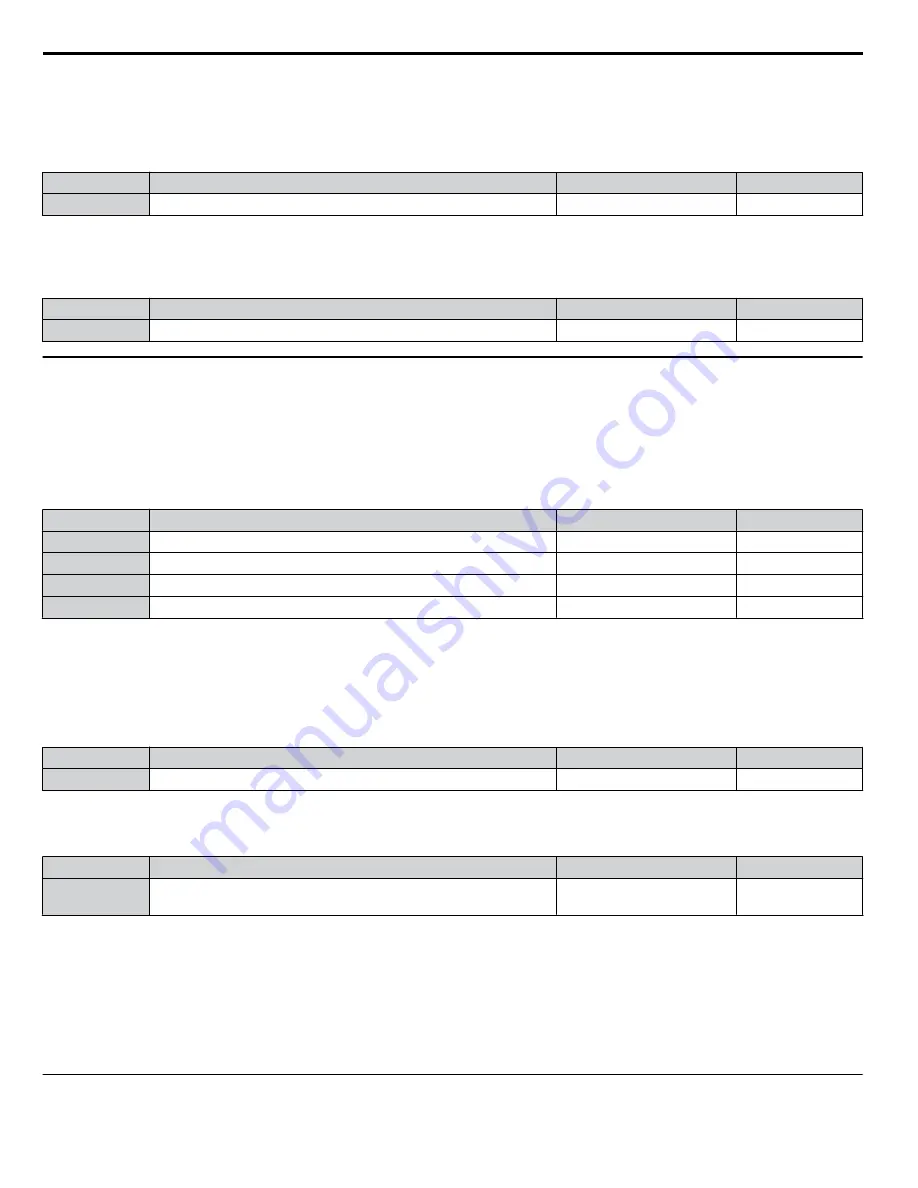
The value is set as a percentage of the maximum frequency. If L6-08 is set for unsigned speed detection (L6-08 = 2, 4, 6, 8)
then the absolute value of L6-09 is used, i.e., negative settings will be treated as positive.
n
L6-10: Mechanical Weakening Detection Time
Sets the time permitted for the situation selected in parameter L6-08 to arise before mechanical weakening is detected.
No.
Name
Setting Range
Default
L6-10
Mechanical Weakening Detection Time
0.0 to 10.0 s
0.1 s
n
L6-11: Mechanical Weakening Detection Start Time
Sets the drives cumulative operation time at which mechanical weakening detection is activated. If U4-01 reaches the L6-11
value, the function is activated.
No.
Name
Setting Range
Default
L6-11
Mechanical Weakening Detection Start Time
0 to 65535 h
0 h
u
L7: Torque Limit
The torque limit function can be used to limit the torque in each of the four quadrants individually and thereby protect the
machinery. It can be used in the Open Loop Vector Control mode. A digital output programmed for “During Torque Limit”
(H2-01/02/03 = 30) can be switched when the drive is operating at the torque limit.
n
L7-01/02/03/04: Torque Limits
These parameters set the torque limits in each operation mode.
No.
Name
Setting Range
Default
L7-01
Forward Torque Limit
0 to 300%
200%
L7-02
Reverse Torque Limit
0 to 300%
200%
L7-03
Forward Regenerative Torque Limit
0 to 300%
200%
L7-04
Reverse Regenerative Torque Limit
0 to 300%
200%
Note:
If the multi-function analog input is programmed for “10: Positive Torque Limit”, “11: Negative Torque Limit”, “12: Regenerative Torque
Limit”, or “15: General Torque Limit”, the drive uses the lower value of either L7-01 through L7-04, or analog input torque limit.
to Setting 10/11/12/15: Positive/Negative/Regenerative/General Torque Limit (OLV only) on page 209
for details on using analog torque
limits.
n
L7-06: Torque Limit Integral Time Constant
Sets the integral time constant for the torque limit function.
No.
Name
Setting Range
Default
L7-06
Torque Limit Integral Time Constant
5 to 10000 ms
200 ms
n
L7-07: Torque Limit Control Method Selection during Accel/Decel
Selects the function of torque limit during acceleration and deceleration.
No.
Name
Setting Range
Default
L7-07
Torque Limit Control Method Selection during Acceleration/
Deceleration
0 or 1
0
Setting 0: Proportional Control
The torque limit function works with P-control during acceleration and deceleration and switches to I-control at constant speed.
Use this setting when acceleration or deceleration to the desired speed has priority over torque limitation during speed changes.
Setting 1: Integral Control
The torque limit function always uses I-control. Use this setting when high accuracy torque limitation is required even during
speed changes. Using this function may increase the acceleration time, or may prevent the motor speed from reaching the
frequency reference when the torque limit is reached before.
u
L8: Hardware Protection
5.8 L: Protection Functions
234
YASKAWA ELECTRIC SIEP C710606 18F YASKAWA AC Drive – V1000 Technical Manual