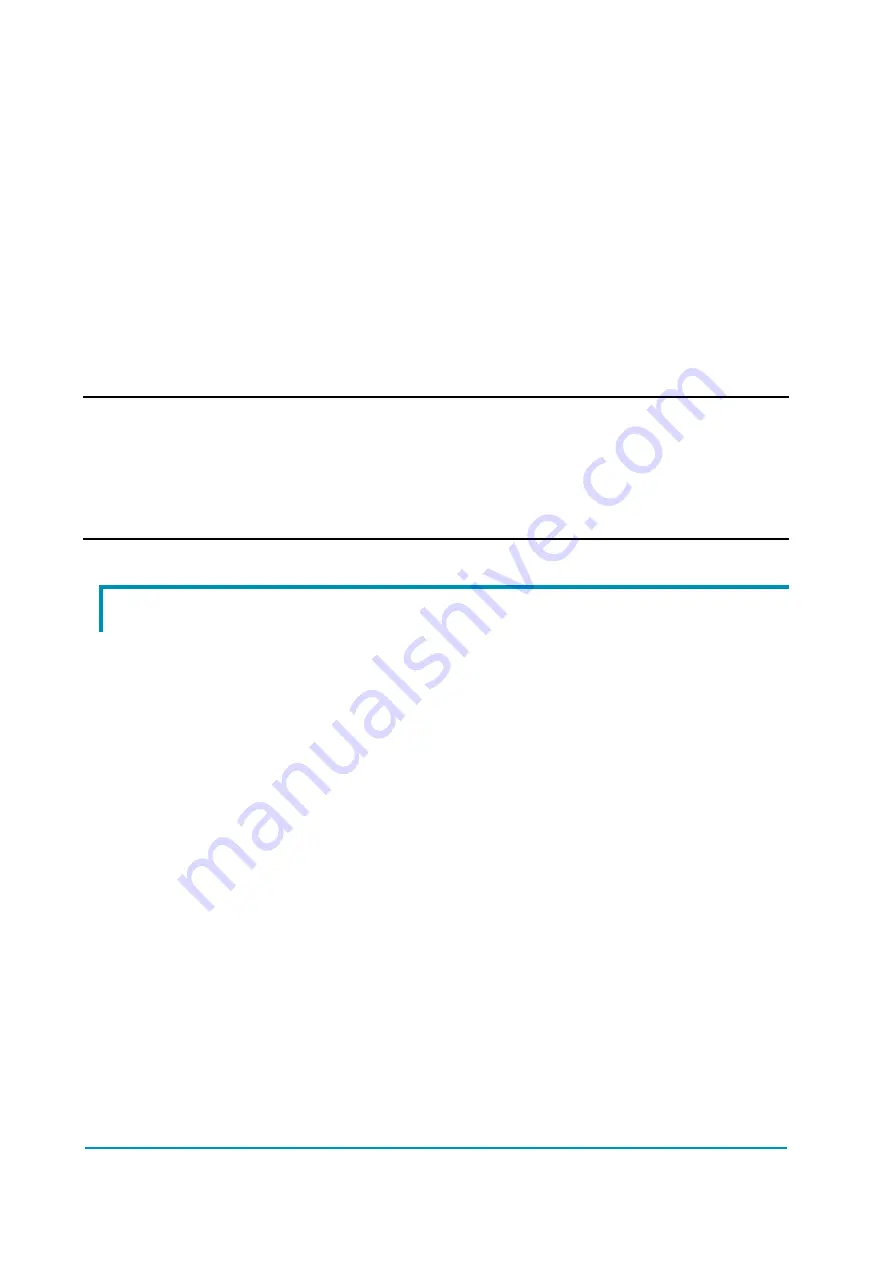
Page – 34/155
AF6ZP0CA – COMBIAC0 & ACE0 2uC – User Manual
5 INSTALLATION HINTS
This section presents a general procedure for startup and verification of
ACE0/COMBIAC0 controller after installation on a vehicle.
The motor controller is a software configurable device. In a CAN supervisor
system, some or all aspects of setup and operations may be managed by a
vehicle master controller communicating over the CAN bus. For standalone
operation (primarily the I/O version), customized software must be installed in the
motor controller.
Built-in diagnostics functions monitor battery voltage, heat-sink temperature,
motor temperature and other conditions. Error and warning events are available
to the master controller, stored in a log for service access (see chapter 10)
Events log provides additional information as well as procedures for pinpointing
and eliminating causes for warnings and errors.
U
Wiring errors, improper setup or other conditions may cause the vehicle to
move in the wrong direction or at the wrong speed.
U
Take necessary precautions to prevent injury to personnel or damage to
equipment before applying power for the first time.
5.1 Material
overview
Before starting the inverter, it is necessary to have the required material for a
correct installation. Wrong choice of additional parts could lead to failures,
misbehaviors or bad performance.
5.1.1 Connection
cables
For the auxiliary circuits, use cables of 0.5 mm² section.
For power connections to the motor and from the battery, use cables having
proper section. The screwing torque for the controller power connection must be
comprised in the range 5.6 Nm ÷ 8.4 Nm. For the optimum inverter performance,
the cables to the battery should be run side by side and be as short as possible.
5.1.2 Contactors
Main contactor has always to be installed. The output driving the coil is
modulated with a 1 kHz PWM basing on parameters MC VOLTAGE and MC
VOLTAGE RED. . After an initial delay of about 1 second, during which the coil is
driven with a percentage of VBATT defined by MC VOLTAGE, PWM reduces the
mean voltage down to the percentage set in MC VOLTAGE RED. . This feature is
useful to decrease the power dissipation of the coil and its heating.
5.1.3 Fuses
-
Use a 10 A fuse for protection of the auxiliary circuits.
-
For the protection of the power unit, refer to chapter 10.5. The fuse value
shown is the maximum allowable. For special applications or requirements
these values can be reduced.
-
For safety reasons, we recommend the use of protected fuses in order to
prevent the spreading of particles in case a fuse blows.
Summary of Contents for ACE0 2mC
Page 14: ...Page 14 155 AF6ZP0CA COMBIAC0 ACE0 2uC User Manual 3 2 2 AC Pump configuration...
Page 15: ...AF6ZP0CA COMBIAC0 ACE0 2uC User Manual Page 15 155 3 2 3 AC CAN Open configuration...
Page 16: ...Page 16 155 AF6ZP0CA COMBIAC0 ACE0 2uC User Manual 3 2 4 PMSM Traction configuration...
Page 17: ...AF6ZP0CA COMBIAC0 ACE0 2uC User Manual Page 17 155 3 2 5 PMSM Pump configuration...
Page 98: ...Page 98 155 AF6ZP0CA COMBIAC0 ACE0 2uC User Manual Torque curves...