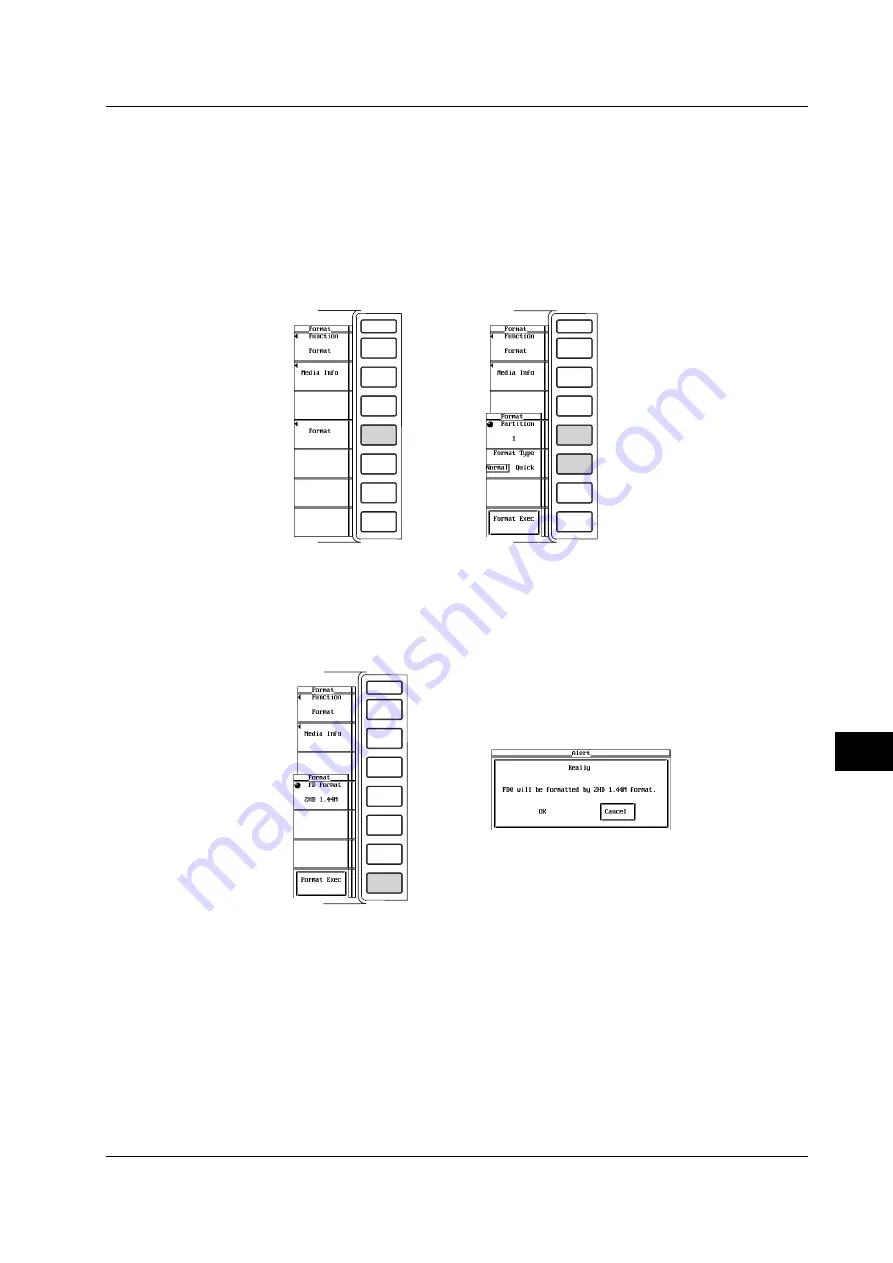
12-7
IM 253710-01E
Saving and Loading the Data
12
Selecting the format type for the SCSI device
6.
Press the [Format] soft key to display the format selection menu.
• Selecting the number of partitions
7.
Turn the jog shuttle to select the number from [1] to [10]
*
.
*
“5” for products (PZ4000) with firmware version before 2.01.
• Selecting the format type
8.
Press the [Format Type] soft key to select [Normal] or [Quick].
Executing and Canceling the format operation
9.
Press the [Format Exec] soft key. An Alert dialog box is displayed.
10.
Turn the jog shuttle to select [OK] or [Cancel].
11.
Selecting [OK] and pressing the SELECT key executes the format operation.
Selecting [Cancel] and pressing the SELECT key will not format the medium.
Viewing the information about the medium
6.
Press the [Media Info] soft key to display the information about the medium that
was selected in step 5.
12.4 Formatting the Disk