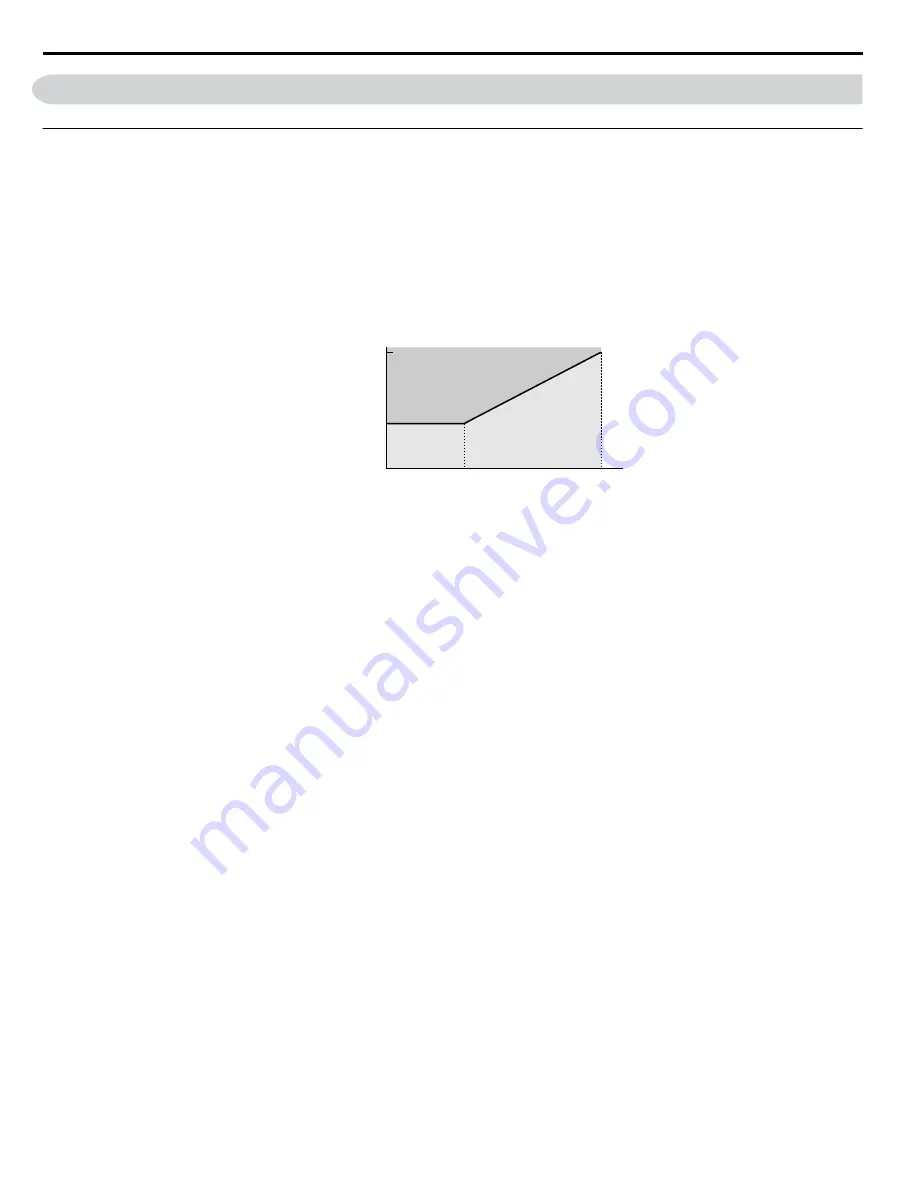
i.3
Application Precautions
u
General Application Precautions
n
Selecting a Reactor
An AC reactor or DC link choke can be used for the following:
• to suppress harmonic current.
• to smooth peak current that results from capacitor switching.
• when the power supply is above 600 kVA.
• when the drive is running from a power supply system with thyristor converters.
Note:
A DC link choke is built in to 200 V and 400 V class models with a capacity of 22 kW and higher (HD rating).
4000
600
0
60
400
Drive Capacity (kVA)
Power Supply
Capacity (kVA)
Power supply harmonics
reactor required
Reactor
unnecessary
Figure i.3 Installing a Reactor
n
Drive Capacity
Make sure that the motor rated current is less than the rated nameplate output current of the drive. When running more than
one motor in parallel from a single drive, the drive rated current should 1.1 times larger than the total motor rated current for
all connected motors or nuisance drive faults may occur.
n
Starting Torque
The overload rating of the drive determines the starting and accelerating characteristics of the motor. Expect lower running
torque than when running the motor from line power. To get more starting torque, use a larger drive or increase both the motor
and drive capacity.
n
Emergency/Fast Stop
During a drive fault condition, a protective circuit is activated and drive output is shut off. The motor may coast to a stop or
attempt to decelerate depending on parameter settings. If the emergency/fast stop cannot stop the load as fast as desired, a
customer-supplied mechanical brake may be required. Test emergency stop circuitry before putting drive into operation.
n
Options
The B1, B2, +1, +2, and +3 terminals are used to connect optional power devices. Connect only devices compatible with the
drive.
n
Repetitive Starting/Stopping
Applications with frequent starts and stops often exceed 150% of their rated current values. Heat stress generated from
repetitive high current can shorten the life span of the IGBTs. The expected lifetime for the IGBTs is about 8 million start and
stop cycles with a 4 kHz carrier frequency and a 150% peak current.
Yaskawa recommends lowering the carrier frequency, particularly when audible noise is not a concern. The user can also
choose to reduce the load, increase the acceleration and deceleration times, or switch to a larger drive. This will help keep
peak current levels under 150%. Be sure to check the peak current levels when starting and stopping repeatedly during the
initial test run, and make adjustments accordingly.
i.3 Application Precautions
18
YASKAWA ELECTRIC SIEP C710606 18F YASKAWA AC Drive – V1000 Technical Manual