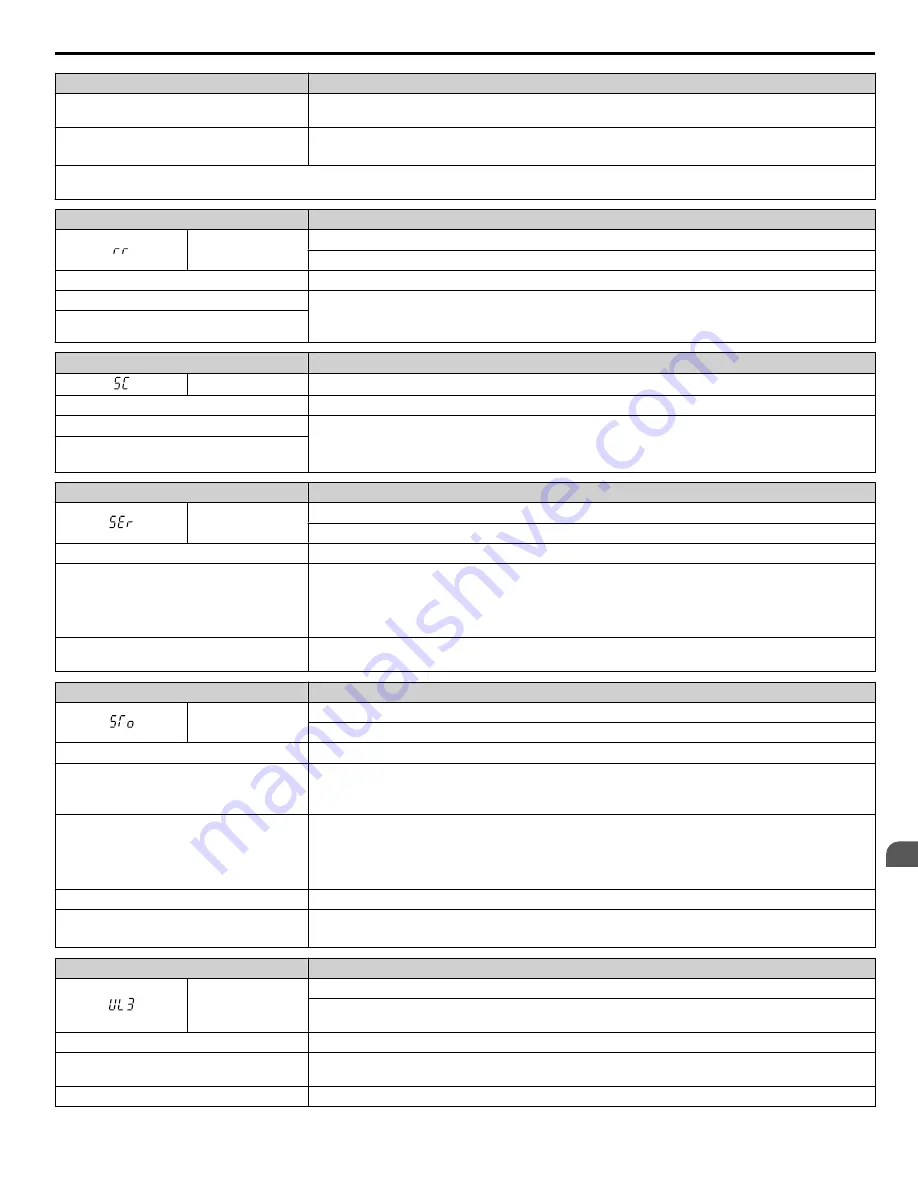
Digital Operator Display
Fault Name
Excessive braking inertia.
Recalculate braking load and braking power. Then try reducing the braking load and checking the braking
resistor settings and improve braking capacity.
The proper braking resistor has not been
installed.
• Check the specifications and conditions for the braking resistor device.
• Select the optimal braking resistor.
Note:
The magnitude of the braking load trips the braking resistor overheat alarm, NOT the surface temperature. Using the braking resistor more frequently
than its rating trips the alarm even when the braking resistor surface is not very hot.
Digital Operator Display
Fault Name
rr
Dynamic Braking Transistor
The built-in dynamic braking transistor failed.
Cause
Possible Solution
The braking transistor is damaged.
• Cycle power to the drive and check if the fault reoccurs.
Refer to Diagnosing and Resetting Faults
.
• Replace the drive if the fault continues.
The control circuit is damaged.
Digital Operator Display
Fault Name
SC
IGBT Short Circuit
Cause
Possible Solution
IGBT fault
• Check motor wiring
• Cycle power to the drive.
• If the problem continues, contact your Yaskawa representative or the nearest Yaskawa sales office.
IGBT short circuit detection and circuit fault
Digital Operator Display
Fault Name
SEr
Too Many Speed Search Restarts
The number of speed search restarts exceeded the number set to b3-19.
Cause
Possible Solution
Speed Search parameters are set to the wrong
values.
• Reduce the detection compensation gain during Speed Search (b3-10).
• Increase the current level when attempting Speed Search (b3-17).
• Increase the detection time during Speed Search (b3-18).
• Repeat Auto-Tuning.
The motor is coasting in the opposite direction
of the Run command.
Set b3-14 to 1 to enable Bi-directional Speed Search.
Digital Operator Display
Fault Name
STo
Motor Pull Out or Step Out Detection
Motor pull out or step out has occurred. Motor has exceeded its pull out torque.
Cause
Possible Solution
The wrong motor code has been set (Yaskawa
motors only).
• Enter the correct motor code for the PM being used into E5-01.
• For special-purpose motors, enter the correct data to all E5 parameters according to the Test Report
provided for the motor.
Load is too heavy.
• Increase the value set to n8-55 (Load Inertia for PM).
• Increase the value set to n8-51 (Pull-In Current during Accel/Decel for PM).
• Reduce the load.
• Increase the motor or drive capacity.
Load inertia is too heavy.
Increase n8-55 (Load Inertia for PM).
Acceleration and deceleration times are too
short.
• Increase the acceleration and deceleration times (C1-01 through C1-08).
• Increase the S-curve acceleration and deceleration times (C2-01).
Digital Operator Display
Fault Name
UL3
Undertorque Detection 1
The current has fallen below the minimum value set for torque detection (L6-02) for longer than the
allowable time (L6-03).
Cause
Possible Solution
Parameter settings are not appropriate for the
type of load.
Check the settings of parameters L6-02 and L6-03.
There is a fault on the machine side.
Check the load for any problems.
6.4 Fault Detection
YASKAWA ELECTRIC SIEP C710606 18F YASKAWA AC Drive – V1000 Technical Manual
279
6
Troubleshooting