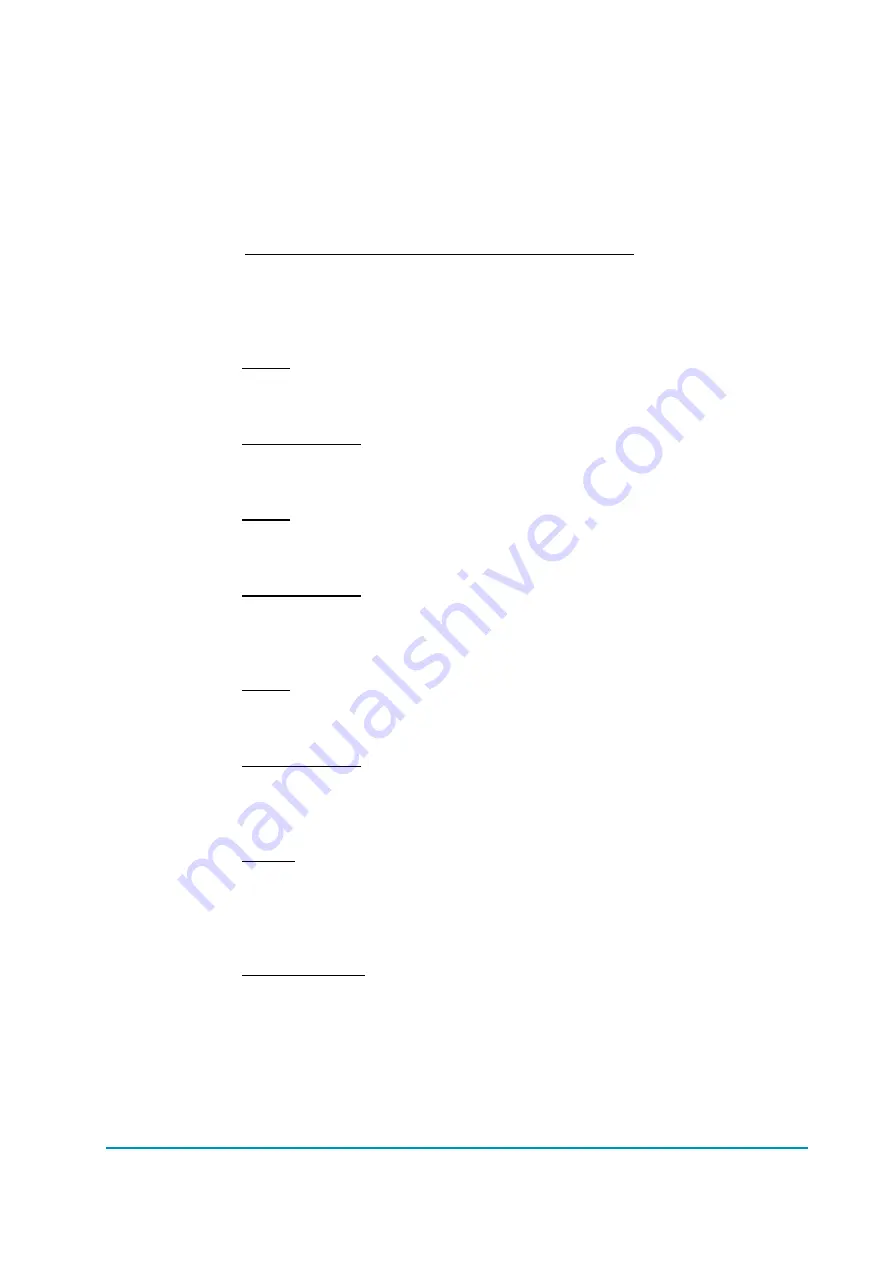
AF6ZP0CA – COMBIAC0 & ACE0 2uC – User Manual
Page – 133/155
-
Fault can be caused by a key input signal characterized by pulses below
the undervoltage threshold, possibly due to external loads like DC/DC
converters starting-up, relays or contactors during switching periods,
solenoids energizing or de-energizing. Consider to remove such loads.
-
If no voltage transient is detected on the supply line and the alarm is
present every time the key switches on, the failure probably lies in the
controller hardware. Replace the logic board.
Troubleshooting (fault displayed during motor driving)
-
If the alarm occurs during motor acceleration or when there is a
hydraulic-related request, check the battery charge, the battery health
and power-cable connections.
LOGIC FAILURE #3
(MDI/LED code = 17)
Cause
A hardware problem in the logic board due to high currents (overload). An
overcurrent condition is triggered even if the power bridge is not driven.
Troubleshooting
The failure lies in the controller hardware. Replace the controller.
NO CAN MSG. XX
(MDI/LED code = 67)
Cause
CANbus communication does not work properly. The hexadecimal value “XX”
identifies the faulty node.
Troubleshooting
-
Verify the CANbus network (external issue).
-
Replace the logic board (internal issue).
NO CAN WR MSG.XX
(MDI/LED code = 67)
Cause
CANbus communication does not work properly. The hexadecimal value “XX”
identifies the faulty node.
Troubleshooting
-
Verify the CANbus network (external issue).
-
Replace the logic board (internal issue).
OUT MISMATCH XX
(MDI/LED code = 16)
Cause:
This is a safety related test. Supervisor
μ
C has detected that master
μ
C is
driving the traction motor in a wrong way (not corresponding to the operator
request). The hexadecimal value “XX” facilitates Zapi technicians debugging
the problem.
Troubleshooting:
-
Checks the matching of the parameters between Master and Supervisor.
-
Ask for assistance to a Zapi technician.
-
If the problem is not solved, replace the logic board.
Summary of Contents for ACE0 2mC
Page 14: ...Page 14 155 AF6ZP0CA COMBIAC0 ACE0 2uC User Manual 3 2 2 AC Pump configuration...
Page 15: ...AF6ZP0CA COMBIAC0 ACE0 2uC User Manual Page 15 155 3 2 3 AC CAN Open configuration...
Page 16: ...Page 16 155 AF6ZP0CA COMBIAC0 ACE0 2uC User Manual 3 2 4 PMSM Traction configuration...
Page 17: ...AF6ZP0CA COMBIAC0 ACE0 2uC User Manual Page 17 155 3 2 5 PMSM Pump configuration...
Page 98: ...Page 98 155 AF6ZP0CA COMBIAC0 ACE0 2uC User Manual Torque curves...